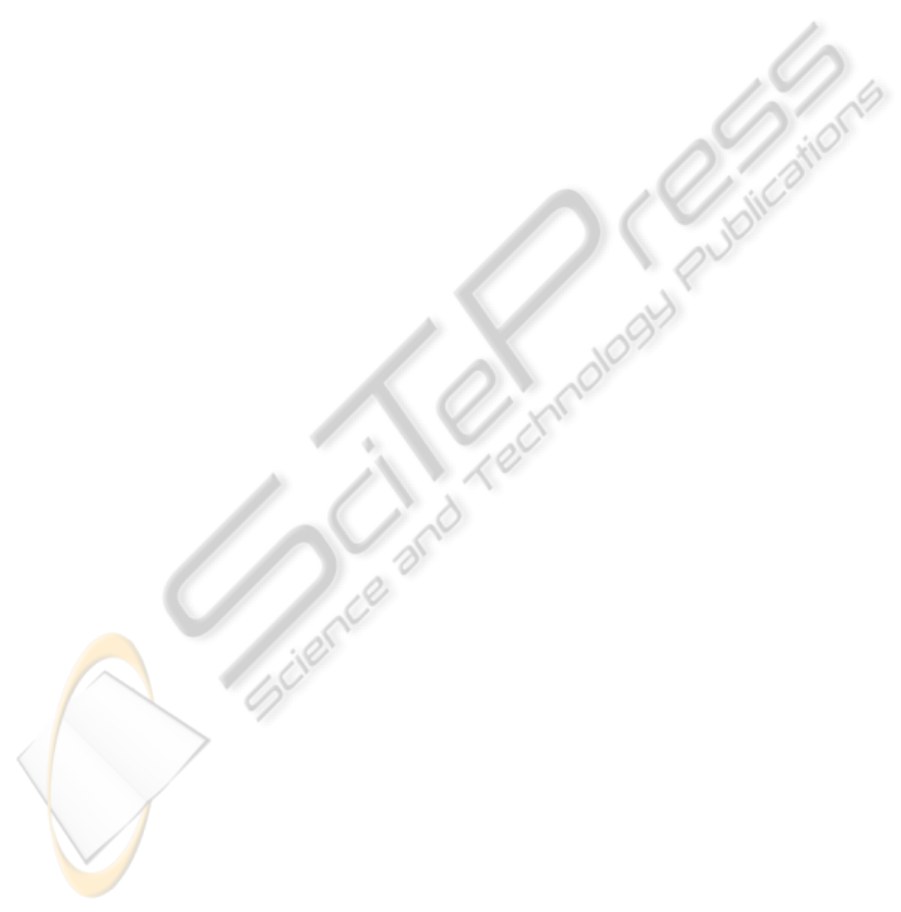
detection rate of 86 per cent for close and fully visi-
ble objects. The random object alignments with un-
favorable object poses, lighting influences and object
occlusions are reasons for recognition failures. How-
ever, considering the large database and the complex-
ity of the scenes the one shot recognition results are
promising.
6 CONCLUSIONS
We presented a system that is able to detect and lo-
calize objects from up to 100 different classes. The
6d detection accuracy of the object pose and the de-
tection rate are evaluated in extensive experiments,
which demonstrated a true positive detection rate of
72% in highly complex cluttered multi object scenes
with partly occlusions. The resulting pose errors had
a standard deviation of 3.4mm in the direction of the
camera (z
c
) and 1.4mm in x
c
and y
c
.
A satisfactory trade-off is found between fast pro-
cessing and good recognition rates and detection er-
rors and failure recognitions. The system is suitable
to applications in cluttered environments with random
object alignments and unknown objects.
In future works, we plan to include sparse bun-
dle adjustment into the model generation process to
increase the precision in the 3d models which is ex-
pected to increase the pose precision on the one hand,
but also to loosen the precision requirements on the
camera pose.
ACKNOWLEDGEMENTS
This work has partly been supported by the German
Federal Ministry of Education and Research (BMBF)
under grant no. 01IME01D, DESIRE.
REFERENCES
Azad, P., Asfour, T., and Dillmann, R. (2007). Stereo-
based 6d object localization for grasping with hu-
manoid robot systems. In IEEE IROS 2007.
Azad, P., Asfour, T., and Dillmann, R. (2009). Stereo-based
vs. monocular 6-dof pose estimation using point fea-
tures: A quantitative comparison. In Autonome Mo-
bile Systeme 2009, Informatik aktuell. Springer.
Collet, A., Berenson, D., Srinivasa, S., and Ferguson, D.
(2009). Object recognition and full pose registration
from a single image for robotic manipulation. In IEEE
ICRA 09.
Dementhon, D. F. and Davis, L. S. (1995). Model-based ob-
ject pose in 25 lines of code. International Journal of
Computer Vision, Springer Netherlands, Volume 15.
Eidenberger, R., Grundmann, T., and Zoellner, R. (2009).
Probabilistic action planning for active scene model-
ing in continuous high-dimensional domains. IEEE
ICRA 2009.
Grundmann, T., Eidenberger, R., and Zoellner, R. (2008).
Local dependency analysis in probabilistic scene esti-
mation. In ISMA 2008. 5th International Symposium
on Mechatronics and Its Applications.
Hartley, R. and Zisserman, A. (2004). Multiple View Geom-
etry in Computer Vision. Cambridge University Press.
Heyer, L. J., Kruglyak, S., and Yooseph, S. (1999). Ex-
ploring expression data: Identification and analysis of
coexpressed genes. Genome Res., 9.
Kragic, D., Miller, A. T., and Allen, P. K. (2001). Real-time
tracking meets online grasp planning. In IEEE ICRA
2001, Seoul, Republic of Korea.
Lowe, D. G. (1999). Object recognition from local scale-
invariant features. In International Conference on
Computer Vision, pages 1150–1157, Corfu, Greece.
Nayar, S., Nene, S., and Murase, H. (1996). Real-time 100
object recognition system. In IEEE ICRA 1996.
Pan, Q., Reitmayr, G., and Drummond, T. (2009). Pro-
FORMA: Probabilistic Feature-based On-line Rapid
Model Acquisition. In Proc. 20th British Machine Vi-
sion Conference (BMVC), London.
Seitz, S. M., Curless, B., Diebel, J., Scharstein, D., and
Szeliski, R. (2006). A comparison and evaluation of
multi-view stereo reconstruction algorithms. In IEEE
CVPR 2006.
Walter, J. A. and Arnrich, B. (2000). Gabor filters for object
localization and robot grasping. In ICPR 2000.
Xue, Z., Kasper, A., Zoellner, J., and Dillmann, R.
(2009). An automatic grasp planning system for ser-
vice robots. In 14th International Conference on Ad-
vanced Robotics (ICAR).
Xue, Z., Marius Zoellner, J., and Dillmann, R. (2007).
Grasp planning: Find the contact points. In IEEE Ro-
bio 2007.
Zhang, J., Schmidt, R., and Knoll, A. (1999). Appearance-
based visual learning in a neuro-fuzzy model for fine-
positioning of manipulators. In IEEE ICRA 1999.
ICINCO 2010 - 7th International Conference on Informatics in Control, Automation and Robotics
308