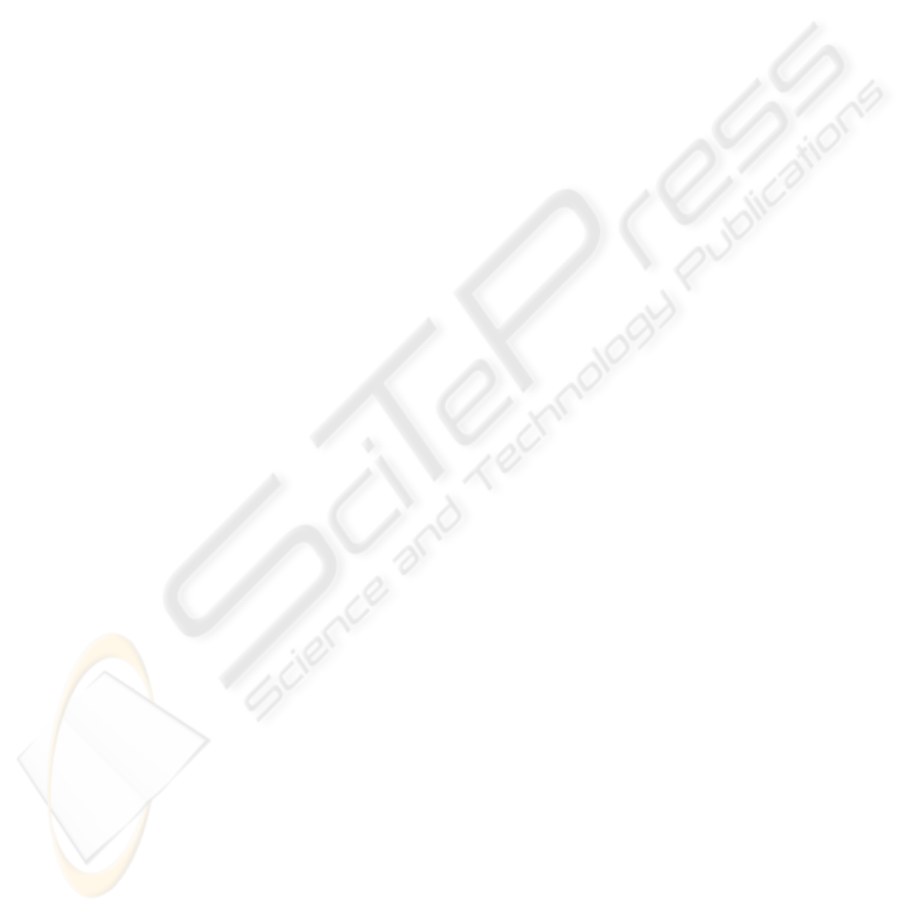
2 TROUBLESHOOTING:
TECHNOLOGIES AND ISSUES
Several technologies relying on Artificial Intelligence
and Decision Making have been proposed over the
time in order to support Troubleshooting activities.
Information Text Retrieval (ITR) systems became
popular in the 90s, especially with respect to docu-
ment management of products and S&M reporting.
Their main function is devoted to store in and retrieve
from a knowledgebase information regarding specific
problems, products, past repairing tasks.
A major limitation of this approach resides in the
amount of information that can be effectively man-
aged, as complex industrial products generally entail
a large number of retrievable data and documentation,
thus leading to an excess of information that hides the
actual needs and to read and understand documents
written by others. In addition, often information is not
self contained is one document or section, but split in
several parts, requiring ability in relating sources.
In order to overcome limitations of early ITR ap-
proaches, a more sophisticated class of tools rely on
Case Based Reasoning (CBR). In detail CBR process-
ing can be outlined considering only four main steps:
(i) retrieve: the user describes its problem submitting
it to the CBR system, obtaining a set of cases that sug-
gest which operations to take for solving the current
problem; (ii) reuse: retrieved cases can be re-used to
solve new problems; revise: a case used in the past is
tested against new problems; retain: new cases can be
compiled and retained in the CBR system.
Differently from ITR, users can provide more de-
tailed description of failure events mostly based on
symptoms, thus allowing to retrieve problems solved
in the past by similarity to the current one. This
approach is able to better model the human experi-
ence in problem solving, addressing the issue of re-
fining generic queries as shown by ITR. Therefore
CBR performs better when dealing with large knowl-
edge bases. However, they heavily rely on the case
description given by user in natural language, affect-
ing the quality of results as documents are indexed
by descriptions that can be imprecise, inaccurate and
erroneous.
Both ITR and CBR do not provide a structured
path to problem solution in order to automate Trou-
bleshooting. This led to employ Decision Trees (DT)
to assist S&M operators in taking repairing actions.
DT are able to drive maintenance operations by mod-
eling decision paths and their possible consequences,
including resource costs, utilities, chance event out-
comes and other factors.
Often this approach requires domain experts to de-
sign and validate the tree structure, although param-
eters can be obtained by training the model against
statistical data. During troubleshooting, users can re-
trace the structure, following suggested decisions un-
til the problem is solved. Modeling decision trees
becomes quickly cumbersome and maintaining them
very complex and error prone, especially for unexpe-
rienced users. Human experience still plays a rele-
vant role in keeping up-to-date this kind of models, as
modifications can invalidate the structure producing a
high impact on model maintenance costs.
Maybe Expert Systems (ES) have been the most
widely approach investigated and applied to Trou-
bleshooting. An expert system attempts to solve a
problem by explicitly modeling knowledge and infer-
ring solutions by causal reasoning as human would
do. For this reason, they are generally specific to do-
mains. In using this kind of tools, (i) creation of a
knowledge base is made by capturing the expert’s do-
main knowledge, and (ii) solutions are found by log-
ically inferring conclusions given a set of collected
premises. This leads to have white-box models, thus
more intelligible, while other techniques mainly pro-
vide black-box models. Other advantages are consis-
tent answers for repetitive decisions, robust theoreti-
cal framework in decision making, improved user ex-
perience, and reduced management cost.
Main limitations regard impossibility of obtain-
ing creative and unsuspected responses, as human ex-
perts generally are able to provide. Quality of results
depends on quality of knowledge encoded when the
model is designed, thus often leading to errors and
wrong decisions due partial knowledge. Complex and
dynamic problems are difficult to encode.
3 BAYESIAN APPROACH
Technologies presented so far share in common some
limitations that can be summarized as follows:
1. Troubleshooting inherently deals with uncer-
tainty, as malfunctioning causes cannot be deter-
ministically identified even by humans. Instead
most of outlined approaches make the link be-
tween symptoms and causes deterministic.
2. They generally do not employ a divide-et-conquer
strategy, thus badly fitting real world systems,
made of complex aggregations of parts, each able
to affect correct functioning of the whole system
or of other parts.
3. As knowledge is hard-embedded, models are dif-
ficult to maintain and evolve.
SUPPORTING COMPLEXITY IN MODELING BAYESIAN TROUBLESHOOTING
345