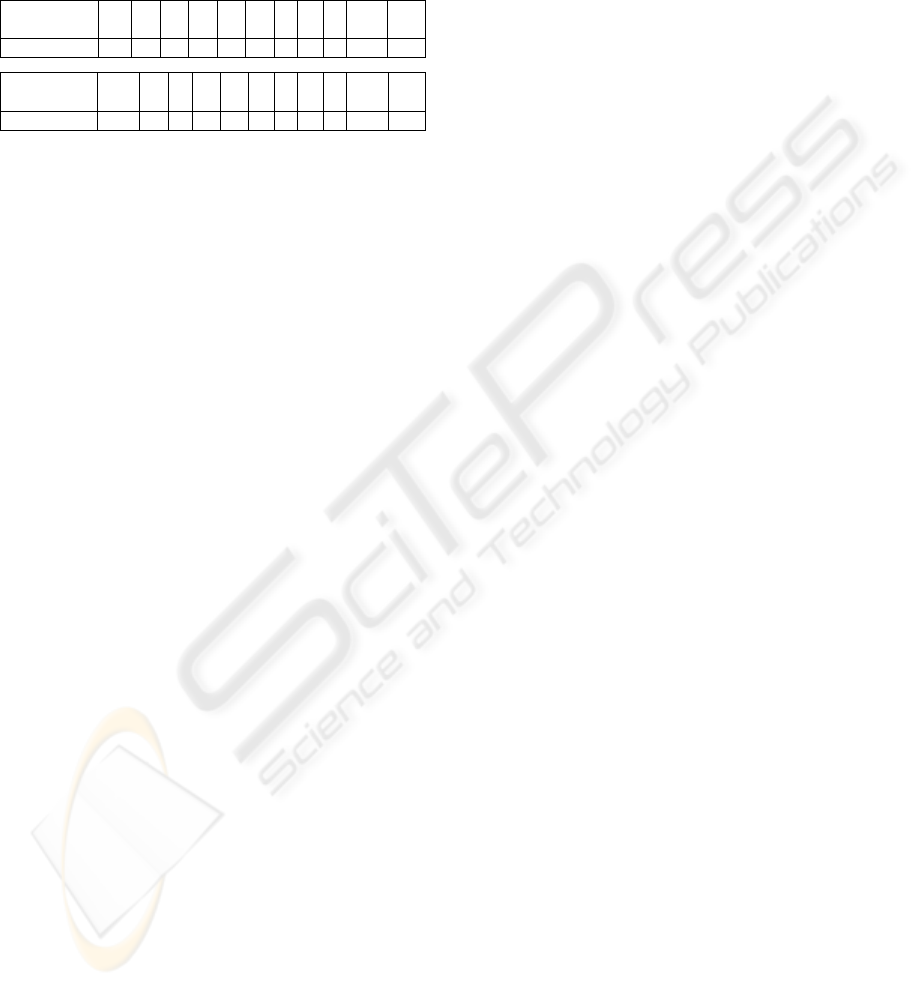
00 01 02 03 04 05 06 07 08 09 10
1.44 1.85 1.64 3.71 0.58 2.76 3.46 3.00 1.82 3.55 1.51
1.90 3.15 2.34 0.86 2.52 1.49 1.86 2.88 1.14 1.62 3.22
CCCCCCCCCCC
PM
Figure 5: The Numerical values of the position matrix of
the PSO solution.
Assembly
sequence
1 2 3 4 5 6 7 8 9 10 11
Component 7 2 5 6 4 1 0 9 8 3 10
Disassembly
sequence
1 2 3 4 5 6 7 8 9 10 11
Component 10 8 3 9 0 1 4 5 2 7 6
Figure 6: The final test results of the integrated assembly
and disassembly sequences.
It is observed that the combinatorial number of
sequences increases as the component number
grows. It can be concluded in general, the PSO
method can be considered an efficient and effective
method for find the solutions of integrated assembly
and disassembly sequences. Although the presented
methods can be useful for generating and evaluating
feasible sequences with good solutions, much
remains to be done to manage more complicated
products with a large number of components.
