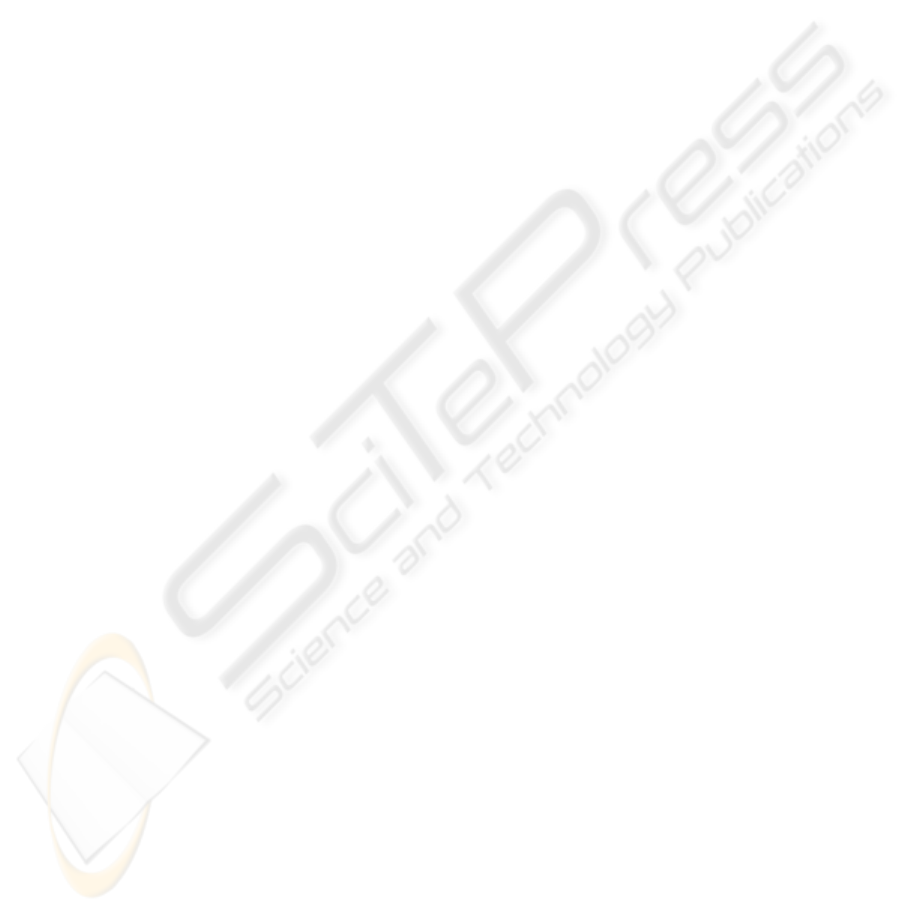
a mesh processing tool. The use of a mesh process-
ing tool has the important advantage that the correct
alignment (which is difficult for 3D measurements ac-
quired by time-of-flight cameras due to the random
and systematic errors in the 3D data) can be super-
vised by a user. Compared to a manual creation of
a 3D model the needed workload is considerably re-
duced. Thus the 3D model can easily be created and
also easily be updated when some parts of the recon-
structed scene change.
The evaluation of our approach shows that the re-
constructed 3D models created with our approach can
successfully be used for model based camera track-
ing. This is even the case for industrial objects with
a metallic surface which are difficult to measure reli-
ably with a time-of-flight camera.
So far the color information is already very useful
for the reconstruction and for the initialisation of the
camera tracking because it is much easier for the user
to supervise a correct alignment of the submeshes if
the texture of the meshes is displayed. In future work
we will extend our approach by using the color infor-
mation of the reconstructed 3D model not only for the
reconstruction step and the camera pose initialization
but also for the frame-to-frame camera tracking.
