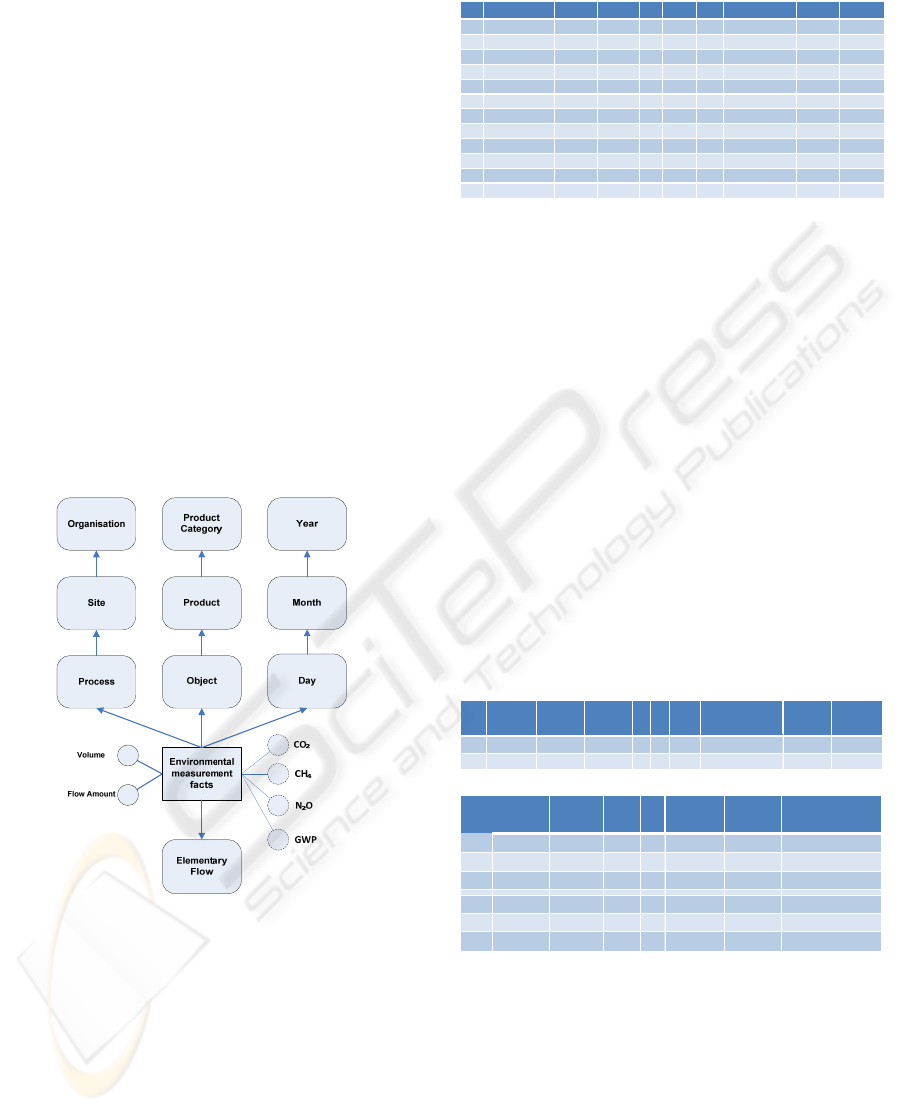
The relation model in Figure 3 can be easily
extended to include more product and supply chain
specific information. For example, we can
implement an organisational hierarchy by creating
Process, Site and Organisation relations
(Node→Process → Site→ Organisation).
This kind of extension enables analysis of
environmental data by using the hierarchy as a
dimension in multidimensional OLAP model.
5 TRACEABILITY CUBE
To be able to use the OLAP type operations for
analyzing the information of the traceability graph
we must combine the previous tables as a data cube.
In this work we will use the multidimensional data
model “MD” that is presented in (Torlone, 2003). In
Figure 4 the dimensions are presented as round-
cornered boxes, the facts are presented as boxes and
the measures as circles. The circles with drawn with
dashed line presents calculated measures.
