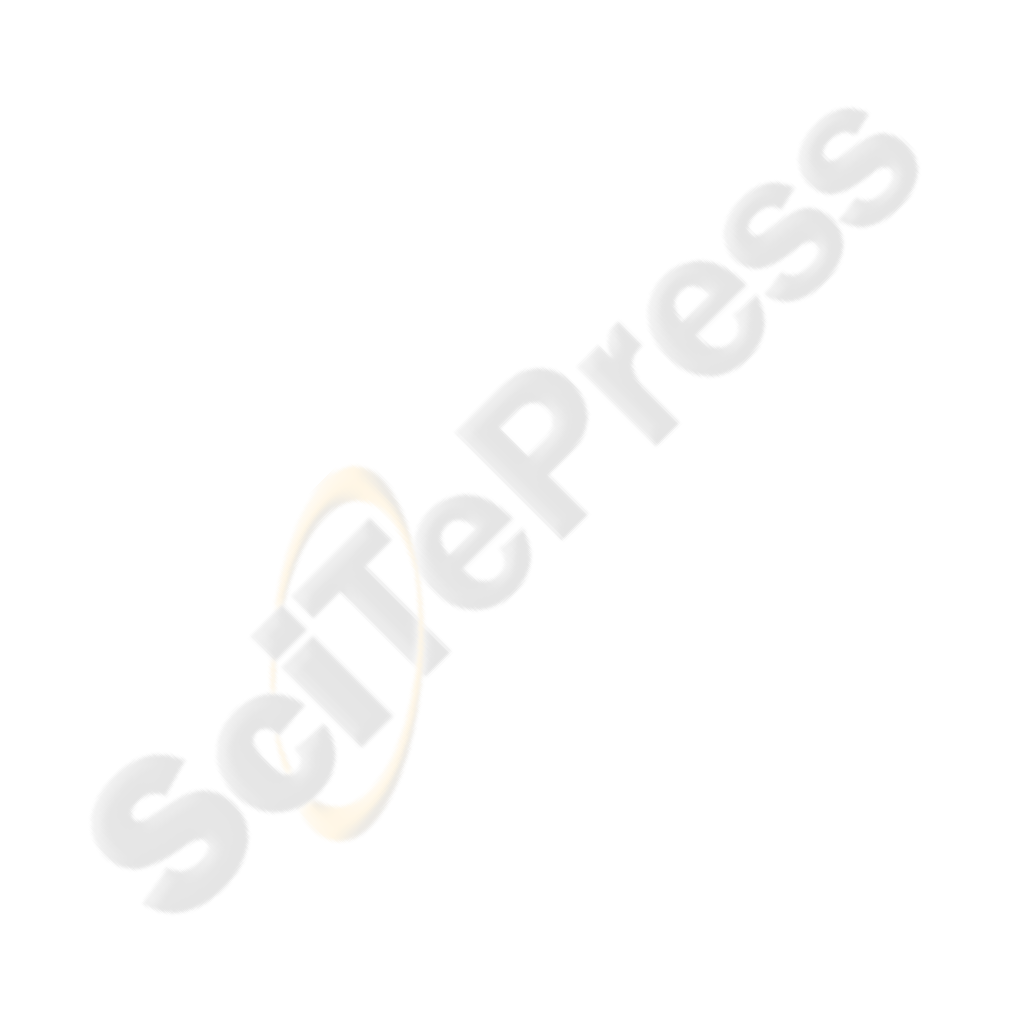
6 CONCLUSIONS
Structural analysis-based design optimisation is a
part of development process for almost every new
product. Thus, it has very important role in
nowadays high-tech world, where only optimal
solutions can win the game on the market. However,
development of the optimal analysis proven design
solutions is very complex domain, which cannot be
treated adequately by using the conventional CAD
tools, unless the user is possessed of special skills
and experience. The main reason for that lies in the
fact that the present CAD tools are still mainly
mathematically oriented and are not able to provide
an adequate expert advice when some crucial
decisions in product development process need to be
made.