ACKNOWLEDGEMENTS
This work has been performed within the AvilusPlus
research project granted by the German Ministry of
Education and Research (BMBF). The authors wish
to thank the MeshLab developers and the members of
the Multimedia Information Processing Group of the
University of Kiel for making their MultiCameraCal-
ibration tool and MeshLab publicly available.
REFERENCES
Becker, M., Bleser, G., Pagani, A., Stricker, D., and Wuest,
H. (2007). An architecture for prototyping and ap-
plication development of visual tracking systems. In
Capture, Transmission and Display of 3D Video (Pro-
ceedings of 3DTV-CON 07 [CD-ROM]).
Besl, P. and McKay, N. (1992). A method for registration of
3-d shapes. In IEEE Transactions on Pattern Analysis
and Machine Intelligence, volume 14(2), pages 239–
256.
Bleser, G., Wuest, H., and Stricker, D. (2006). Online cam-
era pose estimation in partially known and dynamic
scenes. In ISMAR 2006: Proceedings of the Fifth
IEEE and ACM International Symposium on Mixed
and Augmented Reality, pages 56–65.
Cignoni, P., Callieri, M., Corsini, M., Dellepiane, M.,
Ganovelli, F., and Ranzuglia, G. (2008). Meshlab:
an open-source mesh processing tool. In Sixth Euro-
graphics Italian Chapter Conference, pages 129–136.
Durand, F. and Dorsey, J. (2002). Fast bilateral filtering for
the display of high-dynamic-range images. In SIG-
GRAPH ’02: Proceedings of the 29th annual con-
ference on Computer graphics and interactive tech-
niques, pages 257–266.
Huhle, B., Jenke, P., and Straßer, W. (2008). On-the-fly
scene acquisition with a handy multi-sensor system.
International Journal of Intelligent Systems Technolo-
gies and Applications (IJISTA), 5(3/4):255–263.
Kolb, A., Barth, E., Koch, R., and Larsen, R. (2009). Time-
of-Flight Sensors in Computer Graphics. In Proc. Eu-
rographics (State-of-the-Art Report).
Lepetit, V. and Fua, P. (2005). Monocular model-based 3d
tracking of rigid objects: A survey. In Foundations
and Trends in Computer Graphics and Vision, vol-
ume 1, pages 1–89.
May, S., Droeschel, D., Holz, D., Wiesen, C., and Fuchs, S.
(2008). 3d pose estimation and mapping with time-of-
flight cameras. In IEEE/RS International Conference
on Intelligent Robots and Systems(IROS), Workshop
on 3D-Mapping.
Oggier, T., Lustenberger, F., and Blanc, N. (2006). Minia-
ture 3d tof camera for real-time imaging. In Percep-
tion and Interactive Technologies, pages 212–216.
Prusak, A., Melnychuk, O., Roth, H., Schiller, I., and Koch,
R. (2008). Pose estimation and map building with a
time-of-flight camera for robot navigation. Interna-
tional Journal of Intelligent Systems Technologies and
Applications, 5(3/4):334–364.
Schiller, I., Bartczak, B., Kellner, F., and Koch, R. (2008a).
Increasing realism and supporting content planning
for dynamic scenes in a mixed reality system incor-
porating a time-of-flight camera. In Proceedings of
the European Conference on Visual Media Produc-
tion, CVMP, volume 5.
Schiller, I., Beder, C., and Koch, R. (2008b). Calibration
of a pmd camera using a planar calibration object to-
gether with a multi-camera setup. In The Interna-
tional Archives of the Photogrammetry, Remote Sens-
ing and Spatial Information Sciences, volume XXI.
ISPRS Congress, pages 297–302.
Shi, J. and Tomasi, C. (1994). Good features to track.
In IEEE Conference on Computer Vision and Pattern
Recognition (CVPR’94), pages 593–600.
TIME-OF-FLIGHT BASED SCENE RECONSTRUCTION WITH A MESH PROCESSING TOOL FOR MODEL BASED
CAMERA TRACKING
309