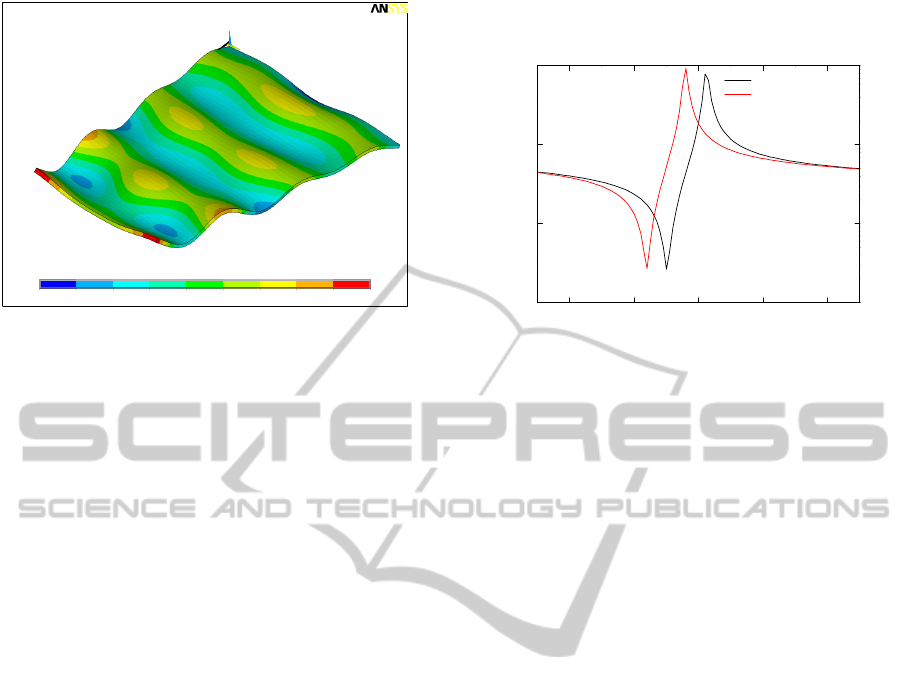
Figure 1: Foil displacement field (arbitrary units) at its
first ultrasonic bending mode (25044 Hz).
3 THE DESIGN OF THE
LANGEVIN TRANSDUCER
The Langevin transducer is basically composed of
two, or more, piezoceramic disks electrically
connected in parallel, sandwiched between two
metal masses (Langevin, 1924). It can be excited to
resonate in length–extensional mode at low
frequency, avoiding the need of high driving
voltages. The structure is usually pre stressed in
order to increase the mechanical strength of
piezoceramic elements and is suitable to absorb high
electrical power. In our case the transducer is
composed by 4 piezoceramic rings (Pz 26, by
Ferroperm Piezoceramics A/S, Kvistgaard,
Denmark) with a thickness of 1 mm, an outer
diameter of 20 mm and an inner diameter of 3.8 mm;
imposing a resonance of 25 kHz, by classical 1–D
analytical models (Zelenka, 1986) we computed that
the thickness of both the front and back steel masses
is 44.6 mm.
The 4 piezoceramic rings are electrically connect
in parallel by means of 4 copper rings (0.35 mm
thick and with the same diameters of piezoceramic
disks) placed between them. In order to verify if the
presence of the copper rings can be neglected in the
actuator design, we computed by ANSYS the
electrical input impedance Z
i
of the Langevin with
and without these rings; in Fig. 2 is shown the Z
i
amplitude computed in the two cases in a frequency
range around the foil resonance. As it can be seen,
the presence of the copper rings is not negligible: the
resonance and antiresonace frequencies both shift of
about 600 Hz (the 2.4 % of the resonance
frequency); in the next steps of the transducer design
the presence of copper contact rings must be
accounted.
Figure 2: Electrical input impedance of the Langevin
transducer computed by ANSYS taking (in red), or not (in
black) the copper contact rings into account.
In order to amplify the displacement on the
actuator front face various solutions can be used;
among these, sectional ultrasonic concentrators,
made from rods of variable and constant cross
section, are those that have been mainly exploited in
applications. Basically, sectional concentrators are
designed to resonate in length–extensional mode at
the same frequency of the Langevin transducer and
the displacement amplification depends on the ratio
between the back and the front sections. Sectional
concentrators have been widely analyzed by
Merkulov (Merkulov, 1957) and Kharitonov
(Merkulov, Kharitonov, 1959) for several shapes
(conical, exponential and catenoidal). These authors
concluded that the maximum displacement
amplification is achieved for a stepped horn, when
the two sections are both one-quarter wavelength
(λ/4) long; in this case, the amplification factor is
equal to the ratio between the areas of the two end
sections. By using this design criterion, the actuator
total length is therefore λ: λ/2 of the Langevin
transducer plus λ/2 of the stepped horn displacement
amplifier. For the design of the displacement
amplifier we just decided to use a stepped horn
device (the whole actuator is shown in Fig. 3); the
sections of the amplifier are both 48.6 mm long, the
thinner section has a diameter of 10 mm while the
other has the same diameter of the other Langevin
components.
The main problem of this kind of actuator is its
total encumbrance: in the present case the whole
length is 194.4 mm. In order to reduce the
encumbrance we designed a device whose total
length is λ/2 at the operating frequency (≈
25 kHz):
it is composed by the same 4 Pz 26 piezoceramic
1
MN
MX
X Y
Z
-43.219
-32.941
-22.662
-12.384
-2.105
8.173
18.452
28.73
39.009
49.287
JUL 2 2010
13:07:54
NODAL SOLUTION
STEP=1
SUB =30
FREQ=25044
UZ (AVG)
RSYS=0
DMX =49.496
SMN =-43.219
SMX =49.287
22 24 26 28 30
10
100
1000
10000
without copper rings
with copper rings
|Z
i
| [Ω]
f [kHz]
BIODEVICES 2011 - International Conference on Biomedical Electronics and Devices
164