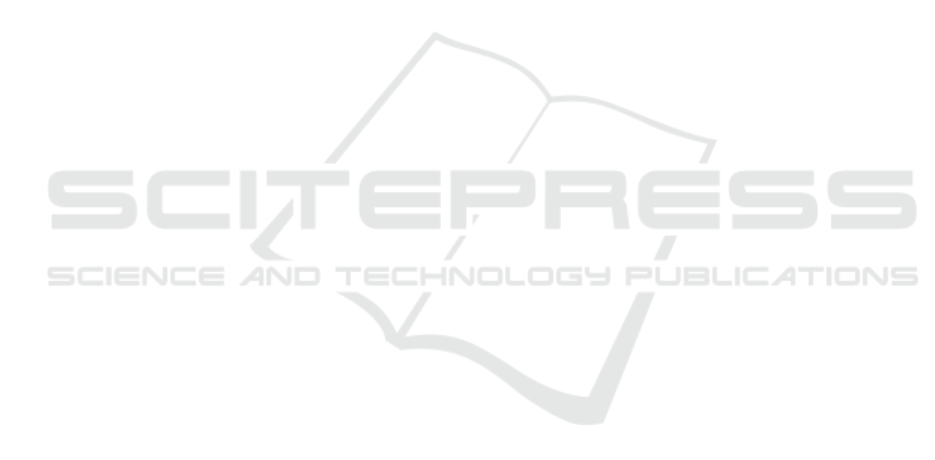
NOVEL PATTERNING TECHNOLOGY USING AIR-PRESSURE
DISPENSER FOR FABRICATING MICRO-FLUIDIC DEVICES
Toshiyuki Horiuchi, Shinichiro Otsuka, Miyu Ozaki, Ryota Ando and Kazunari Hiraki
Tokyo Denki University, 2-2, Kanda-Nishiki-Cho, Chiyoda-Ku, Tokyo, Japan
Keywords: Air-pressure dispenser, Micro-fluidic device, Micro-fluidic mixer, Micro-beaker, Direct writing,
Image reverse, Thick resist, Flow path.
Abstract: A novel method was developed to easily fabricate micro-fluidic devices with a low cost. It will be especially
useful at preliminary research stages. In the new method, inexpensive commercial air-pressure dispenser
was used. Adopting originally developed “wire nozzles”, it was verified that fine resist patterns with widths
down to 50 μm were successfully delineated. However, because patterns have to be delineated connecting
simple line patterns, it was difficult to delineate trench or hole patterns by painting out a large area.
Moreover, sidewalls of the delineated patterns were not sharp. For this reason, easy image-reverse process
was thought out. In the novel process, opaque liquid patterns were delineated using the dispenser on a thick
negative resist film coated on a substrate, and the resist film was exposed to flood exposure light. As a result,
the resist was sensitized except under the opaque liquid patterns. Therefore, trench or hole patterns
corresponding to the opaque liquid pattern shapes were obtained after developing the resist. Replicated thick
resist patterns have sharply-cut sidewalls, and will be durable for micro-fluidic paths or vessels of bio-
devices.
1 INTRODUCTION
Micro-reactors are useful for mixing a small quantity
of bio-medical liquid and chemical reagents. Even
simple micro-beakers without fluid paths are also
effective, because liquids are often sufficiently
mixed by leaving them for a time or shaking
appropriately. For this reason, various methods for
fabricating micro-reactors and micro-beakers are
proposed. Generally speaking, micro-reactor
trenches and micro-beaker holes are separately
fabricated on substrates in advance, and they are
capped or sealed afterwards. It is easiest as the seal
to put lid plates on the trenches and holes and bind
them. If the reactor or beaker materials are elastic,
the trenches and holes are easily but completely
sealed for the practical use. Such structures are
conveniently fabricated by patterning in thick films
of resists such as negative SU-8 (MicroChem)
(Horiuchi, T; Watanabe, H., Hayashi, N., Kitamura,
T., 2010) (Tsai, N. C.; Sue, C. Y., 2006), EPON
(Hexion Specialty Chemicals) (Yang, R.; Soper, S.
A., Wang, W., 2007) and positive poly-methyl-
methacrylate (PMMA) (Nugen, S. R.; Asiello, P. J.,
Connelly, J. T., Baeumner, A. J., 2009) using
lithography, or replicating the lithographically
fabricated resist patterns to plastic materials such as
Poly-dimethyl-siloxane (PDMS) (Lien, K. Y.; Liu, C.
J., Lee, G. B., 2008) (Casquillas, G. V.; Bertholle, F.,
Berre, M., Meance, S., Malaquin, L., Greffet, J. J.,
Chen, Y., 2008).
However, only a few amounts of micro-reactors
and micro-beakers are required at preliminary
research stages. In addition, required pattern sizes
are as large as around 100 μm. Accordingly,
expensive lithography tools such as steppers and
mask aligners are unsuitable from a view point of
costs.
Moreover, to decide the best features, structures
and sizes of the required devices, various candidates
should be compared in the research. However,
reticles and masks are also expensive and it takes at
least a few days to prepare them.
Under these situations, direct writing using a
dispenser is expected as a new patterning technology
for making a breakthrough. Here, a newly developed
process is investigated for fabricating various micro-
fluidic patterns using an air-pressure dispenser with
special nozzle (Otsuka, S; Horiuchi, T., 2010).
114
Horiuchi T., Ohtsuka S., Ozaki M., Ando R. and Hiraki K..
NOVEL PATTERNING TECHNOLOGY USING AIR-PRESSURE DISPENSER FOR FABRICATING MICRO-FLUIDIC DEVICES.
DOI: 10.5220/0003125701140119
In Proceedings of the International Conference on Biomedical Electronics and Devices (BIODEVICES-2011), pages 114-119
ISBN: 978-989-8425-37-9
Copyright
c
2011 SCITEPRESS (Science and Technology Publications, Lda.)