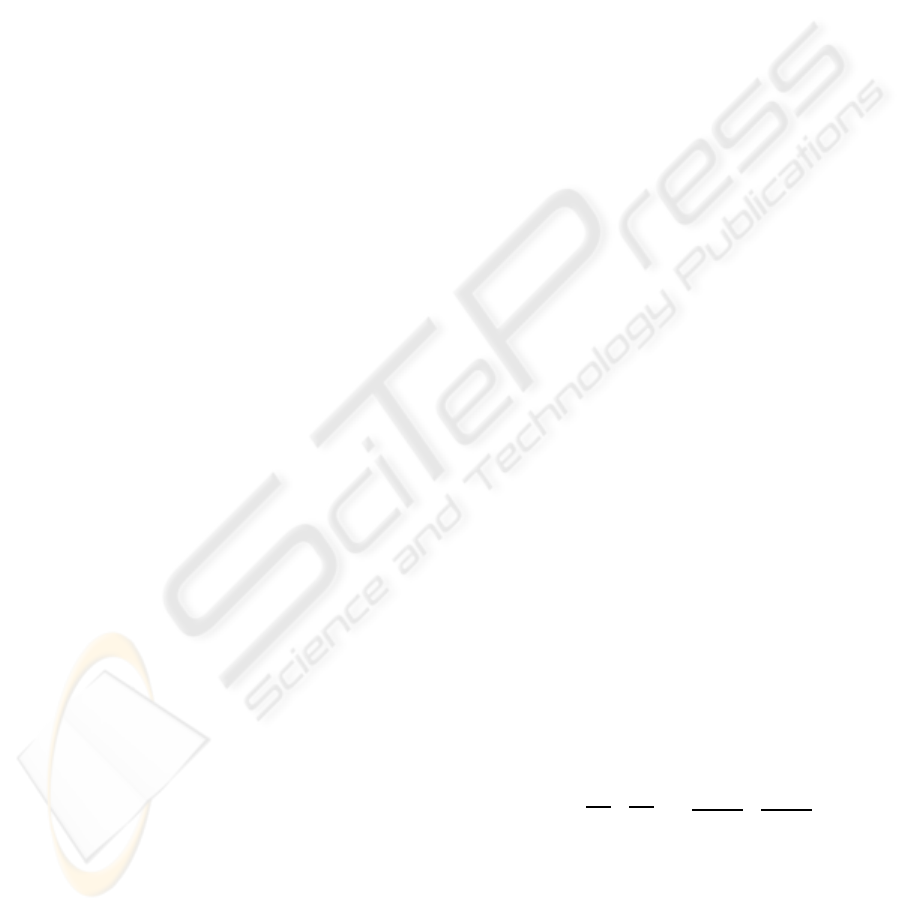
The inclusion of this framework will make the
generation of more complex simulations possible, in
which the interaction of diverse models (organs) that
act together can be possible and, in this manner, de-
sign simulations with major impact in the medical
area, such as the extraction of a tumor or the fully
physical modeling of one part of the body.
ACKNOWLEDGEMENTS
We would like to thank SOFA Team for the help they
bring. We also Graham Maslin for sharing the scalpel
model.
REFERENCES
Allard, J., Cotin, S., Faure, F., Bensoussan, P.-J., Poyer,
F., Duriez, C., Delingette, H., and Grisoni, L. (2007).
Sofa - an open source framework for medical simula-
tion. In Medicine Meets Virtual Reality (MMVR).
Babuska, I. and Melenk, J. M. (1997). The partition of unity
method. International Journal of Numerical Methods
in Engineering, 40:727–758.
Belytschko, T. and Black, T. (1999). Elastic crack growth
in finite elements with minimal remeshing. Interna-
tional Journal of Numerical Methods in Engineering,
45(5):601–620.
Bielser, D., Glardon, P., Teschner, M., and Gross, M.
(2003). A state machine for real-time cutting of tetra-
hedral meshes. In Pacific Graph., pages 377–386.
