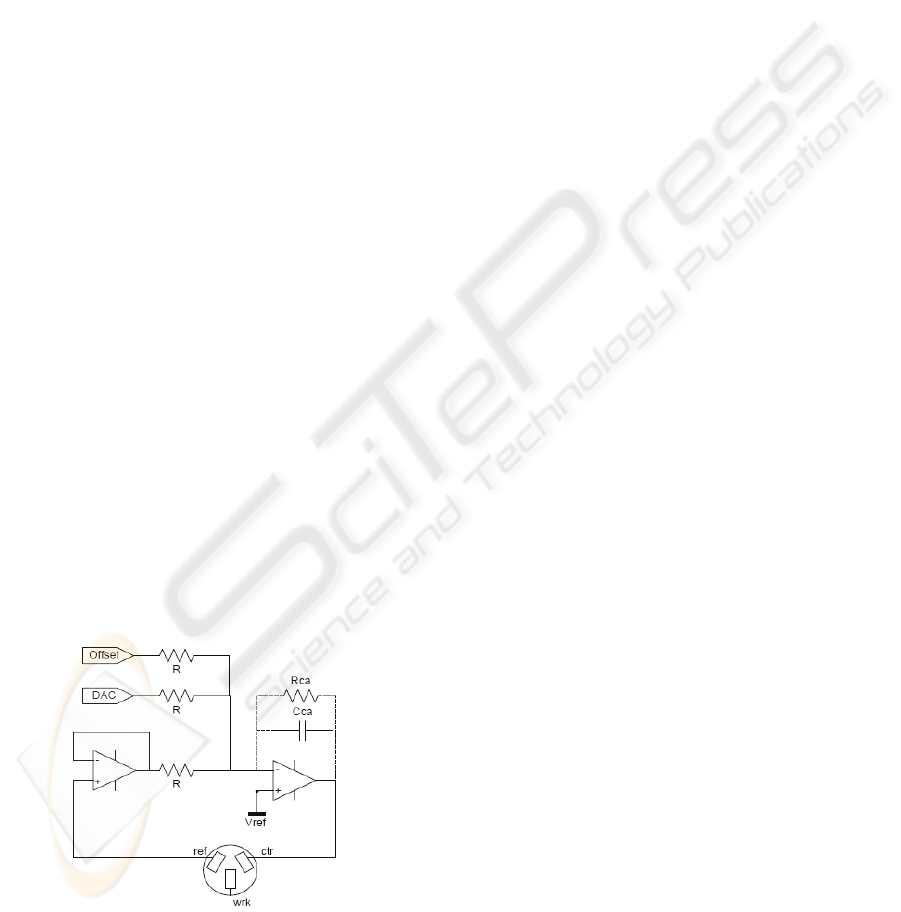
process has been proven and confirmed over a
substantial number of lots. The large geometry is
considered acceptable as speed is not an issue in
sensor applications and the process is more than
sufficient to push out the limits of sensitivity. The
fabricated die has 56 pads and a size of 8x10 mm.
However this is, after all, a development tool so this
should not be a major concern. Many of the larger
components will be redundant and trimming
techniques can be used to reduce the die size.
4 IMPLEMENTATION
The on-chip sensing system interfaces to a three-
electrode cell comprising a working electrode, a
reference electrode and a counter electrode, as
described above. The device was implemented on
the silicon breadboard described using four of the
amplifiers in the array along with a number of
resistive elements. The amplifiers are two-stage
devices using a P-input CMOS format. The design
provides a slew rate of 1V/µs, an open loop voltage
gain of 80 dB and a closed loop bandwidth of 10
kHz while maintaining an offset voltage of less than
±2.5mV. The resistive elements are created from a
combination of poly connect strips and the arrays
resistive segments.
A specific requirement is the necessity of an
enhanced dynamic range due to the differences in
concentrations of target analytes in biological
samples and the natural variations amongst patients
and samples, which results in a widely varying
sensor signal. The potentiostat, Figure 3, provides an
exact replication of the applied signal from the
digital to analogue converter (DAC) at the reference
electrode, due to the feedback via the conducting
biological sample solution.
Figure 3: Potentiostat sensor control circuit with input
stimulus voltage from DAC and connections to sensor.
The main problem in the design is to ensure
system stability under the conditions of a high
capacitive load from the working electrode. To
ensure a stable device a provision is made to add a
bandwidth reducing capacitance (C
ca
, dotted
interconnect) to the feedback path of the control
amplifier. Also a bias compensation resistance can
be added external to the IC. These components
could easily be integrated into the device once their
values are optimised.
A system reference voltage can be applied to the
control amplifier non-inverting terminal. Equally
the amplifier terminal can be grounded and an offset
voltage can be applied in adder configuration with
the DAC stimulus voltage. The value of the
resistance R is not critical so long as the three
resistors are well matched; 4.7 kΩ was selected as it
was most convenient for the process. The function
of the buffer amplifier at the reference electrode was
to eliminate any current flowing through the
electrode resulting in a more stable reference for the
cell and a more accurate measurement (without
offset). The control amplifier can provide a sink or
source of 3.5mA for the cell.
The transimpedance amplifier element of the
device acquires the cell current from the working
electrode and converts it to a corresponding voltage,
V
out
, as illustrated in Figure 4. A significant
challenge for the current measurement is to meet the
wide range of cell currents encountered in practice.
Currents as high as a few mA to as low as a few 10s
nA need to be detectable, so the gain range of the
amplifier must be large. An integrated gain control
block consisting of resistors R
1
and R
2
and a PMOS
switch was included. With the switch opens the gain
contribution is just the resistance R
1
but when closed
the contribution is the parallel combination of R
1
and R
2
. This internal gain function was used in
conjunction with an external potentiometer (dotted
interconnect) which was first realised as a multiturn
variable resistor but later as a 256 tap digital
potentiometer for full gain control assuring the
required dynamic range.
Another important challenge for the
transimpedance amplifier design was to provide
uniformity of the frequency response, and to
eliminate possible oscillations in the transient
process, which can occur from a wide capacitance
range of the working electrode connected to the
amplifier input. This is a particular concern where
the device is controlled by a DAC which can only
approximate smooth waveforms with stepped
values. Again a provision was taken to connect a
bandwidth reducing capacitance across the stage
feedback path; that is between the working electrode
and V
out
pin.
DEVELOPMENT AND EVALUATION OF AN ON-CHIP POTENTIOSTAT FOR BIOMEDICAL APPLICATIONS
105