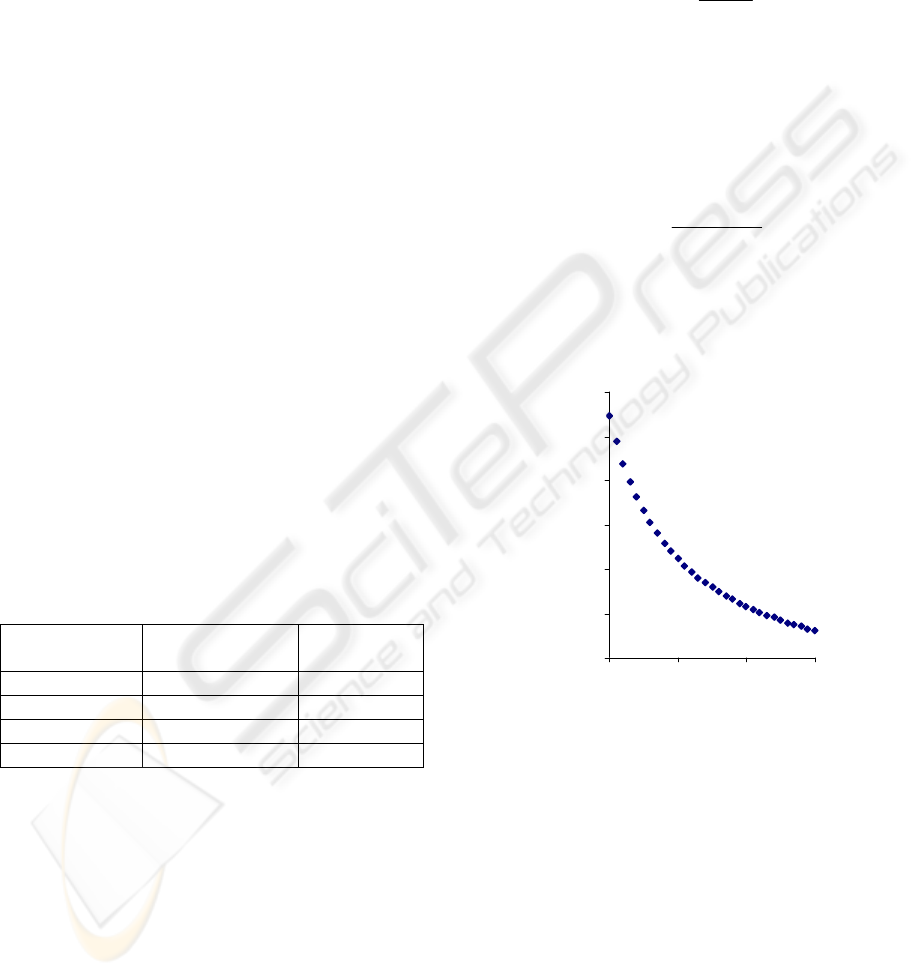
analysis, especially near critical concentration (20%)
which is 25% bacteria concentration. By taking
value of transmission of drain fluid with E.Coli exist
in the drain fluid for 1 day after taken from patient
and path optical length 0.865 cm, the transmission
result is 8.3% then the transmission value is plotted
in Figure 1 to obtain the absorbance value is 1.08.
By using Equation (2) can be calculated the molar
absorption coefficient which is 0.4998. Furthermore,
the optical path length is fixed at 1 mm and using the
Equation (2) the absorbance is 0.125. By plotting the
absorbance result to Figure 1, the transmission value
is found to be 75%.
The important parameters have to be analyzed
to obtain the critical incident angle. It depends on
material properties especially refractive index of the
materials of both core and cladding material. The
incident angle must be more than critical angle to
obtain total reflection. Based on measurement Al
2
O
3
,
deposited by ALD, refractive index ‘n
1
’
is 1.646.
Cladding’s refractive index ‘n
2
’ is 1.33. The angle
can be calculated from Snell’s law modified as
Equation (4) and the result of critical incident angle
is 53.9
o
. In this experiment, the waveguide will be
coupled with source of light with incident angle 90
o
,
λ
i
= 2000 nm and using Equation (6), the penetration
depth of the waveguide sensor can be calculated of
164 nm. Due to the symmetrical waveguide, a
maximum sensitivity S
max
= 2.S (Velduis et al, 200).
Hence, using Equation (9) can be found the
maximum sensitivity of sensor as shown in Table 1.
Table 1: Sensitivity of waveguide of varying waveguide
thickness.
Thickness, nm
(t)
Effective index
(n
e
)
Sensitivity
(S
max
)
50 1.331 0.997
100 1.333 0.989
150 1.338 0.975
200 1.344 0.965
The film has as incompatible elastic mismatch
strain with respect to the substrate; this strain might
be due to thermal expansion effects, epitaxial
mismatch, phase transformation, chemical reaction,
moisture absorption or other physical effects.
Whatever the origin of the strain, the goal here is to
estimate the curvature of the substrate, within the
range of elastic response, induced by the stress
associated with the incompatible strain.
Stoney’s formula is original analysis of the
stress in a thin film deposited on a rectangular
substrate was based on a uniaxial state of the stress.
Consequently, his expression for curvature did not
involve use of the substrate biaxial modulus M
s
.
Consequently, it can be applied in situations in
which mismatch derives from in elastic effect (Freud
and Suresh, 2003). The expression for curvature is
famous Stoney’s formula relating curvature to stress
in the film as:
2
6
mf
s
h
h
κ
=
(10)
Where
κ
represents the curvature, or inverse of the
radius of curvature, of this plane,
σ
f
is mean stress,
h
f
is the thickness of the thin film, M
s
is substrate
biaxial modulus and h
s
is substrate thickness. The
mean mismatch strain of substrate and the
corresponding mismatch stress of thin film
expressed as:
23
23
Si Al O
m
Al O
aa
a
ε
−
=
(11)
mmf
σε
=
(12)
Figure 4 shows the curvature radius of various thin
film thickness. The curvature radii gradually
decrease with increasing thin film thickness.
5
10
15
20
25
30
35
50 100 150 200
Thickness
(nm)
Radius (m)
Figure 4: Curvature radius as function of thin film stress of
Al
2
O
3
in the surface substrate with various thin film
thickness.
By taking the thin film thickness h
f
= 50 nm of Al
2
O
3
is grown on Si-wafer substrate with thickness h
s
=
500 µm, lattice parameter of a
Al
= 0.405nm, a
O
=
0.683 nm and a
Si
= 0.5431nm. The lattice parameter
of Al
2
O
3
at room temperature is a
Al2O3
= 0.53a
Al
+
0.47a
O
= 0.536 nm. The biaxial modulus of Al
2
O
3
(M
f
) and Si (M
s
) are 380 GPa and 180.5 GPa,
respectively. By substitute Equation (11) and
Equation (12) into Equation (10) can be obtained
κ
=
0.031. Then the change of curvature radius is
ρ
=
κ
-1
= 32.34 m. The result of the curvature value is
AL2O3 NANOLAYER AS EVANESCENT WAVEGUIDE FOR BIOMEDICAL SENSOR APPLICATION
47