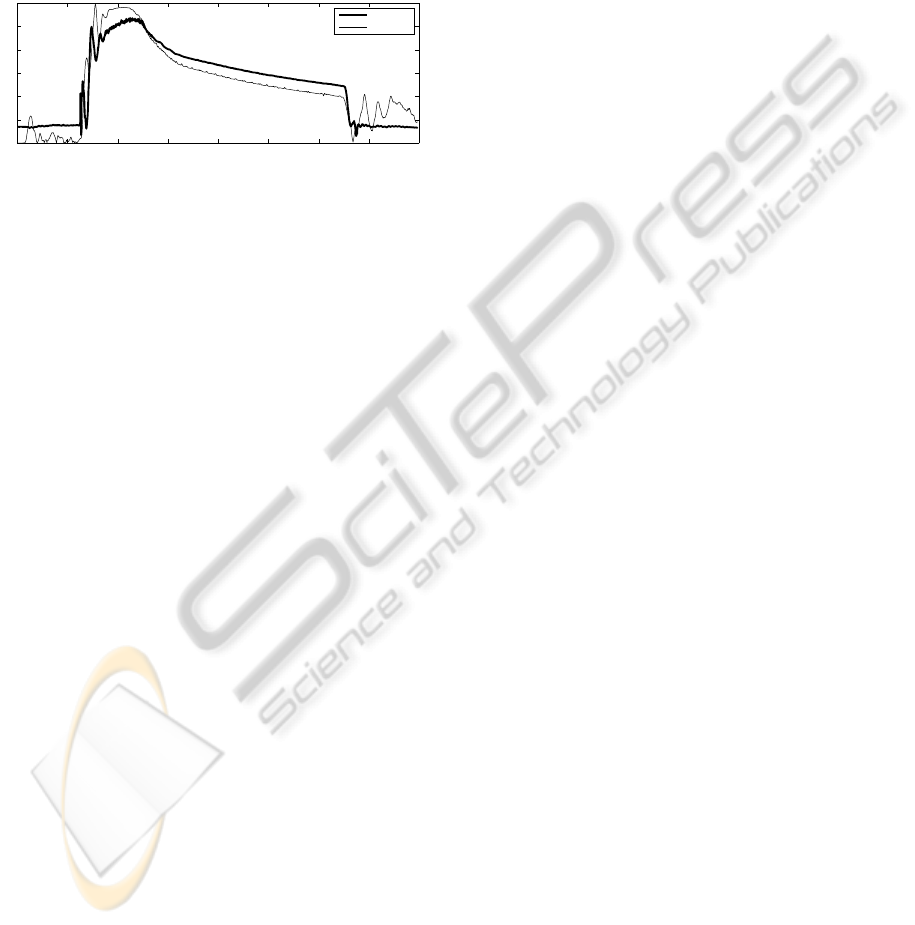
4.3 Measurement Results
We evaluated the detection by driving the manipula-
tor against a workbench at various speeds (50, 100,
150 and 250mm/s), in different directions (X+, Y+,
Z- – see Figure 1a – and mixed diagonal) and with
0.5 or 5 kg of payload mass. Each combination was
measured ten times.
0 2 4 6 8 10 12 14 16
0
10
20
30
40
50
60
measured
estimated
Figure 3: Example of estimated normal contact force in N
over time in s – compared to external sensor measurement.
Although the force characteristic (measured with
a three axis force sensor) varied over the different
scenarios, the detection was successful for nearly all
cases without adapting the threshold. Most problem-
atic was the combination of low speed and small pay-
load. Here we found at the same time false negatives
(5 for X+) and positives (3 for Y+). Other than that,
only one detection of over 300 failed.
The contact force – excluding impact peaks – al-
ways stayed below 20 N (and mostly below 10 N for
speeds below 150mm/s).
5 SHOW-DO PROGRAMMING
In guidance mode, a human can grasp the robot and
move it freely through the workspace. The robot is
still supported by the torques resulting from the model
in Equation 3 but any additional effort from the con-
troller is limited to very low values. Due to the soft
joints, one can interact with the robot along the com-
plete structure.
The guidance mode can be used to quickly move
the robot out of the way, to interactively teach posi-
tions or to record complete continuous path segments.
In our showcase we used a handle with two buttons,
mounted on the lower arm of the robot, to let the user
teach complete pick and place applications – similar
to a macro recorder known from personal computer
software. Tool actions trigger special behaviour – for
example the ”pick” macro at execution time moves
the manipulator in tool direction until it touches the
workpiece and does not solely rely on the recorded
position information.
The interaction with the robot proved to be intu-
itive and all kinds of people were quickly able to per-
form programming tasks.
6 CONCLUSIONS
In this paper we show how to use models of the me-
chanical system and the actuators of a pneumatically
drivenrobot for interaction with the environment. The
illustrated approach worked well when the human op-
erator compensated the remaining model uncertain-
ties. The completely autonomous interaction also
showed good results for the simple case of contact de-
tection.
A first effort to employ the presented interaction
possibilities for more intuitive programming led to
promising feedback from users.
ACKNOWLEDGEMENTS
The authors gratefully acknowledge the Austrian
Center for Competence in Mechatronics (ACCM) for
their support.
REFERENCES
Bicchi, A. and Tonietti, G. (2004). Fast and ”soft-arm” tac-
tics [robot arm design]. Robotics & Automation Mag-
azine, IEEE, 11(2):22–33.
Bremer, H. (2008). Elastic Multibody Dynamics: A Direct
Ritz Approach, chapter 4: Rigid Multibody Systems,
pages 59–113. Springer-Verlag GmbH.
Clark, D. R. and Lehto, M. R. (1999). Handbook of Indus-
trial Robotics, chapter 36: Reliability, Maintenance
and Safety of Robots, pages 717–754. John Wiley &
Sons, 2 edition.
Daerden, F. and Lefeber, D. (2002). Pneumatic artificial
muscles: Actuators for robotics and automation. Eu-
ropean journal of mechanical and environmental en-
gineering, 47:11–21.
Haddadin, S., Albu-Sch¨affer, A., De Luca, A., and
Hirzinger, G. (2008). Collision detection and reaction:
A contribution to safe physical human-robot interac-
tion. In Intelligent Robots and Systems, 2008. IROS
2008. IEEE/RSJ International Conference on, pages
3356–3363.
Hesse, S. (2003). The Fluidic Muscle in Application. Festo
AG & Co.KG.
Van Damme, M., Daerden, F., and Lefeber, D. (2005). A
pneumatic manipulator used in direct contact with an
operator. In Proceedings of the 2005 IEEE Interna-
tional Conference on Robotics and Automation.
INTERACTION OF A FLEXIBLE ROBOT WITH ITS ENVIRONMENT
233