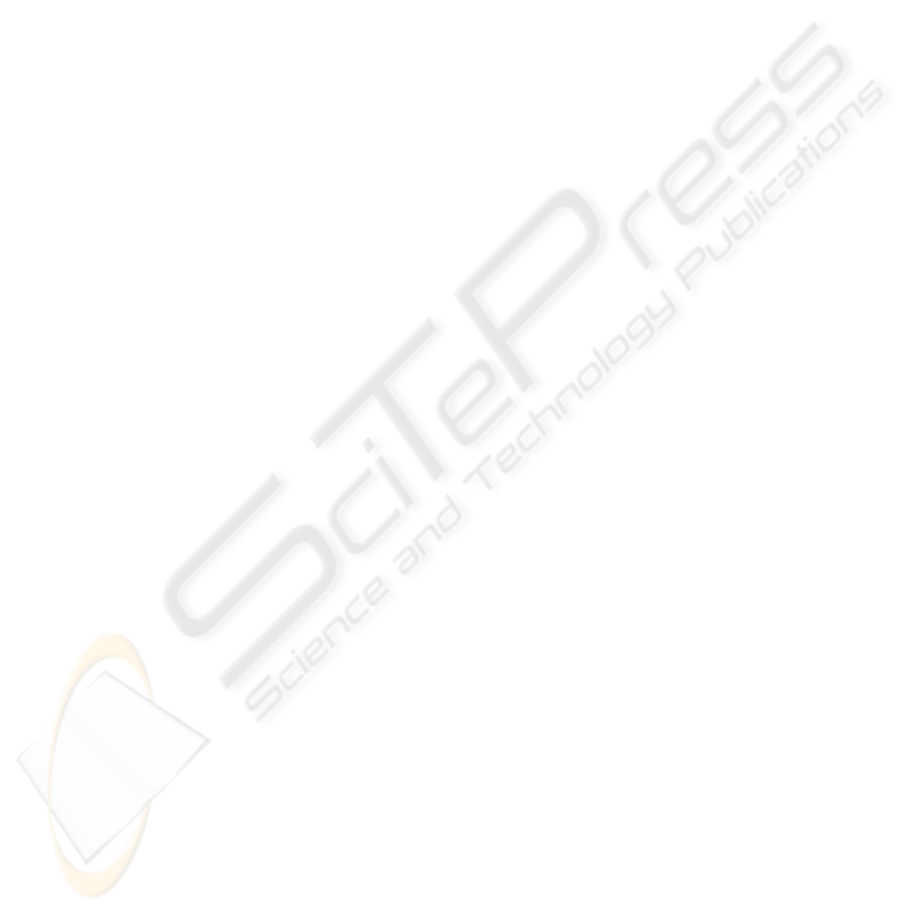
4 CONCLUSIONS
We have presented a research vision for the
development of methods and software tools to
support the design and operation of machine tools
while reducing their energy consumption and
environmental impacts. We presented this vision as
a hierarchy of modeling problems to be resolved
starting from the process level, to the process
planning level, to the machine tool life cycle, to the
sustainable factory and finally to the machining
network management. Besides this vision we briefly
presented support the design and operation of
machine tools while reducing their energy
consumption and environmental impacts. We
presented this vision as a hierarchy of modeling
problems to be resolved starting from the process
level, to the process planning level, to the machine
tool life cycle, to the sustainable factory and finally
to the machining network management. Besides this
vision we briefly presented some of our recent work
on energy consumption modeling in milling of
prismatic parts. This modeling allows comparing
process plans with regard to their cutting parameters
and the selected machine tools. Furthermore, it
allows identifying the most important components of
energy consumption in the machine tool so that we
can focus in their optimal design and use.
In this paper we discussed some of our recent
research relative to the first two levels in the
hierarchy of the machine tool system presented in
Figure 4 and a part of the third level. The complete
coverage of all the life cycles of a machine tool
(third level) is a goal for the future as is the research
on the remaining two levels (fourth and fifth).
REFERENCES
Akbari, J., Oyamada, K., Saito, Y., 2001. LCA of Machine
Tools with regards to their secondary effects on
quality of machined parts. In Proceedings EcoDesign
2001: Second International Symposium on
Environmentally Conscious Design and Inverse
Manufacturing, Tokyo, 347-352.
Dahmus, J., Gutowski, T., 2004. An Environmental
Analysis of Machining. In Proceedings of the 2004
ASME International Mechanical Engineering
Congress, Anaheim, California, USA, November
13-19.
Denkena, B., Reichstein, M., Kramer, N., Jacobsen, J.,
Jung, M., 2005. Eco- and Energy-Efficient Grinding
Processes. In Key Engineering Materials, Vol. 291-
292, 39-44.
Dornkundwar, V., Krishnan, N., Bauer, D. Sheng, P.,
1998. A Distributed Environmental Planning Model
for Machined Components. In Proceedings 5th
International Seminar on Life Cycle Engineering,
KTH Stockolm 227-239.
Jayal, A. D., Balaji, A.K., 2007. On a process modeling
framework for sustainable manufacturing: A
machining perspective. In IMECE 2007, Proceedings
of the ASME International Mechanical Engineering
Congress and Exposition, 301-307.
Munoz, A.A., Sheng, P., 1995. An analytical approach for
determining the environmental impact of machining
processes. In Journal of Materials Processing
Technology 53 , 736-758.
Narita, H., Kawamura, H., Norms, T., Lian-Yi C.,
Fujimoto, H., Hasebe, T., 2006. Development of
prediction system for environmental burden for
machine tool operation. In JSME International
Journal, Series C, v 49, n 4, 1188-95.
Srinivasan, M., Sheng, P., 1999a. Feature-based process
planning for environmentally conscious Machining -
Part 1: microplanning. In Robotics and Computer
Integrated Manufacturing 15, 257-270.
Srinivasan, M., Sheng, P., 1999b. Feature based process
planning in environmentally conscious machining-
Part 2: macroplanning. In Robotics and Computer
Integrated Manufacturing 15 (1999) 271-281.
Young, P., Byrne, G., Cotterell, M., 1997. Manufacturing
and the Environment. In Journal of Advanced
Manufacturing Technology 13:448-493.
Zhigang, J., Hua, Z., Xiao, L., 2008. Study on the cutting
technology based on green manufacturing. In Key
Engineering Materials, v 375-376, 2008, 158-62.
COMPUTING FOR GREEN MACHINING - Recent Results and Research Perspectives
31