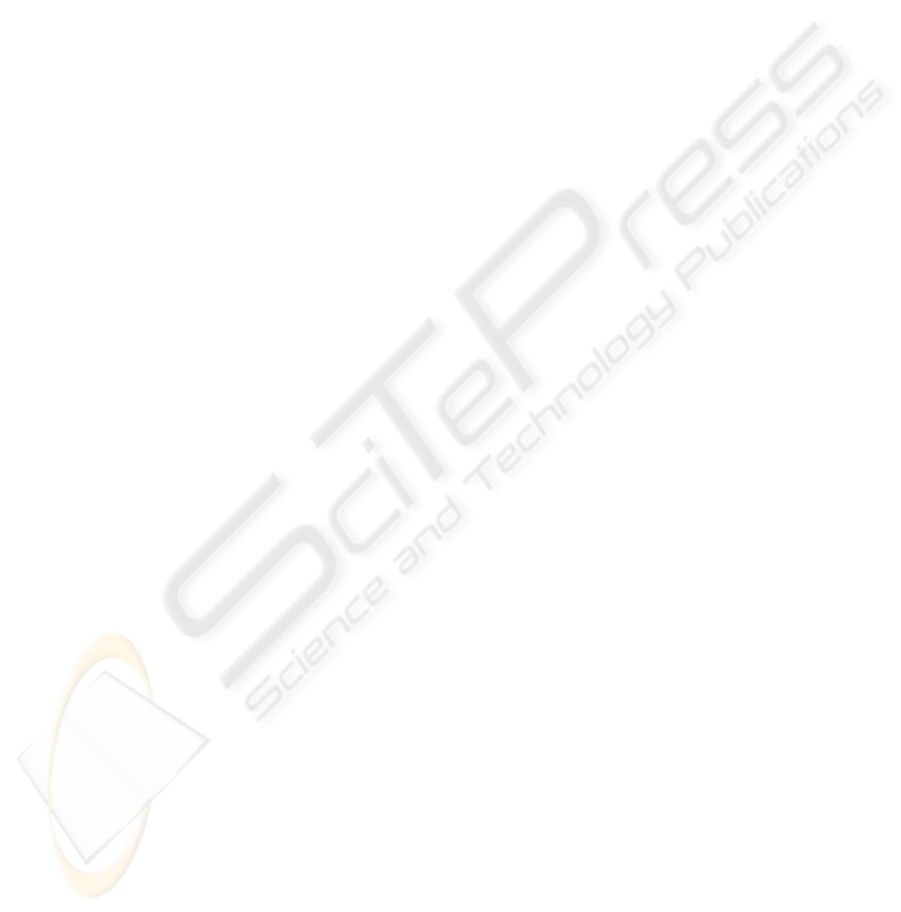
ding problems in our future work.
REFERENCES
Rossignac, J.R., Requicha, A.A.G., 1984. Constant-radius
blending in solid modeling, Computers in Mechanical
Engineering, 65-73.
Lukács, G., 1998. Differential geometry of
1
G variable
radius rolling ball blend surfaces, Computer Aided
Geometric Design 15, 585-613.
Kós, G., Martin, R.R., Várady, T., 2000. Methods to
recover constant radius rolling ball blends in reverse
engineering, Computer Aided Geometric Design 17,
127-160.
Barnhill, R.E., Farin, G.E., Chen, Q., 1993. Constant-
radius blending of parametric surfaces, Computing
Supple 8, 1-20.
Choi, B.K., Ju, S.Y., 1989. Constant-radius blending in
surface modeling, Computer Aided Design 21(4), 213-
220.
Harada, T., Toriya, H., Chiyokura, H., 1990. An enhanced
rounding operation between curved surfaces in solid
modelling, In Proceedings of CG International '90.
Computer Graphics Around the World, Singapore, 25-
29 June, pp. 563-588.
Sanglikar, M.A., Koparkar, P., Joshi, V.N., 1990.
Modelling rolling ball blends for computer aided
geometric design, Computer Aided Geometric Design
7, 399-414.
D.-N. Ying, E.-J. Wang and K. Xue. Blending in solid
modelling. Proceedings of First International
Conference on Computational Graphics and
Visualization Techniques, Sesimbra, Portugal, 16-20
Sept. 1991, Vol. 2, pp. 239-247.
Farouki, R.A.M.T., Sverrisson, R., 1996. Approximation
of rolling-ball blends for free-form parametric
surfaces, Computer Aided Design 28(11), 871-878.
Allen, S., Dutta, D., 1997a. Cyclides in pure blending I,
Computer Aided Geometric Design 14, 51-75.
Allen, S., Dutta, D., 1997b. Supercyclides and blending,
Computer Aided Geometric Design 14, 637-651.
Shene, C.-K., 1998. Blending two cones with Dupin
cyclides, Computer Aided Geometric Design 15, 643-
673.
Bloor, M.I.G., Wilson, M.J., 1989. Generating blend
surfaces using partial differential equations,
Computer-Aided Design 21(3), 165-171.
Bloor, M.I.G., Wilson, M.J., 1990. Representing PDE
surfaces in terms of B-splines, Computer-Aided
Design 22(6), 324-331.
Cheng, S.Y., Bloor, M.I.G., Saia, A., Wilson, M.J., 1990.
Blending between quadric surfaces using partial
differential equations, in Ravani, B. (Ed.), Advances in
Design Automation, vol. 1, Computer and
Computational Design, ASME, 257-263.
Brown, J.M., Bloor, M.I.G., Susan, M., Wilson, M.J.,
1990. Generation and modification of non-uniform B-
spline surface approximations to PDE surfaces using
the finite element method, in Ravani, B. (Ed.),
Advances in Design Automation, Vol. 1, Computer
Aided and Computational Design, ASME, 265-272.
Li, Z.C., 1998. Boundary penalty finite element methods
for blending surfaces, I. Basic theory, Journal of
Computational Mathematics 16, 457-480.
Li, Z.C., 1999. Boundary penalty finite element methods
for blending surfaces, II. Biharmonic equations,
Journal of Computational and Applied Mathematics
110, 155-176.
Li, Z.C., Chang, C.-S., 1999. Boundary penalty finite
element methods for blending surfaces, III,
Superconvergence and stability and examples, Journal
of Computational and Applied Mathematics 110, 241-
270.
Bloor M.I.G., Wilson, M.J., 2000. Generating blend
surfaces using a perturbation method, Mathematical
and Computer Modelling 31(1), 1-13.
You, L.H., Zhang J.J., Comninos, P., 2004a. Blending
surface generation using a fast and accurate analytical
solution of a fourth order PDE with three shape
control parameters, The Visual Computer20, 199-214.
You, L.H., Comninos, P., Zhang, J.J., 2004b. PDE
blending surfaces with
2
C continuity, Computers &
Graphics28(6), 895-906.
You, L.H. Yang, X.S., Pachulski, M. and Zhang, J.J.,
2007. Boundary Constrained Swept Surfaces for
Modelling and Animation, EUROGRAPHICS 2007
and Computer Graphics Forum 26(3), 313-322.
You, L.H., Yang, X.S., Zhang, J.J., 2008. Dynamic skin
deformation with characteristic curves, Computer
Animation and Virtual Worlds 19(3-4), 433-444.
SWEEPING BASED CONTROLLABLE SURFACE BLENDING
83