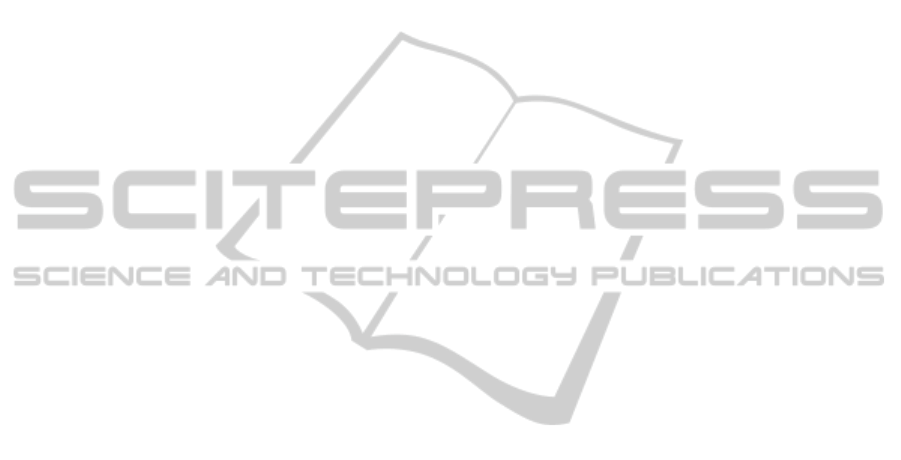
technology. By a direct measurement of the actual
surface temperature an effectively working control
of the heating system can be realized. Therefor a
photo semiconductor is integrated in the tube.
Temperatures from about 700° C can
be
measured pyrometrically with photo diode in the
visible spectral range. Pyrometers (sensor incl.
evaluation system), also called radiation
thermometers, are used for contactless temperature
measurement. Mostly the reception wavelength
range of high-temperature pyrometers is determined
by the photo detector: The lowest reception
wavelength of silicon photodiodes is, for example,
about 1.1 microns. A body with a temperature of
3000 K has its maximum radiation, but temperatures
from about 700° C can already be measured.The
surface temperatures in klystrons, magnetrons,
thyratrons and accelerators range from 890° C to
1050° C (depending on the type of cathode, ie oxide
or impregnated). The surface temperature of the
tungsten filament wire in x-ray tubes is about 2000°
C.
To prevent deposition of evaporated electron
emitting material of the cathode on the cold surface
of the photo sensor (in klystron, magnetron,
thyratron and accelerator), a central lock (a so-called
shutter) is used.
The shutter consists of a number of
curved steel plates, which will be steered out of the
measurement beam. Such shutters are well known in
the camera technology and are available in high
volumes at low prices. The shutter protects the
sensor optics in phases, in which no measure is
taken. To measure the surface temperature, the
shutter, which is located in a vacuum, is activated
and opened electromagnetically from the outside
through a media gap (barrier of glass or ceramic
between the vacuum of the tube and the ambient
pressure). After measurement, the shutter is closed
again. The measurement itself takes place cyclically,
in time intervals still to be defined in detail. Also
usable as a shutter is a disc with an opening which
rotates when activated and releases the beam path to
the sensor.
The advantages for the use of standard integrated
optical measuring equipment for continuous cathode
or anode surface temperature measurement in
vacuum tubes are the reliable service life prediction
and the targeted life extension. With the help of the
exact measurement of surface temperature, the state
(electron emission at currently supplied heating
power) of the cathode can be detected and be used to
determine a precise heating control. The result of an
exact sequence for a heating system is the significant
extension of the life of a tube. Here the following
advantages of the invention compared to a contact
temperature measurement appear:
Very fast measurement (<1 ms to 10 ms
depending on construction). Very long, continuous
ranges possible (eg, 350 ... 3500° C), no wear (excl.
shutter mechanics), no temperature influence on the
measurement object or errors by poor thermal
contact. Possibility of measurement at high voltages,
electromagnetic fields, or corrosive materials.
The proposed novel approach allows continuing
an ongoing monitoring of the condition of the tube.
Slowly impending loss (reducing the temperature at
constant heating power supply) can be detected, an
integration of evaluation into the overall control of
the entire system allows sending of service messages
before the system fails (predictive maintenance).
With the known evaporation rate and the available
quantity of barium in the cathode from the
beginning, an arcing probability can be calculated
(Heuermann, 2009, 2010).
3 CONCLUSIONS
In the field of high-power tubes there is a large
development potential regarding service life
management and condition monitoring services to be
found.
A targeted control of the service life-determining
parameters extends the life of high-power tubes. As
proof of a life extension a simulation model is used,
which provides information about the behavior of
service life-critical parameters. Results produced by
the simulation model are transferable to reality and
can be used in a practical implementation. The
simulation shows that a targeted control of service
life-determining parameters influences the overall
lifetime of a tube. In a next step, real load profiles
recorded at customer sites will drive the tube model.
These reflect the daily routine in a hospital with the
individual patient distribution and their diagnostic
and therapy schedules and, as a result, the real tube
load. This novel approach will improve the uptime
of medical systems. First results from single x-ray-
tube systems (CT, Angiography, Fluoroscopy,
Mammography) show that in case of direct heated
cathodes the predictive maintenance works well. In
case of multiple tube systems like radiation therapy
machines, at least three high power tubes are used in
one system, the proposed specific methods for life
extension of equipment and systems in medical
devices will increase the uptime dramatically.
LIFETIME MANAGEMENT SYSTEMS FOR MEDICAL DEVICES - Specific Methods for Life Extension of Equipment
and Systems in Medical Devices
305