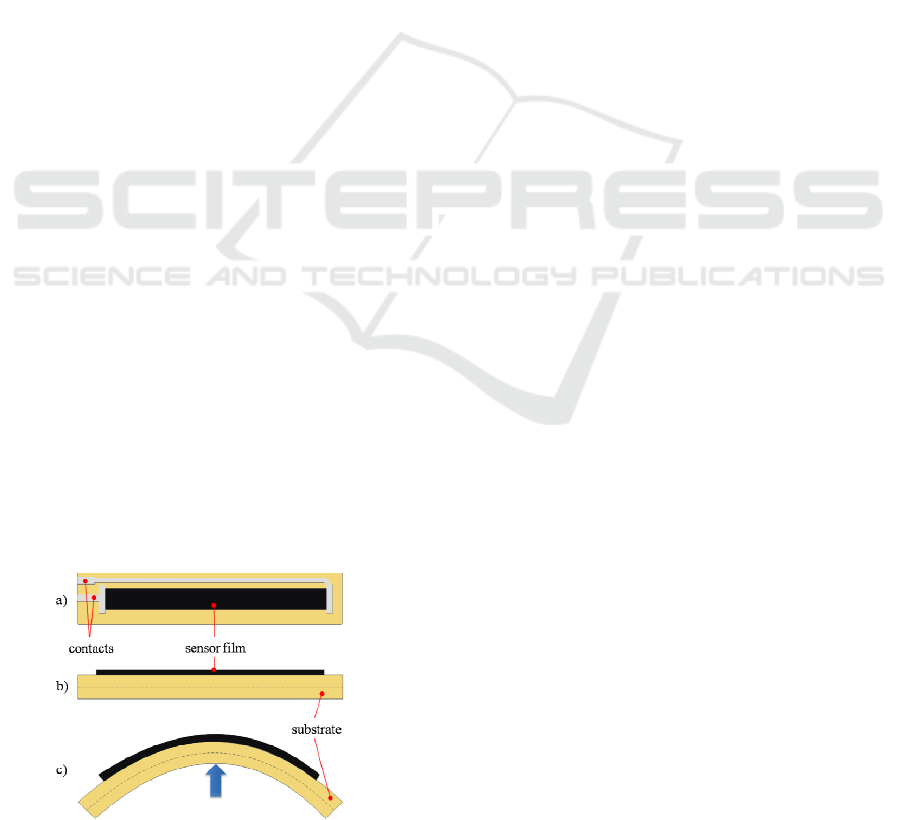
NON UNIFORM GEOMETRY BEND SENSORS EXPLOITED
FOR BIOMEDICAL SYSTEMS
Giovanni Saggio, Stefano Bocchetti, Carlo Alberto Pinto, Giuseppe Latessa and Giancarlo Orengo
Dept. of Electronic Engineering, University of Rome “Tor Vergata”, Rome, Italy
Keywords: Bend sensors, Human postures, Data glove, Linearization.
Abstract: In biomedical systems the bend sensors have been increasingly used stands their interesting properties
useful to measure human joint static and dynamic postures. These commercially available sensors are
usually made of a polyester film printed on with a special carbon ink. The film acts as a support while the
ink’s resistance value changes with bending dues to an applied external force. The substrate film material is
usually made by Kapton and/or Mylar for their properties, stands the fact that substrate must be able to bend
repeatedly without failure for the sensor to work. In spite of their interesting properties the commercial bend
sensors have a resistance vs. bent angle characteristic which is not actually ideal as a linear function, to
measure human postures, would be. So we introduce here a novel solution useful to linearize the sensor
response.
1 INTRODUCTION
Commercial bend sensors are usually made of a few
micrometer tick resistive material deposited onto a
thicker plastic insulating substrate. The overall
thickness is anyway negligible compared to the total
largeness and lengthiness, giving to the sensor a
rectangular geometry, with one side somewhat larger
than the other.
Figure 1: Unbent sensor (a) top (b) lateral view and bent
sensor (c) with the sensible part elongated.
These devices can be adopted as sensors when
placed on human joints with the larger side bent
according to the joints.
From a characterization point of view, the model
which takes into account the mechanical aspect of
the sensor predicts a linear behavior of the electric
resistive variation with the bending angle (Saggio et
al., 2009). Even the Ohm’s law,
⁄
, with
resistivity, l length and S section, suggests that
when the lengthiness l of the resistive sensor
material increases due to bending (see Fig. 1),
supposing a constant value of , it must correspond
a linear increase of the value R.
Nevertheless an electrical characterization of the
sensors furnishes non linear characteristics.
2 SENSOR
CHARACTERIZATION
We measured the characteristic of several
commercial bend sensors thanks to an home made
set-up previously described (Saggio et al., 2009;
Orengo et al., 2009) and as a result we selected
sensors provided by Flexpoint Inc. In particular, we
investigated the 2 inches long Flexpoint non
encapsulated sensors, polyester encapsulated sensors
and polyimide encapsulated sensors.
The results of our measurements, reported in Fig.
2, demonstrated the non linear mentioned
characteristic. In particular the resistance variation is
greater for non encapsulated sensors stands their
higher flexibility.
389
Saggio G., Bocchetti S., Pinto C., Latessa G. and Orengo G..
NON UNIFORM GEOMETRY BEND SENSORS EXPLOITED FOR BIOMEDICAL SYSTEMS .
DOI: 10.5220/0003121203890392
In Proceedings of the International Conference on Bio-inspired Systems and Signal Processing (BIOSIGNALS-2011), pages 389-392
ISBN: 978-989-8425-35-5
Copyright
c
2011 SCITEPRESS (Science and Technology Publications, Lda.)