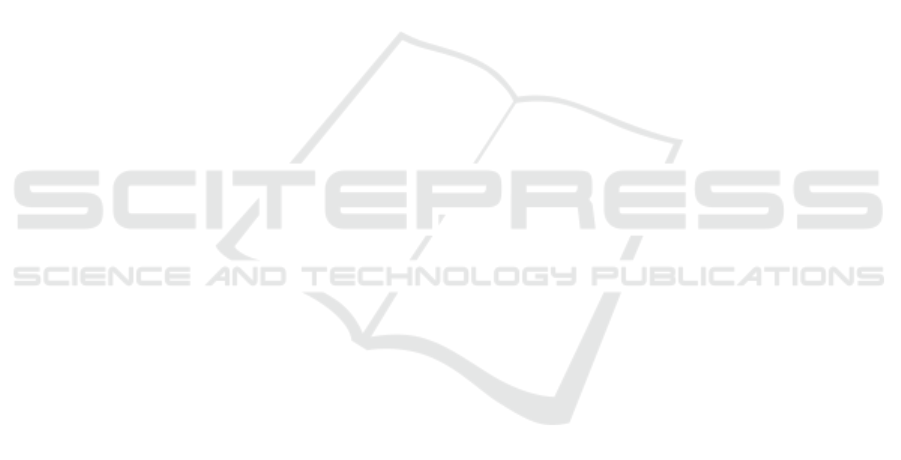
with each other is not true. Therefore, using the multi-
hop capability of modern wireless sensor networks is
a good way to extend the range of the sensors and the
CTU’s communication system.
Sensor Data Memory. Sensor data is important for
decision making of the control algorithms. There-
fore, it needs to be protected from communication
and sensor node failures. For industrial environments
WirelessHART (HART Communication Foundation,
2007) is a standardized protocol for reliable wireless
communication and can be used in the proposed trans-
fer station scenario. It provides robust self-organizing
and self healing mechanisms to encounter communi-
cation failures. But networked sensors have far more
potential, in a cognitive system they can be used as
distributed observers. A distributed observer is a sen-
sor with its own memory that stores a snapshot of
the past. It is similar to the human short-term mem-
ory (with low-capacity) and is used in many cognitive
modelling architectures (Laird et al., 1987) (Anderson
and Lebiere, 1998). This kind of sensors can answer
questions about situations of a larger context, which
is usful for coordination and optimization purposes.
Distributed sensors have an area to observe. For ex-
ample, a fixed sensor knows about the robot traffic in
his area and can therefore give a usage estimation of
the path belonging to his observation area. Techni-
cally, sensors now have to store their data instead of
just sending real-time data to the CTUs. The CTUs
then ask the sensors for certain events in their stored
history snapshot. For fault-tolerance reasons, sensors
are allowed to replicate their data to other fixed or mo-
bile sensors. They can use different replication strate-
gies to trade-off data availability for energy and vice
versa.
7 CONCLUSIONS AND FUTURE
WORK
Present state-of-the-art projects were considered as
too domain specific and not able to raise the flexibil-
ity of logistic systems comprehensively. Therefore,
this paper proposed modular principle that raises the
flexibility of the system. Energy is an important fac-
tor for battery driven autonomous robots, therefore
strategies for the trade-off between energy consump-
tion and timelines were discussed. Furthermore, a
unified sensor integration scheme was proposed that
raises the cognitive perception ability of the whole lo-
gistic system and a sensor data concept that enables
the idea of a distributed observer was shown. At the
moment the proposed models are being implemented
and in a next step they will be simulated. The goal
of the simulation is to find the best granularity of the
modularization and to find the best cooperating strate-
gies for autonomous logistic systems. As a next step
a test bed implementing figure 2 for validation of the
chosen strategies will be created.
REFERENCES
Anderson, J. R. and Lebiere, C. (1998). The Atomic Com-
ponents of Thought. Lea.
Baur, T., Sch
¨
onung, F., Stoll, T., and Furmans, K.
(2008). Formationsfahrt von mobilen, autonomen und
kooperierenden Materialflusselementen zum Trans-
port eines Ladungstr
¨
agers. Fachkolloquium der Wis-
senschaftlichen Gesellschaft f
¨
ur Technische Logistik e.
V., 4.
Guizzo, E. (2008). Three engineers, hundreds of robots, one
warehouse. IEEE Spectrum:, pages 26–34.
G
¨
unthner et al. (2008a). Vom Prozess zum Ereignis - ein
neuer Denkansatz in der Logistik. In Jahrbuch Logis-
tik, pages 224–228.
G
¨
unthner, W. A., Durchholz, J., Kraul, R., and Schnei-
der, O. (2008b). Technologie f
¨
ur die Logistik des 21.
Jahrhunderts. In Kongressband zum 25. Deutschen
Logistik-Kongress, pages 360–393.
HART Communication Foundation (2007). WirelessHART
Technical Datasheet. HART Communication Founda-
tion, 1.0b edition.
Laird, J. E., Newell, A., and Rosenbloom, P. S. (1987).
Soar: An architecture for general intelligence. Artif.
Intell., 33(1):1–64.
Overmeyer, L., Falkenberg, S., Heiserich, G., and Jungk, A.
(2007). Innovative Gestaltung von Intralogistik durch
Kopplung kleinskaliger Systeme. In 16. Deutscher
Materialfluss-Kongress, pages 171–179.
Riedmaier, S. (2008). Neue M
¨
oglichkeiten f
¨
ur Schmal-
gangstapler. Hebezeuge F
¨
ordermittel, 12:762–763.
Robotics, S. (2005). Na, Servus! Automation, 6.
Scholz-Reiter, B., Jagalski, T., and Bendul, J. (2007a).
Bienenalgorithmen zur Selbststeuerung logistischer
Prozesse. Industrie Management, pages 7–10.
Scholz-Reiter, B., Jagalski, T., and de Beer, C. (2007b).
Selbststeuerung logistischer Prozesse in Produktion-
snetzen. Industrie Management, pages 19–22.
Scholz-Reiter, B., Rekersbrink, H., and Freitag, M. (2006).
Kooperierende Routingprotokolle zur Selbssteuerung
von Transportprozessen. Industrie Management, 22.
Servus Robotics (2006). Wie von Geisterhand. Automation,
4.
Windth, K. (2006). Selbststeuerung intelligenter Objekte in
der Logistik.
Wurman, P. R., R., R. D., and Mountz, M. (2008). Coordi-
nating hundreds of cooperative, autonomous vehicles
in warehouses. AI Magazine, 29/1:9–19.
A SYSTEM-ARCHITECTURE FOR ROBOTIC MOVEMENTS OF GOODS - Approaches Towards a Cognitive Material
Flow System
347