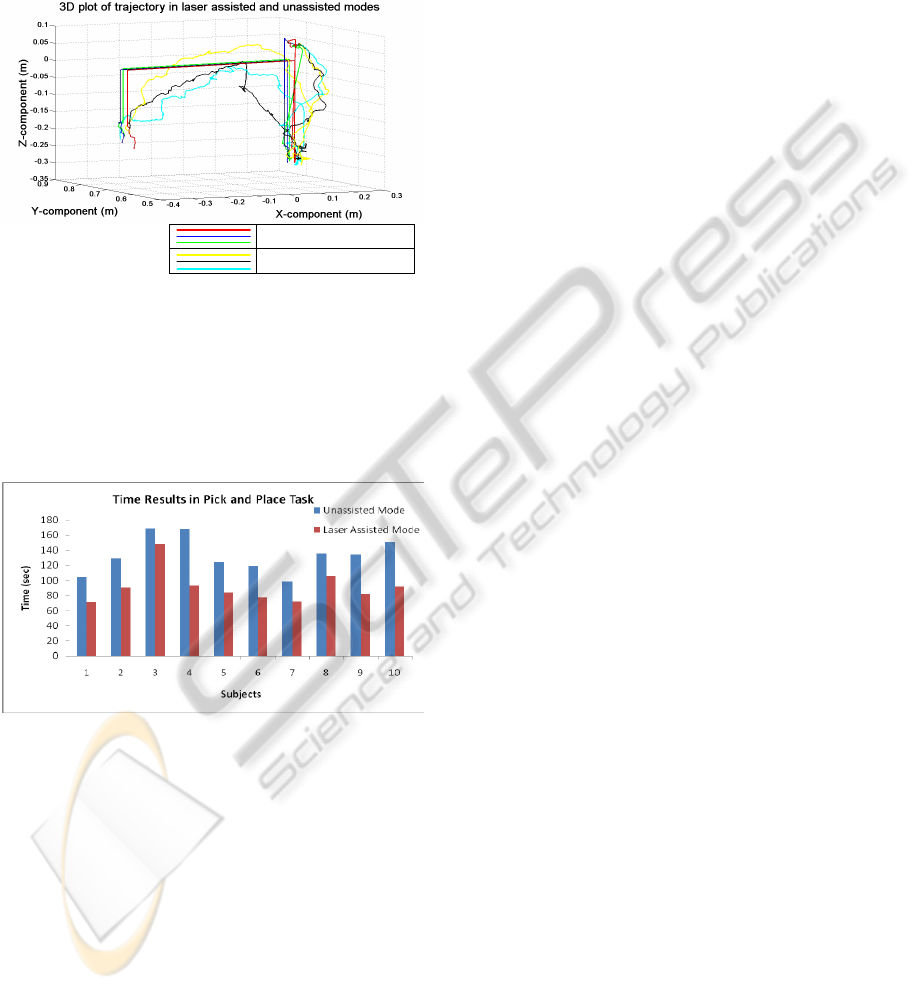
the PUMA without any assistance. The loops around
the pick-up point are due to subjects repeatedly
trying to orient the gripper properly so that it is in a
convenient configuration for grasping. Orienting the
arm properly was one of the most challenging
activities the subjects faced.
Laser Assisted Modes
Unassisted Modes
Figure 5: Accuracy in path traversal for laser assisted and
unassisted modes.
The average time per subject per mode was
computed and is presented in the form of plots in
Fig. 6. We observe that each subject spent more time
to complete the task in the unassisted mode than in
the laser assisted mode.
Figure 6: Time plots in executing pick and place task.
The user experience in executing the task in the
two modes was also noted. The users preferred the
laser assisted mode as generating task plans by
picking up points with the laser was easier for them
and the robot executed the task. In teleoperating
without assistance they experienced a lot of mental
load.
5 CONCLUSIONS
Our hypothesis that the laser assisted telerobotic
control methodology of task execution would
improve the task performance and reduce the mental
load on the users has been validated by tests on
healthy subjects on a pick and place task. The task
performance in terms of time and accuracy improved
and the subjects were overwhelmingly in favour of
using the laser assisted mode in executing the task as
they experienced less cognitive load. With the
results obtained we believe that this telerobotic
system would make it possible for persons with
disabilities to execute ADL tasks with much greater
ease. Next we intend to test the method on persons
with disabilities and for a variety of ADLs.
REFERENCES
Bolmsjo, G., Neveryd, H., Eftring, H. (1995). Robotics in
Rehabilitation. IEEE Transactions on Rehabilitation
Engineering. 3(1), 77 -83.Hasegawa, T., Suehiro, T.
and Takase, K. (1991). A Robot System for
Unstructured Environments Based on an Environment
Model and Manipulation Skills. IEEE International
Conference on Robotics and Automation (Vol. 1, pp.
916-923).
Nguyen, H., Anderson, C., Trevor, A., Jain, A., Xu, Z. and
Kemp, C. (2008). El-E: An Assistive Robot that
Fetches Objects from Flat Surfaces. The Robotic
Helpers Workshop at HRI.
Pernalete, N., Yu, W., Dubey, R. and Moreno, W. (2002).
Development of a Robotic Haptic Interface to Assist
the Performance of Vocational Tasks by People with
Disability. IEEE International Conference on Robotics
and Automation. (Vol. 2, pp. 1269-1274).
Takahashi, Y. and Yashige, M. (2000). Robotic
manipulator operated by human interface with
positioning control using laser pointer. IEEE 26th
Annual Conference of the Industrial Electronics
Society (Vol. 1, pp. 608-613).
Tarn, T., Xi, N. and Guo, C. (1996). Task-Oriented
Human and Machine Co-Operation in Telerobotic
Systems. Annual Reviews in Control. (Vol. 20, pp.
173-178).
Yu, W., Alqasemi , R., Dubey, R. and Pernalete, N.
(2005). Telemanipulation Assistance based on Motion
Intention Recognition. IEEE International Conference
on Robotics and Automation. (pp. 1121-1126).
LASER BASED TELEROBOTIC CONTROL FOR ASSISTING PERSONS WITH DISABILITIES PERFORM
ACTIVITIES OF DAILY LIVING
449