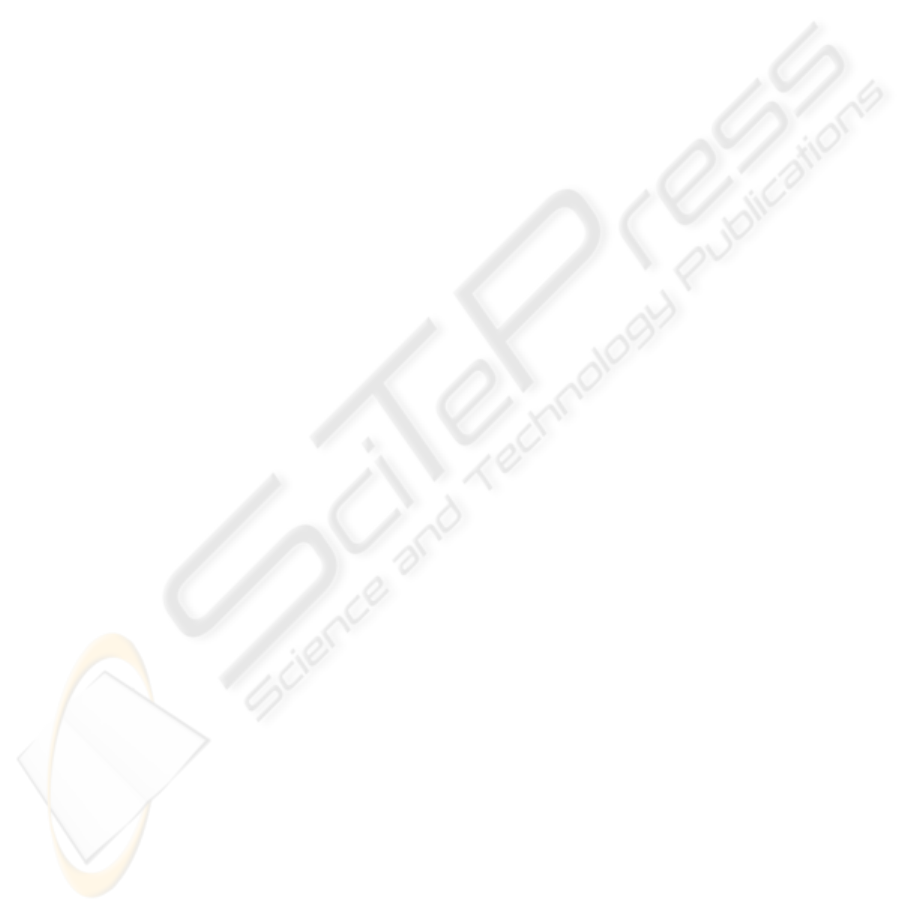
parts of the application. For example, if large val-
ues of K are not desired but the average stretch ratio
should remain at a low level (e.g. solids that practi-
cally keep their volume but have soft surface), then a
lower value for a
1
can achieve the desired result with-
out this increase in stiffness K.
6 CONCLUSIONS
In this paper we presented a particle system that uti-
lizes a full cubic formulation of the inter-particle force
to apply non-linear deformation resistance to simula-
tion conditions of high scale. We also introduced a
constraint based force parameterization for adjusting
the proposed force and described the details regarding
the necessary damping that the presented non-linear
scheme requires in order to ensure numerical stability.
The proposed method is conceptually simple to im-
plement and parameterize according to practical con-
siderations. We showed that the presented method can
robustly handle deformable models that are subject to
environment forces of high scale, both for stretching
and compression. Since the presented force is imple-
mented with particle systems, it has very efficient tim-
ing performance, comparable to simple linear models.
REFERENCES
Baraff, D. and Witkin, A. (1998). Large steps in cloth sim-
ulation. In SIGGRAPH ’98, pages 43–54.
Barbi
ˇ
c, J. and James, D. L. (2005). Real-time subspace inte-
gration for St. Venant-Kirchhoff deformable models.
ACM Transactions on Graphics (SIGGRAPH 2005),
24(3):982–990.
Breen, D. E., House, D. H., and Wozny, M. J. (1994). Pre-
dicting the drape of woven cloth using interacting par-
ticles. In SIGGRAPH ’94, pages 365–372.
