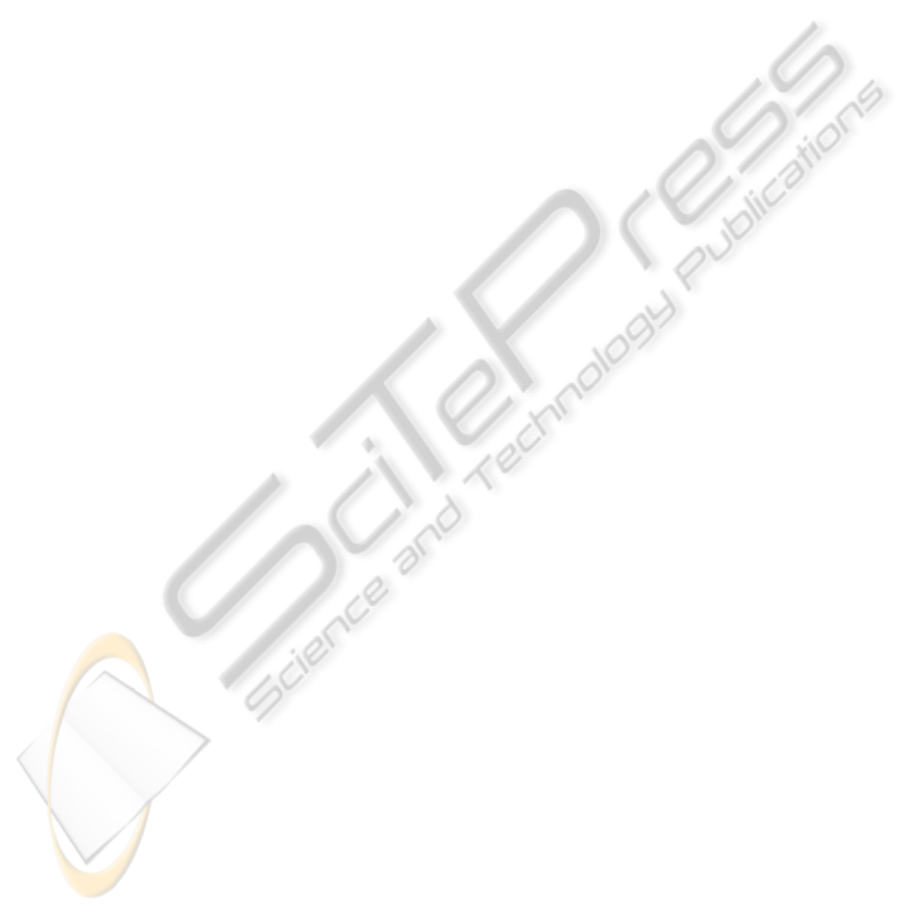
potentiometers mechanical link and to the inertia of
the SMA wires, being smallest than 0.05 mm. The
heating phase is approximately 9 times more rapidly
than the cooling phase; heating time equals 8 s while
the cooling time equals 70 s.
For the final experimental validation test (wind
tunnel test), with real aerodynamic forces load, the
1500 N preloaded forces of the gas springs was
reconsidered. From Fig. 8 (α=2°, Mach=0.225) a
decrease of the SMA wires work temperatures vis-à-
vis of numerically simulated and bench tested cases
is observed. The decrease of these temperatures is a
beneficial one taking into account the negative
impact of a strong thermal field on the other
component of the system, especially on the flexible
skin and on the pressure sensors. Also, a high
frequency noise influencing the LVDT sensors and
the thermocouples instrumentation amplifiers can be
observed. The noise sources are the wind tunnel
vibrations and instrumentation electrical fields. With
this noise, the amplitude of the actuation error
(difference between the realized deflections and
desired deflections) is under 0.07 mm, but this
doesn’t affecting the transition, which is stable on a
sensor with a high RMS spike like in Fig. 9.
So, the results obtained for the actuators control
are very good, the controller fully satisfying the
requirements imposed for the project purpose
achievement.
The designed controller is used for the open loop
development stage of a morphing wing project, but
the closed loop of the morphing wing system, based
on the pressure information received from the
sensors and on the transition point position
estimation, will include, as an internal loop, the
actuation lines here presented controller.
ACKNOWLEDGEMENTS
We would like to thank the Consortium of Research
in the Aerospatial Industry in Quebec (CRIAQ),
Thales Avionics, Bombardier Aerospace, and the
National Sciences and Engineering Research
Council (NSERC) for the support that made this
research possible. We would also like to thank
George Henri Simon for initiating the CRIAQ 7.1
project and Philippe Molaret from Thales Avionics
and Eric Laurendeau from Bombardier Aeronautics
for their collaboration on this work.
REFERENCES
Austerlitz, H., 2003, Data acquisition techniques using
PCs, Elsevier, USA
Chang, P., Shah, A., Singhee, M., 2009, Parameterization
of the Geometry of a Blended Wing Body Morphing
Wing, Project report, Georgia Institute of Technology,
April 2009, Atlanta, Georgia, USA
Gonzalez, L., 2005, Morphing Wing Using Shape Memory
Alloy: a concept proposal, Final research paper, Texas
A&M University, College Station, Texas, USA
Hinshaw, T. L., 2009, Analysis and Design of a Morphing
Wing Tip using Multicellular Flexible Matrix
Composite Adaptive Skins, Master of Science Thesis,
Virginia Polytechnic Institute and State University,
Virginia, USA
Kirianaki, N. V., Yurish, S. Y., Shpak, N. O., Deynega,
V.P., 2002, Data Acquisition and Signal Processing
for Smart Sensors. John Wiley & Sons
Majji, M., Rediniotis, O. K., Junkins, J. L., 2007, Design
of a Morphing Wing: Modeling and Experiments,
AIAA Atmospheric Flight Mechanics Conference and
Exhibit, Hilton Head, South Carolina, USA
Namgoong, H., Crossley, W. A., Lyrintzis, A. S., 2006,
Aerodynamic Optimization of a Morphing Airfoil
Using Energy as an Objective, 44th AIAA Aerospace
Sciences Meeting and Exhibit, Reno, Nevada, USA
Park, J., Mackay, S., 2003, Practical data acquisition for
instrumentation and control systems, Elsevier, UK
Ruotsalainen, P., et. al., 2009, Shape Control of a FRP
Airfoil Structure Using SMA-Actuators and Optical
Fiber Sensors. Journal of Solid State Phenomena,
Volume 144, pp. 196-201
Smith, K., Butt, J., Spakovsky, M. R., Moorhouse, D.,
2007, A Study of the Benefits of Using Morphing Wing
Technology in Fighter Aircraft Systems, 39th AIAA
Thermophysics Conference, Miami, Forida, USA
A MORPHING WING USED SHAPE MEMORY ALLOY ACTUATORS NEW CONTROL TECHNIQUE WITH
BI-POSITIONAL AND PI LAWS OPTIMUM COMBINATION - Part 2: Experimental Validation
19