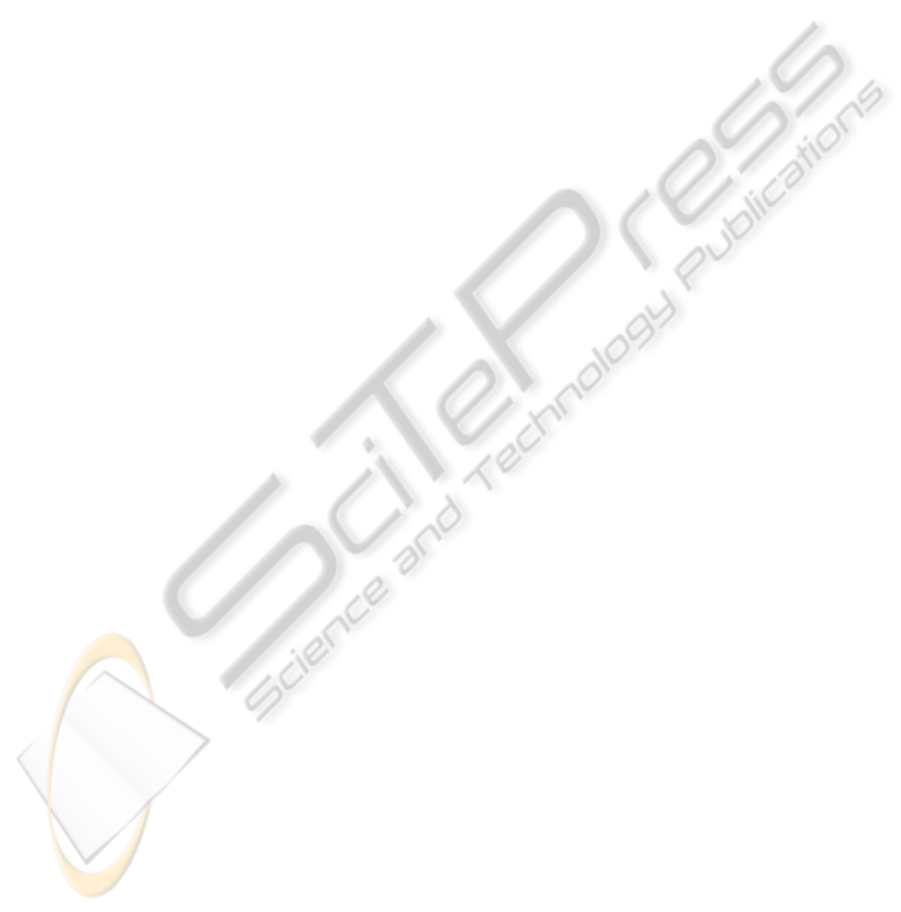
amplitude natural frequency resonance, so the robot
arm doesn’t resonate with actuation system. Also,
considering the displacement (marked with blue in
the figure), it can be observed that the position error
is zero. The overall behavior of the structure is a
very good one.
For the medium speed moves, the stepper motors
may lose steps, but this phenomenon occurs
occasionally and can be considered insignificant if is
evaluated as a ratio lost steps / total number of steps,
meaning that an open loop control can still be
successfully applied to the system. There is a low
amplitude oscillation of the robot’s arm, mainly at
24.6 Hz, induced by the actuation system, but it
induces only a small amplitude natural frequency
resonance, so the robot arm doesn’t resonate with
actuation system. The displacement record reveals a
transient evolution around the final position,
introducing a transient position error, having 2 mm
maximum amplitude and with a short duration, 0.2
seconds. At the end of the transient evolution, the
robot stops on the desired position and the position
error is zero. The overall behavior of the structure is
a good one.
ACKNOWLEDGEMENTS
The research presented in this paper was supported
by the Romanian National University Research
Council CNCSIS through the IDEI Research Grant
ID93 and by FP6 MARTN through FREESUBNET
Project no. 36186.
REFERENCES
Blessing, M., Walker, I. D., 2004. Novel Continuum
Robots with Variable- Length Sections, Proceedings
3rd IFAC Symposium on Mechatronic Systems,
Sydney, Australia, September 2004, pp. 55-60.
Boccolato, G., Manta, F., Dumitru, S., Cojocaru, D., 2009.
3D Control for a Tentacle Robot, 3rd International
Conference on Applied Mathematics, Simulation,
Modelling (ASM'09), Vouliagmeni Beach, Athens,
Greece.
Cojocaru, D., Tanasie, R. T., Marghitu, D. B., 2008. A
Complex Mathematical Expression Operations Tool,
Annals of The Univ. of Craiova, Series: Automation,
Computers, Electronics And Mechatronics, ISSN:
1841-0626, Volume 5(32), no. 1, pp. 7-12.
Cowan, L. S. and Walker, I. D., 2008. “Soft” Continuum
Robots: the Interaction of Continuous and Discrete
Elements, Artificial Life XI.
Crespi, A. and Ijspeert, A. J., 2006. An amphibious snake
robot that crawls and swims using a central pattern
generator. 9th International Conference on Climbing
and Walking Robots (CLAWAR 2006), pp19-27.
Dumitru, S., Cojocaru, D., Dumitru, N., Ciupitu, I.,
Geonea, I., Dumitru, V., 2009. Finite Element
Modeling of a Polyarticulated Robotic System, Annals
of DAAAM, ISSN 1726-9679, pp 969.
Ivanescu, M., Cojocaru, D., Popescu, N., Popescu, D.,
Tănasie, R.T., 2006. Hyperredundant Robot Control
by Visual Servoing, Studies in Informatics and
Control Journal, Volume 15, Number 1, pp93-102,
ISSN 1220-1766.
Robinson, G., Davies, J. B. C., 1999. Continuum robots—
A state of the art. IEEE International Conference on
Robotics and Automation, pp2849–2854. Detroit, MI.
Suzumori, K., Iikura, S., Tanaka, H., 1991. Development
of Flexible Microactuator and its application to
Robotic Mechanisms, Proceedings of the IEEE
International Conference on Robotics and Automation,
pp. 1622-1627.
Tanasie, R. T., Ivanescu, M., Cojocaru, D., 2009. Camera
Positioning and Orienting for Hyperredundant Robots
Visual Servoing Applications, Journal of Control
Engineering and Applied Informatics, Vol 11, No 1,
p19-26, ISSN 1454-8658.
EXPERIMENTS WITH A CONTINUUM ROBOT STRUCTURE
205