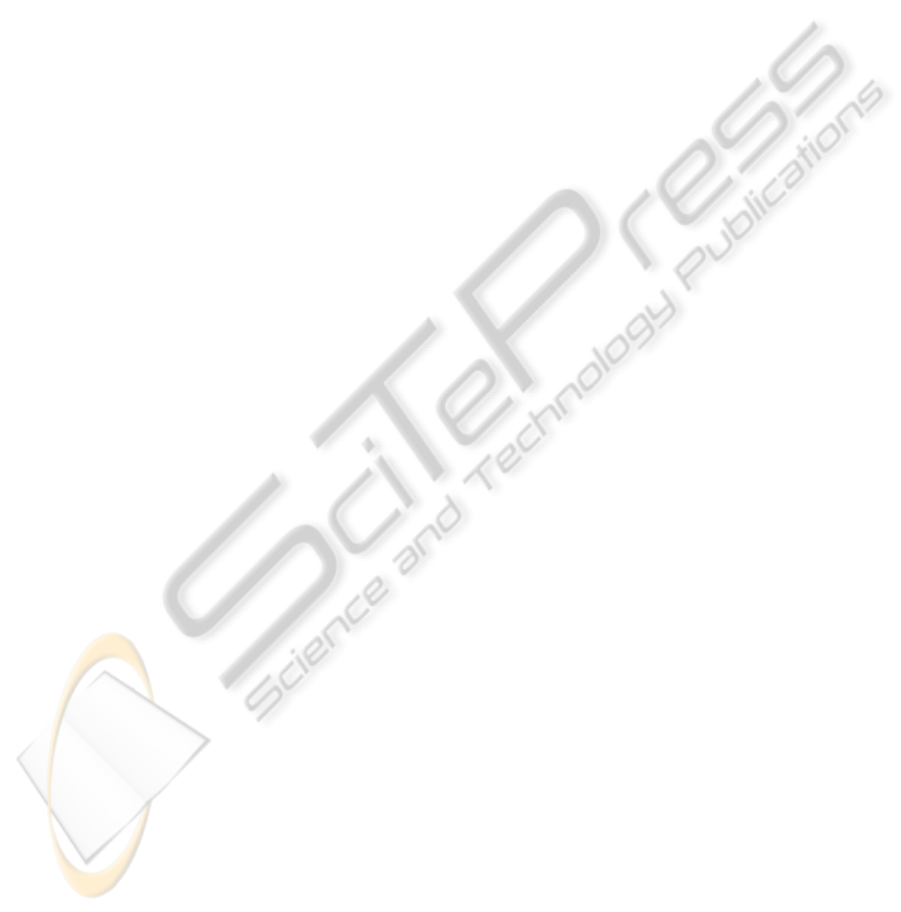
charging and watch on discharging to not outrun a
minimum voltage limits. Due to this we need to
precise charging with balancing/limiting system and
when used (discharged) a system to count energy
and estimate remaining capacity (to stop discharging
in right time) and also watch limits especially
minimum voltage per cell.
Power supply unit then contains a basics
subsystems like: battery cells, protective circuits and
fuel gauge. The protective systems are used in
charging of series of cells and balance variance of
each cell (capacity is not ideally similar, one cell is
fully charged faster than another). Fuel gauge
system based on MCU counts energy stored in cells
and estimate remaining energy which can be
provided. Method is based on simple current and
time measurement and it can be determined a
quantum of current which flows from battery to load
(motor). Also current when charging can be
measured (will be negative, current flows back) but
there is a problem with protective systems because
basic protective system change redundant charging
energy into heat.
In mobile robots for outdoor application we can
estimate a 7 to 10 cell needed to provide power
supply up to 30-42V with continuous discharge
current of 10 to 15A. This make an output power in
range 300 to 600W which is ideal for mobile wheel
based robot with traction based on system from
Figure 7. For the indoor robot same cell can be used
but only two or three will be needed.
Power supply unit is slave to the control unit
(master on the bus) and contain separate control to
measure capacity of power cell(s) and can estimate
and report it to control unit.
3.3 Control Unit
Main unit in robotic carrier is the control unit. This
unit have to decide how to ensure data connection,
how to get to position, to drive traction unit and to
communicate with others carriers and to establish
connection from control centre to deployed robot.
Entire control of robotic carrier is distributed
because all of units have their own control by MCU.
The control unit act like a master on bus via which
all MCUs are connected together. Preferred bus on
such mobile robot is LIN, RS485 or even CAN
based on required speed and data security.
The control unit depends on complexity of
needed solution from algorithms. Based data are
gained from sensor unit and from communication.
The control unit calculates a position to move and
control movement by sending required speed to
closed loop control of motor in traction unit.
Basically this can be covered by some newer MCU
with 32 bit core to obtain a real time solved
problems and results.
Power supply to control unit is from power unit,
so there is a power supply shared with motor on the
other hand a wireless unit have its own because
primary function is to provide data connection.
3.4 Sensor Unit
In mobile robotics we can split sensors into two
groups. Internal sensors are used to ensure a basic
function of the robot. Typically internal sensors are
incremental rotary sensors in motor (traction unit) or
sense resistors in battery (power unit). These sensors
are used to operate a basic system of robot. In the
other hand external sensors are used to contact robot
with his exterior, robot can operate self without it
and this external sensors determine the basic type
and purpose of the robot.
Internal sensors are then on unit which control
basic function of the robot. Sensor unit contains
external sensors to gather data from surrounded area
of robot. Because a primary function of robot is to
carry a wireless system and establish connection to
deployed robot a sensor unit is basically equipped
with sensors to obtain a global position of robot and
to provide them to control unit to establish right
network topology. Also safety ability has to be
implemented to avoid contact robot with obstacle or
to do not injure humans. Basically, the robot needs a
set of tactile sensors to avoid obstacles. Tactile
sensor is contact or contactless, where the simplest
contact tactile sensor is a switch, but this is not very
useful because a short range of operation. More
useful sensors are contactless based on ultrasonic
sensors or infrared optical sensor, both work like
range finder so we can find an obstacle and also we
can estimate range of it.
In indoor application of carrier a network
topology can be determined basically on odometer
(data from traction unit). Indoor due to short ranges
and covering sky a global data cannot be provided
and precise admeasurements have to be used. So
there we need to know a start position of each carrier
to work with this offset of position.
Additional sensors can be used to gather more
data from area where carrier robot is used. This will
work as additional function and area where are
robotics carriers deployed can be better monitored
than only with deployed robot. There can be used
simplest sensors to measure temperature, pressure
sound waves, chemical materials in air etc.
SELF DEPLOYED ROBOTIC NETWORK FOR LONG RANGE SEMIAUTOMATIC OPERATION - Robotics Network
for Distance Data Connection, Areal Signal Connection Coverage or Areal Data Acquisition
431