Figure 4: Traceability cube scheme.
Figure 4 presents the traceability cube with some
example dimensions. The Process dimension can
be used to compare the environmental impact
between manufacturing sites and manufacturers. The
Object dimension is used to aggregating the
environmental data for different product groups. The
measure Flow Amount is the attribute amount for
an object. The measure Volume specifies the
volume of an object. In Table 1 some sample
instances over the traceability cube are presented.
The EPC column is the unique identity of an
object.
Table 1: A sample instance over the traceability cube.
The Flow Amount is used for calculating the
calculated measures – amount of emissions (e.g.
carbon dioxide, methane, nitrous oxides) and
amount of key environmental performance
indicators (see e.g. Lim and Park, 2009). The
emission amount is the amount of emissions caused
when using elementary flow (raw material or
energy) in some process. For example, carbon
dioxide emissions when using electricity from
Tampere electricity station in Finland were 194 g /
kWh in the year 2008. There are many
environmental databases that comprise life cycle
inventory data from different supply chain
processes. For example, the ELCD core database by
European Commission - DG Joint Research Centre -
Institute for Environment and Sustainability
comprises more than 300 process datasets (e.g. key
materials, energy carriers, transport, and waste
management).
Table 2: Emission and Impact Calculation.
↓
In Table 2 the emissions and impact category for
objects with code 2 and 4 are presented. Key
environmental performance indicators are calculated
based on the emissions. In this example we use the
global warming potential which is one commonly
used an environmental key performance indicator. It
is calculated based on carbon dioxide, methane,
nitrous oxide and several other emissions. The
measurement unit for the global warming potential is
kg of carbon dioxide equivalent which means that all
the other emissions are converted by using a
EPC Process Site Product Day Month Year
Flow Amount
Volume
1KilnDrying Mill#1 Timber 1 1 2010 Electricity 0,5kWh 0,30m³
2KilnDrying Mill#1 Timber 1 1 2010 Electricity 0,5kWh 0,35m³
3KilnDrying Mill#1 Timber 1 1 2010 Electricity 0,5kWh 0,33m³
1 Transporting Truck#1 Timber 2 1 2010 LorryTransport 100km 0,30m³
2 Transporting Truck#1 Timber 2 1 2010 LorryTransport 100km 0,35m³
3 Transporting Truck#1 Timber 2 1 2010 LorryTransport 100km 0,33m³
4KilnDrying Mill#1 Timber 1 1 2010 Electricity 0,53kWh 0,40m³
5KilnDrying Mill#1 Timber 1 1 2010 Electricity 0,53kWh 0,42m³
6KilnDrying Mill#1 Timber 1 1 2010 Electricity 0,53kWh 0,38m³
4 Transporting Train#1 Timber 2 1 2 010 RailTransport 20 0 km 0,40m³
5 Transporting Train#1 Timber 2 1 2 010 RailTransport 20 0 km 0,42m³
6 Transporting Train#1 Timber 2 1 2 010 RailTransport 20 0 km 0,38m³
EPC Process Site Product D M Year
Elementary
Flow
Flow
Amount
Volume
2 Transp. Truck#1 Timber 2 1 2010 LorryTransport 10 0 km 0,35m³
4 Transp. Truck#2 Timbe r 2 1 2010 RailTransport 200 km 0,40m³
EPC Emission Amount Unit
Impact
Category
Amount Unit
2CO₂ 19,9102 kg → GWP 19,9102 askgofCO₂eq.
2CH₄ 0,19636 g → GWP 0,004909 askgofCO₂eq.
2N₂O 0,15401 g → GWP 0,045895 askgofCO₂eq.
4CO₂ 22,1193 kg → GWP 22,1193 askgofCO₂eq.
4CH₄ 0,13933 g → GWP 0,003483 askgofCO₂eq.
4N₂O 8,63872 g → GWP 2,574338 askgofCO₂eq.
DATA MANAGEMENT FRAMEWORK FOR MONITORING AND ANALYZING THE ENVIRONMENTAL
PERFORMANCE
61