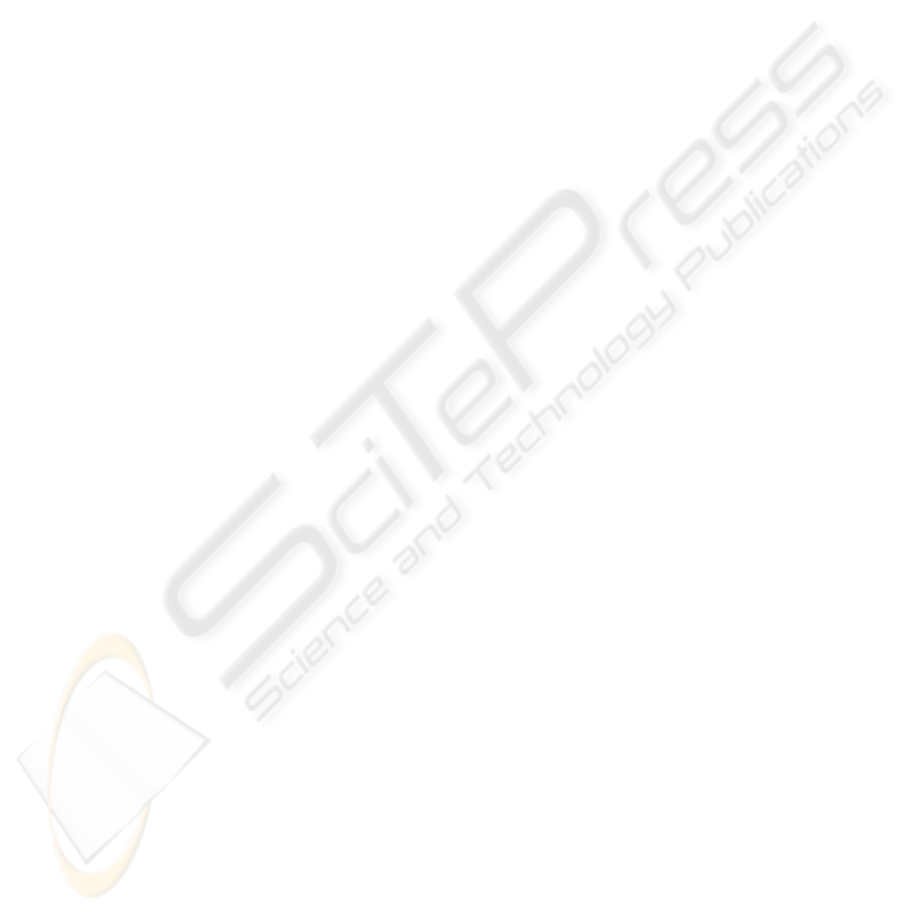
nection between the outputs of the controlled system
and its inputs. The control being carried out without
any feedback, it only depends on the model within
the controller itself. The second kind of control is a
closed loop, which is focused on the feedback, allow-
ing the control system to make actions on the inputs
by knowing the system’s outputs. In those two cases,
the function determiningthe control to apply is named
the control law. The control system presented here is
designed as a closed loop.
2.1 PID Control
Currently, the most widespread approach to control
bioprocesses is the Proportional-Integral-Derivative
(PID) controller. Controlling with such a tool means
that three different functions will be applied to the re-
ceived feedback, in order to select the adequate con-
trol. These functions are i) the proportional, which
computes the current error multiplied by a “propor-
tional constant”, ii) the integral, which takes into ac-
count the duration and magnitude of the error, by
summing their integral and multiplying by an “inte-
gral constant” and finally iii) the derivative, which es-
timates the rate of change of this error, allows to ob-
serve its variation, and multiplies it by a “derivative
constant”. These three functions are then summed.
However,several points need to be treated to make
this approach adaptive enough to follow the biopro-
cess dynamics; the different constants appearing in
the formulas have still to be defined and a way to al-
low them to be adjusted during the bioprocess has to
be found. Such a modification may be done by using
methods like Ziegler-Nichols (Ziegler and Nichols,
1942) or Cohen-Coon (Cohen and Coon, 1953).
This PID approach is quite generic, and can be ap-
plied to a wide range of control systems. However, its
performances in non-linear systems are inconsistent.
This drawback led to the hybridization of this method
by adding mechanisms relying on fuzzy logic (Visi-
oli, 2001), or artificial neural networks (Scott et al.,
1992).
2.2 Adaptive Control
The differences existing in the results coming from
distinct runs of the same bioprocess led us to study the
field of adaptive control; these differences are for ex-
ample a noise addition or a delay in the chemical reac-
tions that modify the system dynamics. This problem
can be overcome by applying methods that dynami-
cally modify the control law of the controller.
There are mainly three different categories of
adaptive controller, the Model Identification Adaptive
Control (MIAC), the Model Reference Adaptive Con-
trol (MRAC), and the Dual Control.
MIAC systems (Astrom and Wittenmark, 1994)
use model identification mechanisms in order to en-
able the controller to create a model of the system
it controls. This model can be created from scratch
thanks to the observed data, or by using an already
known basis. The identification mechanism updates
the model using values coming from inputs and out-
puts of the controlled system.
MRAC systems, suggested by (H.P. Whitaker and
Kezer, 1958), employ a closed loop approach modi-
fying the parameters of the controller thanks to one
or several reference models. This time, the system
does not create a model of the bioprocess, but it uses
an existing model to update the control law by ob-
serving the difference between the predicted output
and the measured ones. This adjustment is generally
applied by the use of the MIT rule (Kaufman et al.,
1994), which is a kind of gradient descent minimiz-
ing a performance criterion computed from the error
measured.
The last system is called Dual Controller (Feld-
baum, 1961) and is especially useful for controlling
an unknown system. In fact, such a control system
uses two kinds of actions, the first one is a normal con-
trol, which aims at leading the system toward a certain
value, while the other one is a probing action, which
allows the controller to obtain more information on
the controlled system by observing its reaction. The
difference here is that the probing action is physically
applied on the system, and not only predicted by the
use of a model.
2.3 Intelligent Control
The last kind of controller is a subtype of the adap-
tive control, called intelligent control. It focuses on
the use of methods coming from artificial intelligence
to overcome problems linked to non-linearity and dy-
namic systems.
In the case of bioprocess control, the most used
intelligent controller is the artificial neural network
(ANN). Initially applied to bioprocesses to infer some
non-measurable variables, it was then used to control
such processes, or to improve already existing control
methods by providing adaptation. Furthermore, ANN
appear in pattern recognition control such as (Megan
and Cooper, 1992).
Unfortunately, the black box aspect of ANN is a
limit to their use in the bioprocess control. And even
if some works exist to reduce this aspect (Silva et al.,
2000), it is to the detriment of their adaptability.
Among the Artificial Intelligence techniques used
SELF-ADAPTIVE MULTI-AGENT SYSTEM FOR SELF-REGULATING REAL-TIME PROCESS - Preliminary Study
in Bioprocess Control
31