Choi, K.-J. and Ko, H.-S. (2002). Stable but responsive
cloth. ACM Trans. Graph., 21(3):604–611.
Choi, K.-J. and Ko, H.-S. (2005). Research problems
in clothing simulation. Computer-Aided Design,
37:585–592.
Delingette, H. (2008). Triangular springs for modeling non-
linear membranes. IEEE Transactions on Visualiza-
tion and Computer Graphics, 14(2):329–341.
Duriez, C., Dubois, F., Kheddar, A., and Andriot, C. (2006).
Realistic haptic rendering of interacting deformable
objects in virtual environments. IEEE Transactions on
Visualization and Computer Graphics, 12(1):36–47.
Etzmuss, O., Gross, J., and Strasser, W. (2003). Deriving
a particle system from continuum mechanics for the
animation of deformable objects. IEEE Transactions
on Visualization and Computer Graphics, 9(4):538–
550.
Goldenthal, R., Harmon, D., Fattal, R., Bercovier, M., and
Grinspun, E. (2007). Efficient simulation of inexten-
sible cloth. ACM Transactions on Graphics (Proceed-
ings of SIGGRAPH 2007), 26(3).
Irving, G., Schroeder, C., and Fedkiw, R. (2007). Volume
conserving finite element simulations of deformable
models. In SIGGRAPH ’07, page 13.
Irving, G., Teran, J., and Fedkiw, R. (2004). Invertible fi-
nite elements for robust simulation of large deforma-
tion. In ACM SIGGRAPH/Eurographics symposium
on Computer animation, pages 131–140.
Kikuuwe, R., Tabuchi, H., and Yamamoto, M. (2009).
An edge-based computationally efficient formulation
of saint venant-kirchhoff tetrahedral finite elements.
ACM Trans. Graph., 28(1):1–13.
Lloyd, B., Szekely, G., and Harders, M. (2007). Identifica-
tion of spring parameters for deformable object simu-
lation. IEEE Transactions on Visualization and Com-
puter Graphics, 13(5):1081–1094.
Moore, P. and Molloy, D. (2007). A survey of computer-
based deformable models. In IMVIP ’07: Proceed-
ings of the International Machine Vision and Image
Processing Conference, pages 55–66.
Nealen, A., Mueller, M., Keiser, R., Boxerman, E., and
Carlson, M. (2006). Physically based deformable
models in computer graphics. Computer Graphics Fo-
rum, 25(4):809–836.
Picinbono, G., Delingette, H., and Ayache, N. (2003). Non-
linear anisotropic elasticity for real-time surgery sim-
ulation. Graph. Models, 65(5):305–321.
Provot, X. (1995). Deformation constraints in a mass-spring
model to describe rigid cloth behavior. In Graphics
Interface ’95, pages 147–154.
Schmedding, R., Gissler, M., and Teschner, M. (2009). Op-
timized damping for dynamic simulations. In Spring
Conference on Computer Graphics, Budmerice, Slo-
vakia, pages 205–212.
Selle, A., Lentine, M., and Fedkiw, R. (2008). A mass
spring model for hair simulation. ACM Trans. Graph.,
27(3):1–11.
Selle, A., Su, J., Irving, G., and Fedkiw, R. (2009). Robust
high-resolution cloth using parallelism, history-based
collisions, and accurate friction. IEEE Transactions
on Visualization and Computer Graphics, 15(2):339–
350.
Terzopoulos, D., Platt, J., Barr, A., and Fleischer, K. (1987).
Elastically deformable models. In SIGGRAPH ’87,
pages 205–214.
Volino, P., Faure, F., and Magnenat-Thalmann, N. (2009).
Simple, yet accurate tensile stiffness. ACM Trans.
Graph., 28(4).
Volino, P. and Thalmann, N. M. (2000). Implementing fast
cloth simulation with collision response. In CGI ’00:
Proceedings of the International Conference on Com-
puter Graphics, page 257.
Wu, Z., Au, C., and Yuen, M. (2003). Mechanical proper-
ties of fabric materials for draping simulation. Inter-
national Journal of Clothing Science and Technology,
15(1):56–68.
A PRACTICAL APPROACH FOR APPLYING NON-LINEAR DYNAMICS TO PARTICLE SYSTEMS
53