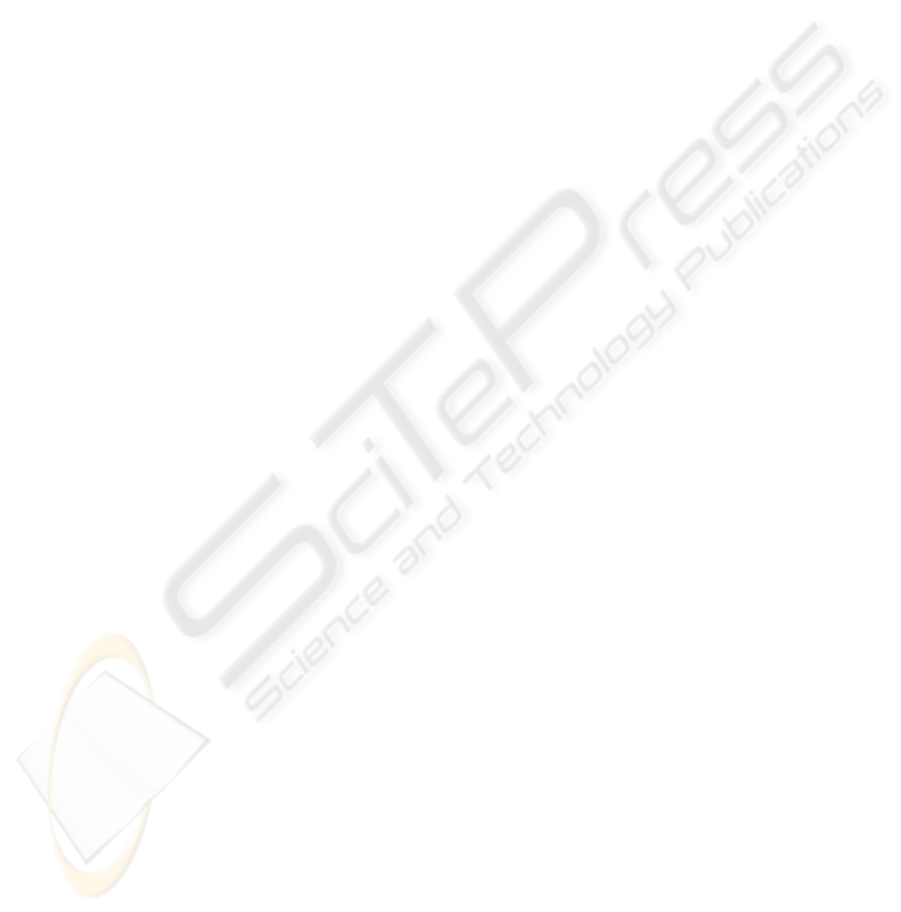
software platform model for forestry contractors.
6 CONCLUSIONS
A unified platform solution for forest industry faces
the ICT challenges that were foreseen in GUN
activities early in years 2002-2003. The UBIWARE
platform being designed to resolve such challenges,
still remains domain independent, and, therefore, has
to be tailored and extended to meet domain-specific
needs. Such platform customization is a first step
towards GERI (Global Enterprise Resource
Integration) – where various industrial domains will
be taken into account. At the moment, UBIWARE-
based industrial applications are naturally needed for
proper platform evolution as a whole. SOFIA
platform will have an extended tool set (RABs and
S-APL models) on top of UBIWARE to solve forest
industry sector tasks. We believe that success of
SOFIA forest industry platform can bring a new
breath both to the forestry and to the ICT worlds.
The results of the research published in
(Lappalainen, 2009), state that utilization of business
models with more than one customer for the
harvesting, transportation and chipping contractors,
can save approximately 50 million euro annually in
the forest biomass supply chain in Finland only. A
simulation study conducted within the same project
has shown that annual cost savings in raw wood
harvesting only would account for 21 million euro at
least if business models and ICT-tools would
support it (Väätäinen et al., 2008).
