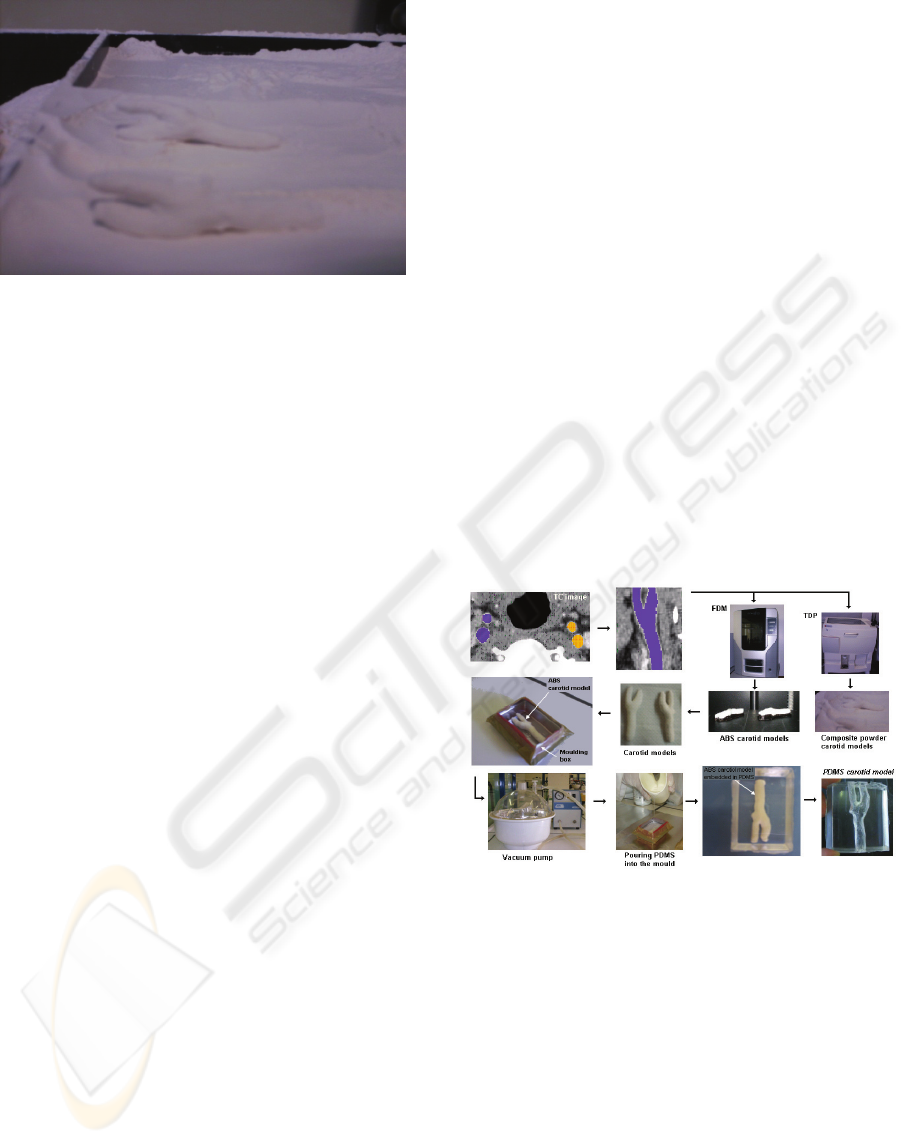
Figure 4: Carotid artery model manufactured by TDP
process.
2.3 Fabrication of PDMS Anatomical
Channels
In vivo animal research is an excellent way of
performing experiments with in environments that
closely mimics the human body. However, in vivo
experiments are laborious, expensive and difficult to
control several parameters and consequently it is
extremely complex to obtain accurate
measurements. On the other hand, by using in vitro
models, besides reducing the number of sacrificed
animals, this kind of models have many other
advantages over in vivo models, such as the ability
to control important parameters, obtain accurate
measurements and reproducible experiments. For
hemodynamic researchers in vitro models have been
extremely attractive as this kind of models allows
systematic flow studies. Hence, many studies on the
blood flow behavior in vitro models have been
performed over the past years. However, most
studies have been done in rigid or simplified models
(Goldsmith et al., 1996)(Lima, 2007). As a result,
there is a need to develop more realistic in vitro
models with geometries and environments that
closely mimics the human body. In this study we
applied two rapid prototyping techniques – Fused
Deposition Modeling (FDM) and Tridimensional
Printing (TDP) combined with a PDMS casting
technique to obtain anatomically realistic models of
a carotid artery.
The PDMS carotid artery was fabricated by
using two kinds of rapid prototyping techniques, i.e.,
Fused Deposition Modeling (FDM) and
Tridimensional Printing (TDP). The main steps for
fabricating the PDMS carotid channel (Figure 5)
were as follows. First, the human carotid geometry
was obtain by computerized tomography (TC) and
then printed by means of FDM and TDP. By
applying the FDM we were able to obtain the carotid
model in a copolymer of acrylonitrile, butadiene,
and styrene (ABS), whereas by using a TDP we
have obtained another kind model in a composite
powder. Next, carotid models with clay supports
where positioned in the bottom of a molding box in
order to pour an elastomeric material into the mould.
Note that, the model obtained by FDM technique
needed to be cut around the branch in order to pull
the model from the casting material without
breaking it. The elastomeric material selected was
the polydimensiloxane (PDMS) due to its
outstanding properties, including good optical
transparency and biocompatibility, easily reversible
sealing to glass, elasticity, replication of fine and
complex geometries, permeable to gases, thermally
stable, and low cost (Lima, 2008). The PDMS
prepolymer was prepared by mixing a commercial
prepolymer and catalyzer (Silpot 184; Dow Corning,
USA) at a weight ratio of 10:1. After removing the
bubbles, created during mixing, by a vacuum pump
the PDMS mixture was poured into the mould
containing the carotid model and then baked into a
oven for about 2 hours at a temperature of about
60°C. Both model and mould with PDMS were then
cooled to room temperature.
Figure 5: Main steps to fabricate PDMS carotid channels.
The embedded carotid model manufactured by
the FDM technique was pulled out of the PDMS and
as result it was possible to obtain an anatomically
transparent model of a human carotid artery (see
Figure 6). From Figure 6 it is possible to observe
that the PDMS carotid model seems to have enough
good transparency able to perform blood flow
visualization studies. However, should be pointed
out that walls of this PDMS carotid model have high
levels of roughness due to the rapid prototyping
technique (FDM) used to manufacture the ABS
carotid model. In a near future, we are planning to
polish the surface of the ABS carotid model to
decrease roughness of the model.
RAPID PROTOTYPING OF 3D ANATOMICAL MODELS TO HEMODYNAMIC STUDIES
249