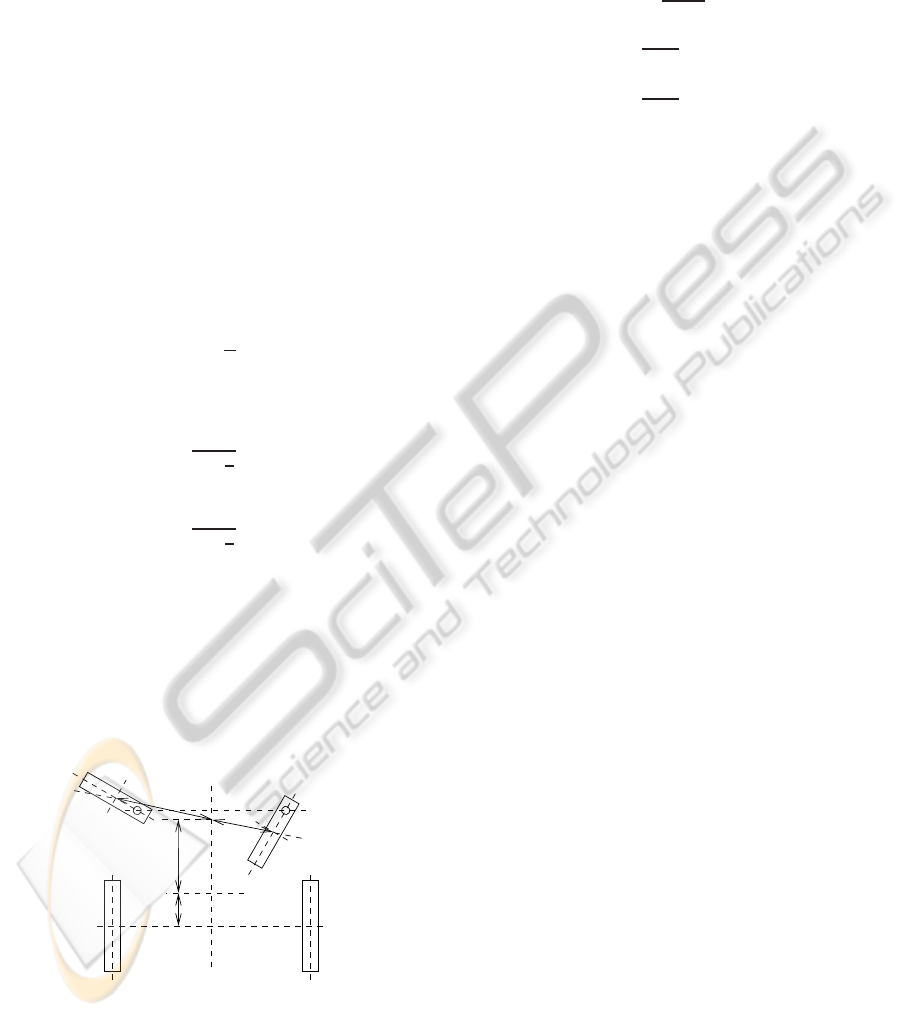
where F
ground
represents the friction between the
ground and the tire at the ground touching point, and
F
joint
the friction inside the turning joint. The joint
is typically so constructed that F
joint
≪ F
ground
. A
difference between sticking and gliding forces could
not be observed, due to the plasticity of the tire. As
frictional forces grow proportionally with the normal
force between the surfaces, the castor turn forces can
be described as
F = c
castor
L (7)
where L is the load of the castor wheel and c
castor
is constant for a given wheelchair and ground mate-
rial. Equation 7 must be understood as an upper limit
of the required castor force. A rolling castor wheel
requires much smaller turn forces, which should be
considered by the castor controller (see Section 3).
The castor turn force can be projected to the forces
of the two differential drive wheels, F
L
and F
R
(see
Figure 3):
θ = α±
π
2
(8)
¯
F =
¯
F
l
+
¯
F
r
(9)
F
L
= F
l
cosτ
l
(10)
tanτ
L
=
a
b−
d
2
(11)
F
R
= F
r
cosτ
r
(12)
tanτ
R
=
a
b+
d
2
(13)
+ or − in Equation 8 is chosen depending on the in-
tended castor steering direction (left or right swivel).
Equation 9 splits the castor correction force
¯
F into
forces of the differential drive wheels. The left en-
gine produces
¯
F
l
as the sum of the motor force
¯
F
L
and
a shearing force
¯
S
L
(see Figure 3). The left engine
force F
L
is computed by Equations 10 and 11, and the
right one by Equations 12 and 13.
M
b
M
M
r
l
r
p
q
M
l
M
f
Figure 4: Mass distribution to castor and differential drive
wheels.
Figure 4 shows the center of mass M of the
wheelchair at the point with a distance of p to the back
axis. The back wheels are connected with springs to
the chassis, such that both wheels can be assumed
to carry the same weight that sums up to M
b
at the
back axis center. The front wheels carry the remain-
ing mass M
f
, giving the following mass distribution:
M
f
= M
p
p+ q
(14)
M
l
=
r
l + r
M
f
(15)
M
r
=
l
l + r
M
f
(16)
The values for p, l, and r can be obtained from the
ground touch points as in Figure 2.
2.3 Maximal Castor Turn Forces
Using the kinematic model of Sections 2.1 and 2.2,
Figure 5 gives an overview of the forces required by
the differential drive vehicle using the geometry of
the Meyra CHAMP wheelchair (in mm: d = 585, p =
160, a = 470, b = 42). For each value of the left cas-
tor angle (x-axis), the diagram shows the angle of
the right castor wheel, which maximises the required
correction force for one of the two differential drive
motors. The force factor (right y-axis in Figure 5)
is the relation between the required motor force and
the standard situation in the left diagram of Figure
6, where castor turn forces and engine forces are all
equal, and the castor wheels are in a blocking state
when drivingforward. The diagram in Figure 5 shows
two symmetric maximal force factors −2.21 (left en-
gine) and 2.21 (right engine). The −2.21 maximum
for the left drive wheel is also shown in the right
diagram of Figure 6 with castor angles L = 46.08
◦
,
R = 8.28
◦
.
3 MOTION CONTROLLER
The kinematic model described in Section 2 has
been implemented and integrated into the wheelchair
ROLLAND in two ways:
• as an add-on for a classical proportional-integral
(PI) controller using odometry information to
control translational and rotational wheelchair
speed (used for autonomous driving).
• as a pure castor force compensation controller to
support joystick driving.
Although the tests reported in Section 4 have been run
with the pure castor controller, both controllers have
been implemented using the following principles:
1. The castor controller applies a slowly growing
correction force. This helps to adapt to different
ICINCO 2010 - 7th International Conference on Informatics in Control, Automation and Robotics
176