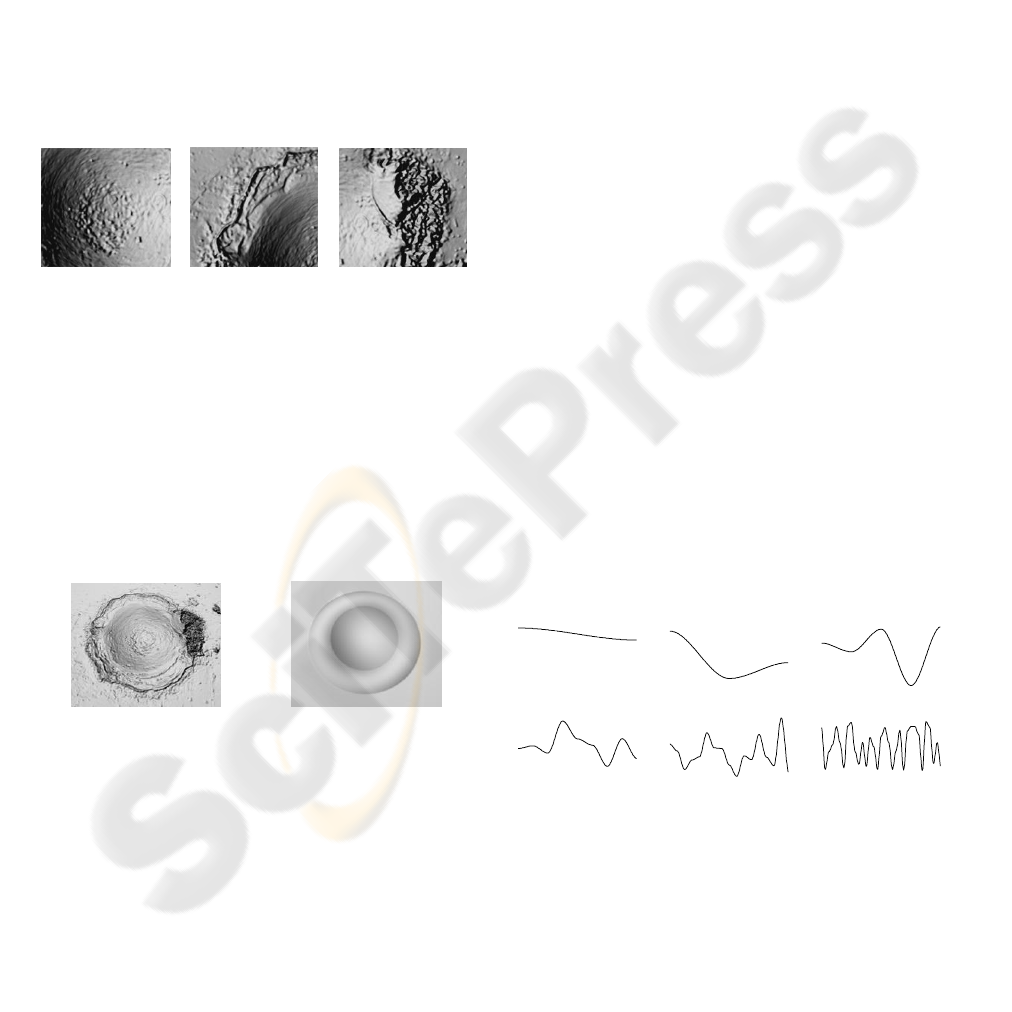
laser pulses burned into a single point in steel) in 3D
view can be seen in Figure 3a.
The central part of the pulse (i.e., the area
directly irradiated by the laser beam) is smooth and
the bottom of the pit is a little bit rougher (Figure
2a). The most ragged surface part is the transition
ring. The surface is modulated by some concentric
waves that are both regular and irregular (Figure 2b).
Sometimes, local defects with a considerable
roughness can appear, especially at the outer border
of the transition ring (Figure 2c). At the outer
border, the roughness declines slowly and fades into
the roughness of the bulk material. All these facts
should be taken into account if we want to generate
a realistically looking surface of a laser-burned
sample.
a) b) c)
Figure 2: Examples from different parts of a typical
sample surface.
1.2 Sample Shape Approximation
As described in (Hájková, 2009), the basic shape of
a sample can be approximated by a smooth surface
defined by mathematical functions which
approximate the pulse pit by an elliptical paraboloid,
and the pulse transition ring by the top half of a
parabolic elliptic torus. An example of a real sample
and its approximation can be seen in Figure 3.
a) b)
Figure 3: An example of the sample approximation by a
smooth surface.
To obtain the most realistically looking sample,
surface the generated surface should be further
modified and some roughness should be added.
2 ROUGHNESS GENERATION
If we burn the same sample twice into different
places, it will never be the same, because at least the
surface of the basic material differs. That is why we
have to enhance the sample generation with random
features such as noise or various defects to get more
realistic results. These features and the methods how
to generate them are described in the following
subsections.
2.1 Perlin Noise Function
As can be seen in Figure 3, the mathematically
generated sample is too smooth in comparison with
the real one. That is why it is necessary to modify a
generated surface by some kind of artificial defects
that would represent the granularity of the material
and the roughness of different parts of a real sample.
One of the possible solutions is to use the Perlin
noise function (Perlin 1985), (Perlin, 2002). The
Perlin noise function has a very wide range of
application, not only in the computer graphics, but
also in many other areas, where natural appearance
is required.
Perlin noise combines a noise function with an
interpolation function. The noise is formed by
randomly generated values the distance of which is
given by some frequency. This frequency is defined
as 1/wavelength, where the wavelength represents
the distance from one generated value to the next
one. The generated values are interpolated using the
Hermit interpolation (Žára et al., 2005) to get a
smooth interpolating curve (with given amplitude
and frequency). If we sum up several curves (called
octaves) with various frequencies and amplitudes,
we get the final Perlin noise function. An example of
1D octaves can be seen in Figure 4. The frequency
ranges from 1 to 32, the amplitude is the same for all
octaves.
Figure 4: Octaves that are added to the final 1D Perlin
noise with the same amplitude and different frequencies:
a) 1, b) 2, c) 4, d) 8, e) 16, f) 32.
For the modification of the generated smooth
material surface, we need the 2D Perlin noise. A
different number of octaves can be added into the
final 2D noise or various amplitudes can be used.
Several examples of the final 2D Perlin noise are
shown in Figure 5.
ICSOFT 2009 - 4th International Conference on Software and Data Technologies
284