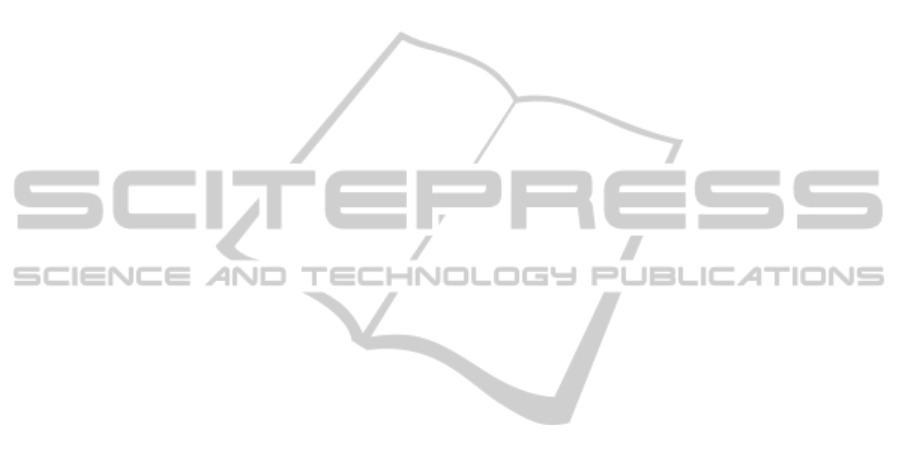
can be produced either just-in-time in small
lots or at fixed, short intervals.
• A reduction in flow time is obtained. Reduced
material handling time and reduced setup time
greatly reduce flow time.
• Tool requirements are reduced. Parts produced
in a cell are of similar shape, size, and
composition. Thus, they often have similar
tooling requirements.
• Throughput times are reduced. In a job shop,
parts are transferred between machines in
batches. However, in CM each part is
transferred immediately to the next machine
after it has been processed. Thus, the waiting
time is reduced substantially.
As a result of these characteristics, product
quality is also improved: As the parts are transported
individually from one work center to another within
the cell, the feedback is immediate and the process
can be stopped whenever any errors may occur.
5 CONCLUSIONS
Summarizing the above results presented with the
study performed we may highline that several kind
of advantages were able to be reached throughout
the implementation of the proposed work. These
advantages are mainly related to wip and inventory
costs reduction, throughout decreasing the number
of kanbans necessary, under the scope of Lean and
JIT production principles, with are being used in
Bosch Production System.
Another important improvement obtained was
due to the proposed cellular manufacturing system
scenario, instead of the existing line system.
Therefore, it is possible to enhance the production
system, by improving the production flow and
consequently the production tasks management.
Moreover it is possible to simplify materials
acquisition and storage. Besides that, material
handling and control is also simplified.
As a final conclusion we may state that kanbans
sharing and minimization was possible through a
manufacturing system layout change and
improvement, by transforming lines to cellular
manufacturing system. Thus, improving several
other related aspects in the BPS, related to a better
production system arrangement and materials and
production flow, also enabling to facilitate the
production planning and control tasks and material
acquisition, storage, manipulation and control.
Moreover, this study consists on another
contribution in the Lean, JIT and kanban domain
showing that these principles enable to better control
production process, enabling better tasks
performance and enhance productivity and
production quality in manufacturing environments,
by enabling better work integration among
operators, through a closer interaction and
information and responsibility sharing, which is a
clear achievement within the proposed
manufacturing cell. As a consequence, reduced
production time and material and wip flow is also
reached, through the reduction of waste and
distances between work centres within the
manufacturing system, which was also visible in the
proposed manufacturing cell.
REFERENCES
Askin, R. G. and Standridge, S. R. 1993. Modeling and
analysis of manufacturing systems, John Wiley and
Sons, 461.
Baker, K. R. and Trietsch, D. 2009. Principles of Se-
quencing and Scheduling, Jonh Wiley and Sons, 493.
Black, J. T. 1991. The design of the factory with a future,
McGraw-Hill, 233.
Cheng, K., Harrison, D. K., Pan, P. Y. 1998. An internet
based architecture of implementing design and
manufacturing agility for rolling bearings. J Mater
Process Technology 76(1–3):96–101.
Hirano, H. 2009. JIT Implementation Manual - The
Complete Guide to JIT Manufacturing: Vol 1 - The
JIT Production System, CRC Press, 5 Ed, 192.
Hyer, N. 1984. The potential of group technology for U.S.
manufacturing. Journal of Operations Management,
4(3):183-202.
Kidd, P. T. 1995 Agile manufacturing – forging new fron-
tiers. Addison-Wesley, Wokingham, England, UK.
Levy, D. L. 1997. Lean production in a international
supply chain. Sloan Management Review.
Ming P. Tsai, James T. Lin. 2004. A web-based control
system. Springer-Verlag, London.
Monden, Y. 1993. Toyota Production System: An
integrated approach to Just-In-Time, Industrial
Engineering and Management Press, 2 Ed, 423.
Mortimer, A. L. 2008. A continuing lean journey: an
electronic manufacturer’s adopting ok kanban.
Assembly Automation, 28/2, 103-112.
Ohno, T. 1988. Toyota Production System: Beyond Large-
Scale Production, Productivity Press, 143.
Shingo, S. 1989. A study of the Toyota Production System
from an Industrial Engineering viewpoint, Productivity
Press, 257.
Singh, N. and Rajamaani, D. 1996. Cellular
Manufacturing Systems: Design, Planning and
Control, Chapman and Hall, 277.
Slack, N., Chambers, S. and Johnston, R. 2007. Operations
Management, Pearson Education, 5 Ed, 728.
KMIS 2010 - International Conference on Knowledge Management and Information Sharing
90