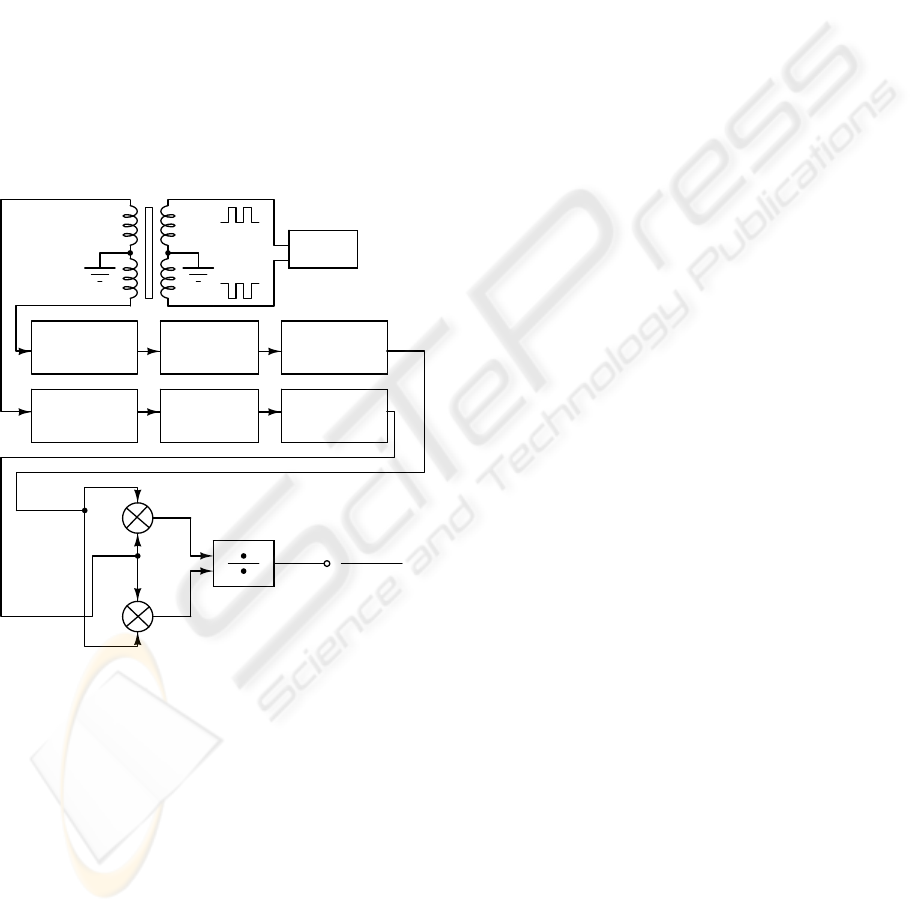
The displacement actuator is then constituted by
four windings: two primary windings with a small
number of turns and two secondary windings with a
larger number of turns. The primary windings are
excited by the power switching circuit in order to
produce the displacement of the core. The secondary
windings use to advantage the switching frequency
of the PWM in order to measure the displacement,
as it will be described in the following paragraphs.
A block diagram of the displacement transducer
and respective signal conditioner is shown in Figure
8. The circuit consists of a PWM wave generator to
drive the primary windings, a conditioner circuit for
each secondary winding, a differential amplifier that
determines the difference between the voltages of
the secondary windings and a summing amplifier,
which determines the sum of the secondary winding
voltages.
Figure 8: block diagram of the displacement transducer
and signal conditioner.
The PWM wave that is applied to the primary
windings, where besides producing the displacement
of the core, it induces in the secondary windings a
voltage whose magnitude difference is proportional
to the core position. These two secondary voltages
are band-pass filtered for the fundamental frequency
of the PWM generator. So, the output from the band-
pass filters consists of a pair of sine waves whose
amplitude difference, (VA–VB), is proportional to
the core position.
In order to operate in a ratiometric principle and
thus eliminating the errors associated to non-
constant amplitude of the PWM signal, the circuit
computes (VA-VB)/(VA+VB).
The signals VA and VB are firstly rectified and
low-pass filtered. A signal with precise frequency is
not necessary because the inputs are rectified and
only the sine wave carrier magnitude is processed.
There is also no sensitivity to phase shifts between
the primary excitation and the secondary outputs
because synchronous detection is not employed.
Then, the signals are applied to the differential
amplifier and to the summing amplifier. The ratio
(VA-VB)/(VA+VB) is performed by the A/D
(analog to digital) converter. The (VA-VB) signal is
applied to its input and the (VA+VB) signal is used
as reference voltage for the A/D conversion. Finally,
The digital signal is read by the microcontroller.
4 CONCLUSIONS
In this article, it is described the design of a
bioreactor to apply controlled mechanical
stimulation to cell cultures. The bioreactor consists
on a mechanical loading actuator, experimental
chamber, and control system. The actuator is based
on an innovative design of a feedback controlled
electromagnetic actuator, which allows the
measurement of its own position. The control system
is based on a master-slave architecture, where the
master (computer) receives the user commands and
sends the actuation parameters to the slave
(microcontroller). This last one reads and feedback
controls the actuator position.
ACKNOWLEDGEMENTS
The authors thank the Portuguese Foundation for
Science and Technology (FCT) Grants
PTDC/CTM/73030/2006, PTDC/CTM/69362/2006
and NANO/NMed-SD/0156/2007. V. Correia thanks
the FCT for the PhD Grant (SFRH/BD/48708/2008).
J. L. G. Ribelles acknowledge the support of the
Spanish Ministry of Education through project No.
MAT2007-66759-C03-01 (including the FEDER
financial support. and founding in the Centro de
Investigación Principe Felipe in the field of
Regenerative Medicine through the collaboration
agreement from the Conselleria de Sanidad
(Generalitat Valenciana), and the Instituto de Salud.
+
+
-
+
VA-VB
VA+VB
VA
-VB
Full wave
Rectifier
Full wave
Rectifier
Low-pass
Filter
Low-pass
Filter
PWM
Band-pass
Filter
Band-pass
Filter
VA-VB
VA+VB
BIODEVICES 2010 - International Conference on Biomedical Electronics and Devices
150