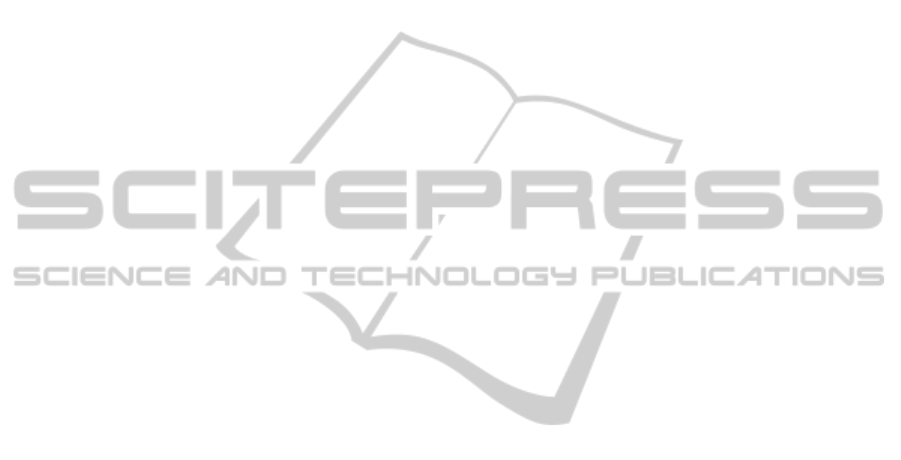
The advantages are twofold. First, physically cor-
rect simulated robots can be compared with their real
counterparts using the same “brain“. Thus, no code
written for the robot simulator LPZROBOTS needs to
be changed or adapted regarding to self-organizing
neural networks. Second, it allows to use the com-
putational power of a standard desktop PC as well
as easy to deploy extensions or off-the-shelf analysis
tools.
The THREECHAINED TWOWHEELED robot ex-
ample demonstrated the PLUG&LEARN architecture
shows that similar behaviours can be observed in as
reality as in simulation, but with difficulties. These
are caused by the differences between the simulation
and the reality. This implies that it is essential to use
real robots in order to proof theoretical concepts gath-
ered with the simulation. The PLUG&LEARN archi-
tecture minimizes the differences between the simu-
lation and reality to a level whereas a comparison be-
tween simulated and real robots are possible.
As for example, the PLUG&LEARN architecture
is used to drive an artificial human hand (Franke and
Bogdan, 2009). The task is to control this hand with
a self-organizing neural network in order to get emer-
gent motions from which Postures can be derived. A
simulated counterpart in LPZROBOTS is used to proof
theoretical concepts which are then tested with the
real artificial human hand.
A task for future research is to investigate if e.g.
the information theoretical aspects considered in (Der
et al., 2008) can also be measured for the real coun-
terpart or the centralized control involves the same be-
havioural results as with decentralized control.
REFERENCES
Ay, N., Bertschinger, N., Der, R., G
¨
uttler, F., and Olbrich,
E. (2008). Predictive Information and Explorative Be-
havior of Autonomous Robots. The EPJ B - Con-
densed Matter and Complex Systems, 63(3):329–339.
Bergbreiter, S. and Pister, K. (2003). CotsBots: An Off-the-
Shelf Platform for Distributed Robotics. IROS 2003.
Chung, D., Hirata, R., Mundhenk, T. N., Ng7, J., Peters,
R. J., Pichon, E., Tsui, A., Ventrice, T., Walther, D.,
Williams, P., and Itti, L. (2010). A New Robotics Plat-
form for Neuromorphic Vision: Beobots, volume 2525
of Lecture Notes in Computer Science, pages 325–
340. Springer Berlin/Heidelberg.
Der, R., G
¨
uttler, F., and Ay, N. (2008). Predictive Informa-
tion and Emergent Cooperativity in a Chain of Mobile
Robots. In Artificial Life XI. MIT Press.
Der, R., Martius, G., Gttler, F., Herrman, M., and Hesse,
F. (2010). Videos of Self-Organized Robot Behavior.
http://robot.informatik.uni-leipzig.de/videos.
Franke, M. and Bogdan, M. (2009). A New Lightweight,
Robust and Forceful Finger for an Artificial Limb.
WC2009 - MEDICAL PHYSICS AND BIOMEDICAL
ENGINEERING, pages 339–342.
Gttler, F., Rabe, W., and Bogdan, M. (2010).
Videos of THREECHAINED TWOWHEELED
robot showing Self-Organized Robot Behavior.
http://robot.informatik.uni-leipzig.de/Videos/PLA/
TCTW.
Hesse, F. (2009). Self-Organizing Control for Autonomous
Robots. A Dynamical Systems Approach Based on
the Principle of Homeokinesis. PhD thesis, Georg-
August-Universit
¨
at G
¨
ottingen.
Lichtensteiger, L. (2003). The Need to Adapt and Its Impli-
cations for Embodiment. In Embodied Artificial Intel-
ligence, pages 98–106.
Lungarella, M. and Sporns, O. (2005). Information self-
structuring: Key principle for learning and develop-
ment. In Proceedings 2005 IEEE Intern. Conf. Devel-
opment and Learning, pages 25–30.
Martius, G. (2010). Goal-Oriented Control of Self-
Organizing Behavior in Autonomous Robots. PhD the-
sis, Georg-August-Universit
¨
at G
¨
ottingen.
Martius, G., Der, R., and Gttler, F. (2007). LpzRobots
- Simulation Tool for Autonomous Robots.
http://robot.informatik.uni-leipzig.de/software.
OpenSource-Community (2008). Player/Stage/Gazebo -
free software tools for robot and sensor applications.
http://playerstage.sourceforge.net.
Pfeifer, R. and Bongard, J. (2006). How the Body Shapes
the Way We Think. A New View of Intelligence. MIT
Press.
Pfeifer, R. and Scheier, C. (1999). Understanding Intelli-
gence. MIT Press,Cambridge, MA.
Schmidhuber, J. (1990). A possibility for implementing
curiosity and boredom in model-building neural con-
trollers. In Proceedings of the first international con-
ference on simulation of adaptive behavior on From
animals to animats, pages 222–227, Cambridge, MA,
USA. MIT Press.
Smith, R. (2005). Open Dynamics Engine. http://ode.org/.
Tschacher, W. and Dauwalder, J. (2003). The Dynamical
Systems Approach to Cognition: Concepts and Empir-
ical Paradigms Based on Self-Organization, Embodi-
ment, and Coordination Dynamics. World Scientific
Publishing Company, Singapore.
Vamplew, P. (2004). Lego Mindstorms Robots as a Platform
for Teaching Reinforcement Learning. In AISAT2004,
Hobart, Australia.
Wolf, J., Vicente, A., Gibbons, P., Gardiner, N., and Tilbury,
J. (2009). BunnyBot: Humanoid Platform for Re-
search and Teaching. Buch Progress in Robotics,
44:25 – 33.
TRANSPOSING SIMULATED SELF-ORGANIZING ROBOTS INTO REALITY USING THE PLUG&LEARN
ARCHITECTURE
357