Further research on the complexity issues need to be
conducted.
6 CONCLUSIONS
In this research, a green decision support system is
presented to integrate assembly and disassembly
sequence planning models. First, graph-based
models are built by analyzing the spatial
relationships of the components and the operations.
Second, a solution method using a PSO approach is
applied to search for the good assembly sequence
and disassembly sequence. A new encoding scheme
of position matrix is developed for representing a
particle. A cost function by integrating the assembly
costs and disassembly costs is formulated. An
example product is illustrated in this paper. The test
results show that the PSO method converges within
a small number of generations with a near optimized
low cost. It can be generally concluded that the
developed model in the decision support system is
feasible and efficient for integrating assembly and
disassembly sequence planning. The green decision
support system is capable of finding complete
assembly and disassembly sequences with a near
optimized low cost. In further research, more
detailed assembly and disassembly cost functions
can be further explored. The solution method can be
refined to enhance the solution speed.
REFERENCES
Abdullah, T. A., Popplewell, K., and Page, C. J. (2003). A
review of the support tools for the process of assembly
method selection and assembly planning, International
Journal of Production Research, 41(11), pp. 2391–
2410.
Banks, A., Vincent, J., and Anyakoha, C. (2008). A review
of particle swarm optimization. Part II: hybridization,
combinatorial, multicriteria and constrained
optimization, and indicative applications, Natural
Computing, 7, 109-124.
Chen, R. S., Lu, K.-Y., and Tai, P. H. (2004). Optimizing
assembly planning through a three-stage integrated
approach, International Journal of Production
Economics, 88, pp. 243-256.
Gottipolu, R. B., and Ghosh, K. (1997). Representation
and selection of assembly sequences in computer-aided
assembly process planning, International Journal of
Production Research, 35(12), pp. 3447-3465.
Gungor, A., and Gupta, M. (2001). Disassembly sequence
plan generation using a branch-and-bound algorithm,
International Journal of Production Research, 39(1),
pp. 481-509.
Homem de Mello, L. S., and Sanderson, A. C. (1991).
Two criteria for the selection of assembly plans:
maximizing the flexibility of sequencing the assembly
tasks and minimizing the assembly time through
parallel execution of assembly tasks, IEEE Transactions
on Robotics and Automation, 7(5), pp. 626-633.
Huang, Y. M. and Huang, C. T. (2002). Disassembly
matrix for disassembly processed of products,
International Journal of Production Research, 40(2),
pp. 255- 273.
Kennedy, J., and Eberhart, R. C. (1997). A discrete binary
version of the particle swarm algorithm, Proceedings of
the International Conference on Systems, Man and
Cybernetics, Piscataway, NJ, 4104-4109.
Kongar, E., and Gupta, S. M. (2006). Disassembly
sequencing using genetic algorithm, International
Journal of Advanced Manufacturing Technology, 30,
pp. 497-506.
Lambert, A. J. D. (2003). Disassembly sequencing: a
survey, International Journal of Production Research,
41(16), pp. 3721- 3759.
Laperriere, L., and ElMaraghy, H. A. (1996). GAPP: A
Generative Assembly Process Planner, Journal of
Manufacturing Systems, 15(4), pp. 282-293.
Lin, A. C., and Chang, T. C. (1993). An integrated
approach to automated assembly planning for three-
dimensional mechanical products, International Journal
of Production Research, 31(5), pp. 1201-1227.
Torres, F., Puente, S. T., and Aracil, R. (2003).
Disassembly planning based on precedence relations
among assemblies, International Journal of Advanced
Manufacturing Technology, 21, pp. 317-327.
A GREEN DECISION SUPPORT SYSTEM FOR INTEGRATED ASSEMBLY AND DISASSEMBLY SEQUENCE
PLANNING USING A PSO APPROACH
449