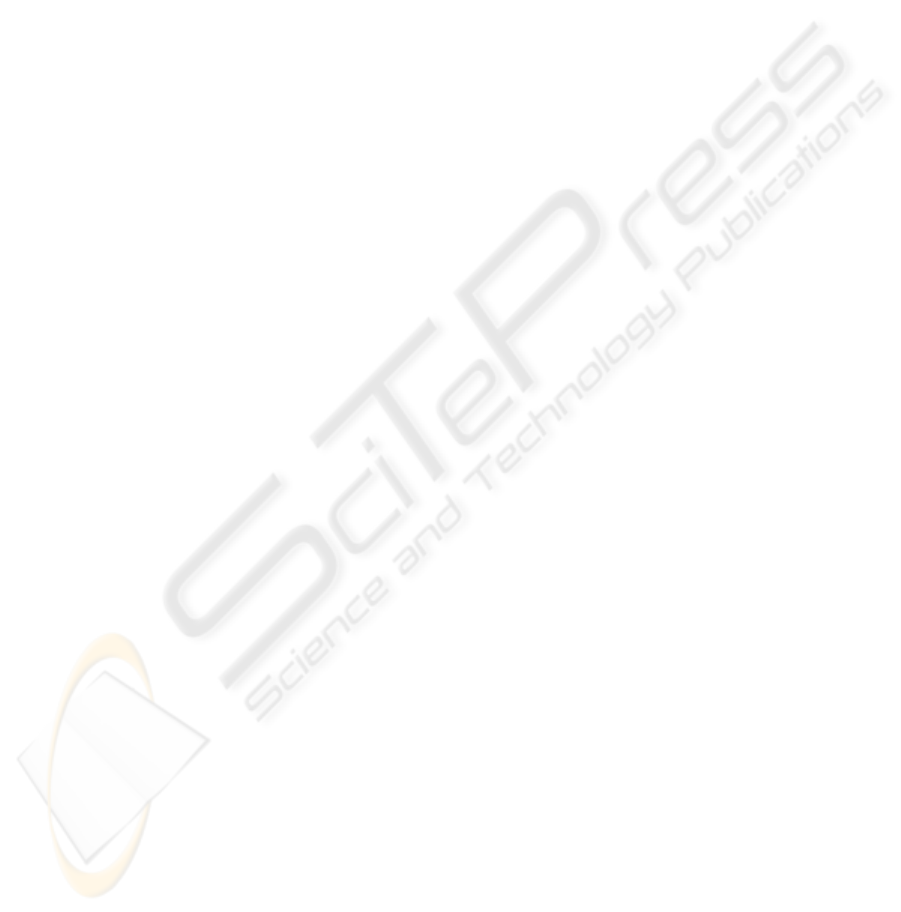
manually by appropriate engineers based on their
implied knowledge. Afterwards, another iteration
loop of production-oriented analysis must be
executed in order to ensure technologically
manufacturability of the particular component. This
iterative process is then executed for each action
alternatives. In doing so, multiple iterations can be
performed until a proper solution is available.
Therewith, possible resource configurations are the
result of the proposed method, which ensures the
manufacturability of a product component at an
existing production system.
4.4 Application Scenario
The following paragraph describes an application
scenario of the introduced validation method. The
main application is to support the product
development process when developing a new car
that should be manufactured on an existing
production line. In the context of this challenge the
validation method can be applied for continuous
validation of the product specification thorough the
different phases of the product lifecycle.
The core of the framework is the validation
method that is executed in the frame of a validation
procedure. In case that the validation procedure is
positive, the new developed product can be
manufactured on the existing production line. In
case the result is negative, an engineer needs to
change either the product design or the production
resources. At this the validation tool suggests the
possible action alternatives.
To react accordingly on changing requirements
from the production planning, the product
specification needs to be validated iteratively
through the whole product development process.
With the progress of the product development
process the product design gets more mature and
more information can be regarded for the validation.
In the early stages of the development process the
materials are specified. Already at this point of the
development process the engineer should check if
the product materials can be joined using the
technology on the production line.
Later in the development process the product
geometry, joints, functions are defined. These are
the base for further validations (i.e. accessibility
checks). At this point the validation can be done
either by using internal validation methods or using
external ones.
5 CONCLUSIONS
Due to an increasing customer-individualisation and
the growing complexity of the production systems
the integration of new products on existing
production facilities is getting more important. This
work presents an integrated method for validation if
a product component can be manufactured on a
given production line. This is performed by
modeling and evaluating the respective product,
resource and process informaion based on
knowledge engineering techniques. The application
of this method in the industry ensures time reduction
between introducing a new product to the market
and also creates an important improvement of the
decision security for all responsible personnel.
ACKNOWLEDGEMENTS
The authors wish to acknowledge their appreciation
to the European Commission that partially funded
the project and to all the MyCar project partners for
their valuable cooperation and contribution.
REFERENCES
Weyand, L., Bley, H., Kaiser, J.-M., Meißner, R., Bär, T.
2008. Production Oriented Design-Check in Car
Manufacturing – Not Only a Question of Powerful
Validation Tools. In: Intelligent Computation in
Manufacturing Engineering, 6th Conference, Neapel.
Pahl G, Beitz W, Feldhusen J, Grote K-H (2007):
Konstruktionslehre Grundlagen erfolgreicher
Entwicklung. Methoden und Anwendungen, Springer
Verlag. Berlin Heidelberg New York, 7
th
Edition.
Müller, M., 2007. Reifegradbasierte Optimierung von
Entwicklungsprozessen – am besonderen Beispiel der
produktionsbezogenen Produktabsicherung. In: Bley
H, Weber C (eds.) Schriftenreihe Produktionstechnik.
Saarland University, Saarland.
Svensson, D., Malmström, J., Pikosz, P., Malmqvist, J.: A
Framework for Modelling and Analysis of
Engineering Information Systems. Proceedings of
ASME DETC ‘99, 1999. Las Vegas, USA.
Burr, H., Müller, M., Vielhaber, M., 2007. EIMS – A
framework for engineering process analysis. In:
Proceedings of the International Conference on
Engineering Design, ICED ’07, Paris.
Winston, P. H., 1993. Artificial intelligence, Addison-
Wesley Reading. 1
st
Edition.
Puppe, F., 1991. Einführung in Expertensysteme, Springer
Verlag. Berlin Heidelberg, 1
st
Edition.
Gottlob, G., Frühwirt, T., Horn, W., 1990. Experten-
systeme, Springer Verlag. Wien, 1
st
Edition.
KEOD 2009 - International Conference on Knowledge Engineering and Ontology Development
170