In addition to the cost savings mentioned above,
SOFIA can be used to provide higher level
harvesting and transportation services for customers
at the same time serving simultaneously many of
them. SOFIA would enable more efficient order
handling and organization of right-time deliveries
while minimizing the risk of human failures.
We have presented the results of the preparatory
project. This work has been inspired by thorough
analysis of business opportunities that led us to look
for technological implementation challenges and
workarounds. At the moment we are considering
both business-oriented as well as science-oriented
directions for further development of SOFIA.
REFERENCES
Bellifemine, F. L., Caire, G., and Greenwood, D. (2007).
Developing Multi-Agent Systems with JADE. Wiley.
Frayret, J.-M., D'Amours, S., Rousseau, A., Harvey, S.,
Gaudreault, J. 2007. Agent-Based Supply Chain
Planning in the Forest Products Industry. International
Journal of Flexible Manufacturing Systems, 19(4), p.
358-391.
Forget, P., D'Amours, S., Frayret, J-M., Multi-behavior
agent model for planning in supply chains: An
application to the lumber industry, Robotics and
Computer-Integrated Manufacturing, Volume 24,
Issue 5, October 2008, Pages 664-679, ISSN 0736-
5845, DOI: 10.1016/j.rcim.2007.09.004.
Hayes, B. 2008. Cloud computing. Commun. ACM 51, 7
(Jul. 2008), 9-11. DOI= http://doi.acm.org/10.1145/
1364782.1364786
Katasonov, A., Kaykova, O., Khriyenko, O., Nikitin, S.,
Terziyan, V., Smart Semantic Middleware for the
Internet of Things. In: Proceedings of the 5-th
International Conference on Informatics in Control,
Automation and Robotics, 11-15 May, 2008, Funchal,
Madeira, Portugal, ISBN: 978-989-8111-30-2,
Volume ICSO, pp. 169-178.
Katasonov, A., and Terziyan, V., 2008. Semantic agent
programming language (S-APL): A middleware
platform for the Semantic web. In Proc. 2nd IEEE
International Conference on Semantic Computing, pp.
504–511, 2008.
Kaykova, O., Khriyenko, O., Kovtun, D., Naumenko, A.,
Terziyan, V., and Zharko, A., 2005. General Adaption
Framework: Enabling Interoperability for Industrial
Web Resources, In: International Journal on Semantic
Web and Information Systems, Idea Group, Vol. 1,
No. 3, pp.31-63.
Lappalainen, M., 2009 Kotimaisen puunhankinnan
tulevaisuuden liiketoimintamallit –tutkimushanke.
Loppuraportti., University of Jyväskylä, School of
Business and Economics. Working paper No
355/2009.
Penttinen, M. & Mikkola, J. & Rummukainen, A., 2009.
Profitability of wood harvesting enterprises. Working
Papers of the Finnish Forest Research Institute, No.
126.
Terziyan, V., 2003. Semantic Web Services for Smart
Devices in a “Global Understanding Environment”, In:
R. Meersman and Z. Tari (eds.), On the Move to
Meaningful Internet Systems 2003: OTM 2003
Workshops, Lecture Notes in Computer Science, Vol.
2889, Springer-Verlag, pp.279-291.
Terziyan, V., 2005. Semantic Web Services for Smart
Devices Based on Mobile Agents, In: International
Journal of Intelligent Information Technologies, Vol.
1, No. 2, Idea Group, pp. 43-55.
Vesterinen, M., 2005. Kotimaisen puunhankinnan
tulevaisuuden liiketoimintamallit. In edition Niemelä,
T. et al. Puheenvuoroja yrittäjyydestä maaseudulla.,
University of Jyväskylä, School of Business and
Economics, Publications No: 152/2005. pp. 84-100.
Väätäinen, K., Lappalainen, M., Asikainen, A. and Anttila,
P. 2008. Kohti kustannustehokkaampaa puunkorjuuta
– puunkorjuuyrittäjän uusien toimintamallien
simulointi., Finnish Forest Research Institute.
Working Papers No 73.
ICEIS 2010 - 12th International Conference on Enterprise Information Systems
22