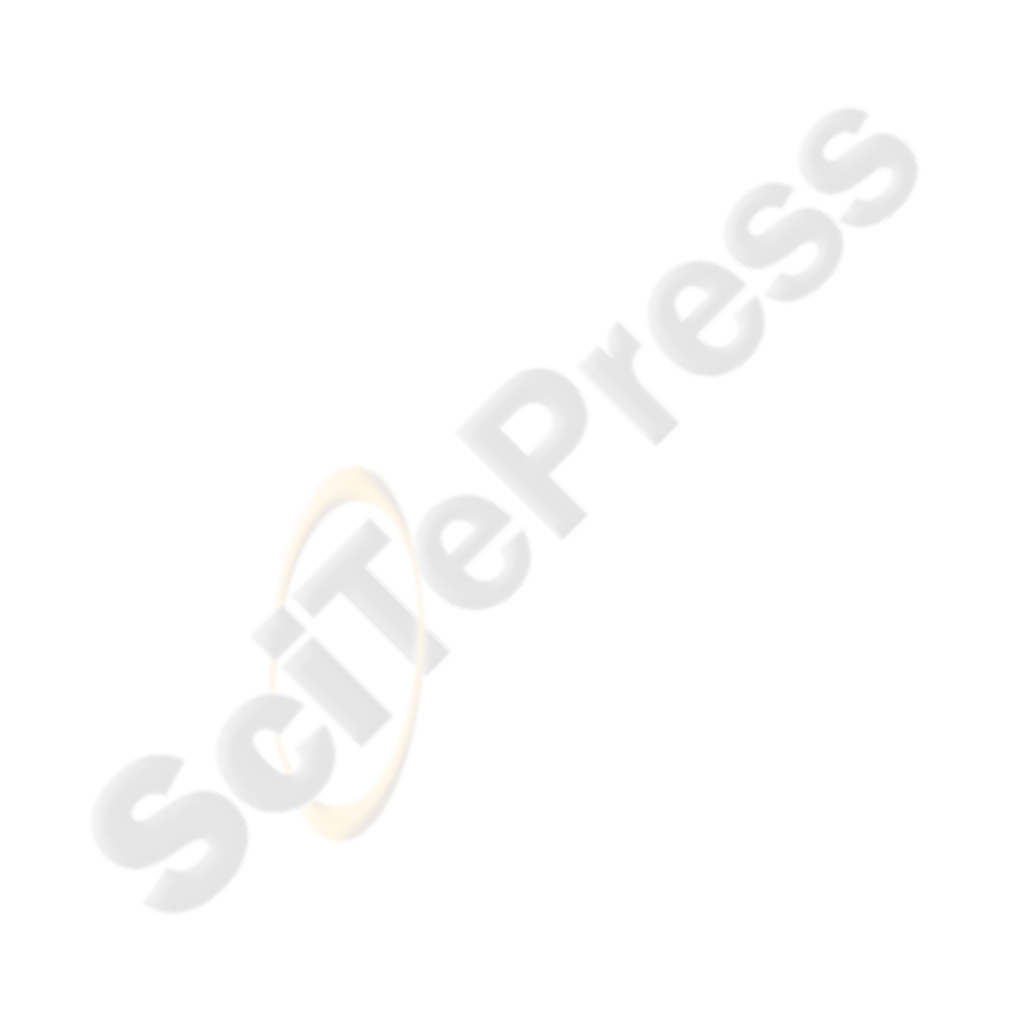
team is often numerous due to the complexity of the
product as their knowledge is desirable in diverse
aspects of design:
at selection of material, tool, production
process, etc.,
at performance of analyses and simulations, at
their evaluation, and consequentially, design
modifications,
at Design for X, where X resembles the
appropriateness for manufacturing,
maintenance, service, etc. (Huang, 1996).
Experts’ cognition is a support to designer
during processing though the four phases of design:
task clarification, conceptual design, embodiment
design, and detail design. More developed and well-
provided enterprises are in better position in
correspondence to Small and Medium-sized
Enterprises (SME’s), whose economic status does
not enables hiring an expert to cover a specific
design aspect.
3 PLASTIC PRODUCTS’ DESIGN
PROCESS
3.1 Current State Analysis
Engineer’s contribution to a design results as a
functional and user friendly finished product,
meaning an ergonomic and aesthetic product,
supported by adequate technical background. In
enterprises, it is a common practice to divide a
product development process into two parts:
ergonomic and aesthetic design, where the
outer surface is designed by industrial
engineer (Gordon, 2003),
functional design, where all technical criteria,
along with requirements and conditions, are
considered, and the process is performed by
design engineer
This article is oriented into functional design,
where the material selection phase is of supreme
importance, therefore the ergonomic (Kaljun and
Dolšak, 2006) and aesthetic values, although their
contribution is not marginal, are not discussed here.
After research was made in several Slovenian
world-class enterprises involved in plastic products’
manufacturing, the conclusions were unexpected but
also reasonable. What is obvious, the material
selection within a new product development, can be
characterized as Selection by Synthesis (Ashby and
Johnson, 2005) where design requirements appear in
the form of intentions, features, and perceptions.
This method is used, when knowledge of the solved
cases can be exploited and transferred to other
products with some features in common. In other
words, the product with the same significant
attributes can be used as a template. Preconceptions
about the material used may be logical in some
cases, as also the shortcut to the solution, however,
the creativity and innovation are degraded here.
Figure 1 illustrates the product development
process resembling the situation in most enterprises
included in this study. Design engineers have expert
knowledge about some particular materials,
extensively applied in the industry, in which the
company participates. Thus, the preliminary material
selection is a decision without irresolution.
The design process starts with the outer design
introduced by various 3D computer models
performed by an industrial designer. Computer
models are supported by 3D prime models produced
using rapid prototyping, with the aim of evaluating
the ergonomic and aesthetic design of the product.
After adjustments, the most appropriate variant gets
the experts’ approval so the product progresses into
the most complex and time consuming phase,
functional design. The design engineer studies the
design requirements consisting of technical criteria,
safety requirements and the wishes of the
management. The completed product design can
again be represented by a rapid prototyping prime
model in the form of a completely functional
exemplar, often made of the material resembling the
preliminary selected material for the finished
product. Due to this fact, the testing and measuring
is possible and any necessary adjustment can be
performed accordingly. At this point of the design
process, the designer usually provides a modification
of the material based on past experiences in plastics’
design. The next step includes casting simulation
upgraded with appropriate production process
selection and tool design, where technical
parameters should be defined by considering the
selected material. Casting simulation is repeated
until the design engineer approves the production
appropriate solution.
From Figure 1 it can also be acknowledged that
without preconceptions about material selection, the
material could be modified more than once
throughout the product development process, as new
information about the product appears at every phase
of design.
KEOD 2009 - International Conference on Knowledge Engineering and Ontology Development
124