Forest, C., Delingette, H., and Ayache, N. (2005). Remov-
ing tetrahedra from manifold tetrahedralisation : ap-
plication to real-time surgical simulation. Medical Im-
age Analysis, 9(2):113–122.
Je
ˇ
r
´
abkov
´
a, L. and Kuhlen, T. (2009). Stable cutting of de-
formable objects in virtual environments using xfem.
IEEE Comput. Graph. Appl., 29(2):61–71.
Linblad, A. and Turkiyyah, G. (2007). A physically-based
framework for real-time haptic cutting and interaction
with 3d continuum models. SPM.
Molino, N., Bao, Z., and Fedkiw, R. (2004). A virtual node
algorithm for changing mesh topology during simula-
tion. ACM Trans. Graph. (SIGGRAPH Proc, 23:385–
392.
M
¨
uller, M. and Gross, M. (2004). Interactive virtual materi-
als. In Proceedings of the 2004 conference on Graph-
ics interface, pages 239–246.
Nealen, A., M
¨
uller, M., Keiser, R., Boxerman, E., and Carl-
son, M. (2005). Physically based deformable models
in computer graphics. Eurographics 2005 State of the
Art Report.
Nesme, M., Kry, P. G., Je
ˇ
r
´
abkov
´
a, L., and Faure, F. (2009).
Preserving topology and elasticity for embedded de-
formable models. In ACM Transactions on Graphics
(Proc. of SIGGRAPH). ACM. to appear.
Nesme, M., Payan, Y., and Faure, F. (2005). Efficient, phys-
ically plausible finite elements. In Dingliana, J. and
Ganovelli, F., editors, Eurographics (short papers).
Schmidt, H.-M. (2003). Surgical anatomy of the hand.
Thieme.
Serby, D., Harders, M., and Szkely, G. (2001). A new ap-
proach to cutting into finite element models. In Med-
ical Image Computing and Computer Assisted Inter-
vention (MICCAI), number 2208 in LNCS, pages 425–
433. Springer-Verlag.
Sifakis, E., Der, K. G., and Fedkiw, R. (2007). Arbi-
trary cutting of deformable tetrahedralized objects. In
2007 ACM SIGGRAPH / Eurographics Symposium on
Computer Animation, pages 73–80.
Steinemann, D., Harders, M., Gross, M., and Szekely, G.
(2006). Hybrid cutting of deformable solids. In
Proceedings of the IEEE Virtual Reality Conference,
pages 425–433.
Turkiyyah, G., Karam, W. B., Ajami, Z., and Nasri, A. H.
(2009). Mesh cutting during real-time physical simu-
lation. In Symposium on Solid and Physical Modeling,
pages 159–168.
Vidal, F., Bello, F., Brodlie, K., John, N., D.Gould, Philips,
R., and Avis, N. (2006). Principles and aplications of
computer graphics in medicine. Computer Graphics,
pages 113–137.
Vigneron, L. M., Verly, J. G., and Warfield, S. K. (2004).
Modelling surgical cuts, retractions, and resections
via extended finite element method. In Proceed-
ings of Medical Image Computing & Computer As-
sisted Intervention, volume 7 of LNCS, pages 311–
318. Springer Verlag.
APPENDIX A. EXTENDED FINITE
ELEMENT METHOD (XFEM)
The main idea of exploiting the partition of unity
property is to construct basis functions through prod-
ucts of classical shape functions and a local enriched
basis; allowing to generate discontinuous elements.
Hence, the equation of the displacements can be cal-
culated as
u(x) =
n
∑
i=1
Φ
i
(x)u
i
|
{z }
classical
+
n
∑
j=1
Φ
j
(x)ψ
j
(x)a
j
| {z }
enrichment
(7)
where Φ
i
(x) are the clasical shape functions; the
discontinuous enrichment functions are denoted by
ψ
j
(x), and the new nodal DOFs as a
j
. The enrich-
ment function ψ(x) can be any discontinuous func-
tion; commonly, it is the Heaviside function (Eq. 8),
another option is the shifted function defined in Eq. 9.
GRAPP 2010 - International Conference on Computer Graphics Theory and Applications
282