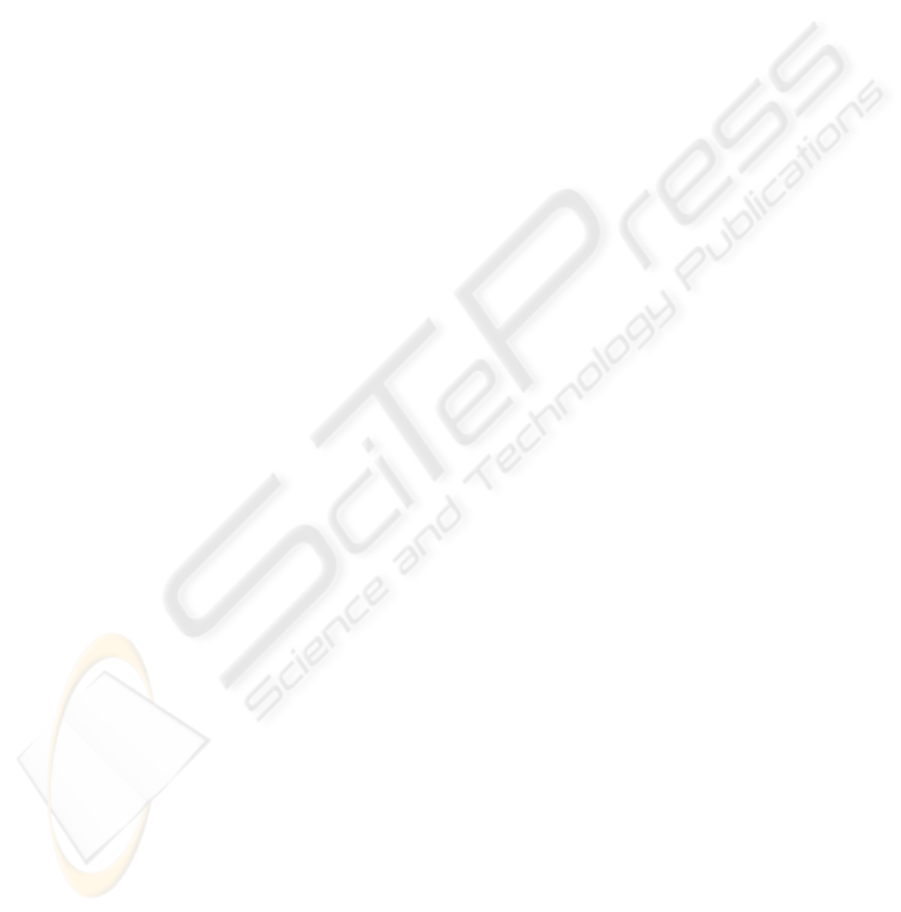
ands. This wearing phenomenon for viscoelastic materials does not have a clear and
exhaustive explanation due to the difficult to quantify the soft polymer coating the
hard islands. Making use of the image analysis based on drift compensation it is poss-
ible to reduce the drift in sequential AFM measurements and calculate with accuracy
the soft polymer volume moved by AFM tip. Our method is divided in two steps. In
the first one, we identify using a cross correlation function the residual thermal drift.
In the second step, we introduce a function connected to the thermal drift and a set of
specific parameter connected to low-order polynomial mapping function. The mini-
mization of such mapping function leads to the optimal parameters removing the
drifts from the sequence of the AFM images of viscoelastic sample using an useful
pattern recognition matching the images correspondent to same sample areas recorded
in different times. Our proposed method should become a powerful tool for the accu-
rate analysis of stressed viscoelastic surface and accurate quantification of AFM mul-
tichannel measurements.
2 Numerical Methods for Image-based Adaptive Drift
Compensation
The possibility of investigation of surface properties of viscoelastic materials using
AFM is based essentially on a sequence of scans on the same area to be observed.
The interpretation of data is complicated by two main factors: i), the presence of
drifts does difficult to compare AFM images acquired in different times on the same
sample location; ii), the accurate identification of specific morphological deforma-
tions of viscoelastic materials due to stressing tip resulting in a modified sequential
images with respect to the first primitive image, so leading to misinterpreted data.
Since AFM generates multiple image channels simultaneously, the spatial and tem-
poral correlation of patterns in these channels can substantially enhance the robust-
ness of the pattern detection and its position measurement, see appendix. Further-
more, the raster scanning of a probe across the same pattern back and forth embeds
asymmetric feedback control signatures for widely contact mode imaging. These
signatures provide a powerful tool to distinguish a true pattern from a set of noisy
data. Reliable pattern positioning data enable a precise adaptive control which should
achieve a sub-nanometer positioning accuracy over long period of time. The forward
scan (trace) and the reverse scan (retrace) of the same location also provide indepen-
dent information of the same patter location. In this paper, we will consider two
channels correspondent to the topographic data (first channel, quantitative data) and
surface elastic Young moduli data (second one) measured using the modulation force
AFM tool. The topographic data correspond to the height z=f(x,y) measured by the
AFM tip scanning the sample surface, see figure 5 (left). On contrary, the modulation
force channel measures in a qualitatively way the differences of surface elasticity.
Modulation force is a powerful tool for the knowledge of surface properties, never-
theless when the AFM is used for a time sequence scanning cycle on the same viscoe-
lastic sample area, it is strongly limited by its qualitatively nature.
We adopt a new method integrating a numerical corrections of thermal drifts with
pattern recognition imaging. A cross correlation function is used a priori as a method
69