On the other hand, advanced computing
applications are changing the way in which
designers interact with computers. Knowledge
representation formalisms and advanced reasoning
techniques are no longer the sole territory of AI
community. New approaches have earned
acceptance in design sphere and have started to
emerge in commercial software.
For this reason, many research activities are
oriented in making analysis-based design
optimisation process more intelligent and less
experience-dependent (Chapman and Pinfold, 2001).
Many experts share the opinion that it can be done
by supplementing the existing CAD systems with
some intelligent modules that will provide advice
when needed.
The intelligent modules discussed here represent
some crucial parts of the overall design optimisation
cycle, where in addition to the structural analysis,
some other design aspects, such as for example the
ergonomics and aesthetics of the product (Kaljun
and Dolšak, 2006) also play an important role.
The intelligent analytical aids in design that are
presented in this paper have already proved to be
very useful in the university education as well as in
engineering practice. Some practical examples
demonstrating the use of intelligent decision support
in FEA-based design optimisation process are
presented in references that are listed for each
intelligent module discussed in this paper.
REFERENCES
Chapman, C., Pinfold, M., 2001. The Application of a
Knowledge Based Engineering Approach to the Rapid
Design and Analysis of an Automotive Structure. In
Advances in Engineering Software, 32, 903-912.
Clarkson, J., Eckert, C. (eds.), 2005. Design Process
Improvement - a Review of Current Practice. Springer.
Dolšak, B., 2002. Finite Element Mesh Design Expert
System. In Knowledge-based Systems, 15, 315-322.
Dolšak, B., Bratko, I., Jezernik, A., 1998. Knowledge
Base for Finite Element Mesh Design learned by
Inductive Logic Programming. In Artificial
Intelligence in Engineering Design, Analysis and
Manufacturing, 12, 95-106.
Gero, J.S. (ed.), 2002. Artificial Intelligence in Design '02.
Springer.
Kaljun, J., Dolšak, B., 2006. Computer Aided Intelligent
Support to Aesthetic and Ergonomic Design. In
WSEAS Transactions on Information Science and
Applications, 3 (2), 315-321.
Mili, F., Shen, W., Martinez, I., Noel, P., Ram, M.,
Zouras, E., 2001. Knowledge Modeling for Design
Decisions. In Artificial Intelligence in Engineering,
15, 153-164.
Novak, M., Dolšak, B., 2008. Intelligent FEA-based
Design Improvement. Engineering Applications of
Artificial Intelligence, 21 (8), 1239- 1254.
Novak, M., Dolšak, B., 2006. Intelligent Computer-aided
Structural Analysis-based Design Optimisation. In
WSEAS Transactions on Information Science and
Applications, 3 (2), 307-314.
Novak, M., Rieg, F., Dolšak, B., Hackenschmidt, R.,
2006. Intelligent Support to Finite Element Type
Selection. In WSEAS Transactions on Information
Science and Applications, 3 (9), 1617-1624.
Ong, Y.S, Keane, A.J., 2002. A Domain Knowledge
Based Search Advisor for Design Problem solving
Environments. In Engineering Applications of AI, 15,
105-116.
Pinfold, M., Chapman, C., 2004. Using Knowledge Based
Engineering to Automate the Post-processing of FEA
Results. In International Journal Computer
Applications in Technology, 21 (3), 99-106.
Rieg, F., 2006. Z88 – The Compact Finite Element
System, version 12.0. In Chair for Engineering Design
and CAD, University of Bayreuth, Germany.
Rieg, F., Koch, F., 2001. Selection of Finite Elements
Considering Loadcases and Geometry. Design
Methods for Performance and Sustainability. In
Proceedings of the int. conference on Engineering
Design, Glasgow, 107-114.
Turban, E., Aronson, J.E., Liang, T.P., 2004. Decision
Support Systems and Intelligent Systems. Prentice
Hall. 7th edition.
Zienkiewicz, O.C., Taylor, R.L., Shu, J.Z., 2005. The
Finite Element Method: Its Basis and Fundamentals.
Butterworth-Heinemann. 6th edition.
KEOD 2009 - International Conference on Knowledge Engineering and Ontology Development
134