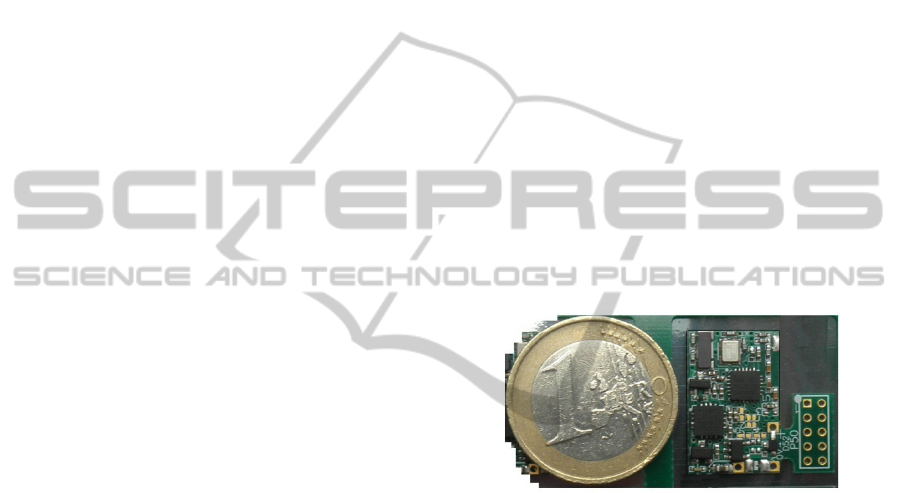
EEPROM resources and the integration of a 2.4Ghz
RF transceiver.
The nRF24LE1 is combined with an Analog
Devices ADXL325 three axis accelerometer for the
purpose of measuring accelerations of the user’s
lower leg; the sensor being placed just above the
ankle.
The microcontroller samples the three axes at a
rate of 50 or 100Hz and performs activity
recognition processing on this data. Following each
sample and activity identification the sensor logs the
result in the EEPROM, time stamps it and continues
to the next activity recognition.
Due to the fact that the RF end of the
microcontroller consumes a large proportion of the
power, the RF stage is seldom switched on during
normal operation. However every 5 seconds, the RF
stage is switched on for 20 milliseconds and the
device listens for a command packet from the users
Home PC. In the event one is received the sensor
begins an authentication handshake and subsequent
interchange of relevant data.
As the device is to be worn continuously three
very important design constraints have been
demanded:
• The battery life must be as long as possible
• The device must be small and hermetically
sealed to survive swimming and bathing
• The device must therefore be non contact
charged
The device is powered by a 20mAh lithium
polymer battery with the intention being to last
ideally 72 hours between charge times. Besides
reducing any unnecessary usage of the RF stage, as
previously mentioned, the design includes several
energy saving methods.
For example the ADXL325 device has been
chosen for its wider G range and very low cost
however it is slightly more power hungry than other
devices available and is the main power-sink after
the microcontroller. To reduce power applied in
sensing the accelerometer and the microcontroller
ADC are only switched on before and switched off
immediately after the 3 axes are sampled. Allowing
for switch on times delay, this saves about 50% of
the power compared to leaving them on at all times
i.e. saving roughly 0.15mA on average.
Similarly, it is planned that the activity
recognition task should itself be managed depending
on time and observed activity. That is, by using the
local timer and sleep function, the sensor will set to
conduct activity recognition between around 10%
and up to 70% of the time, depending on the
observed activity seen by the accelerometer.
This is achieved by implementing a small
dedicated code to check the accelerometer outputs
and to decide if there is some activity or not. If there
is no activity, then the device goes to sleep for 100
milliseconds before repeating the activity check. As
soon as activity is detected the main recognition task
is engaged and repeated up to a maximum of 70% of
the time, the rest of the time the sensor is set to sleep
mode.
In this way if the user is continuously active,
such as engaged in a long walk, the energy
maximum usage is 70% of worst case. Meanwhile if
the user is sleeping, then the sensor is largely
inactive apart from if the user moves from time to
time.
3.1 Ergonomics Constraints
The small size of the sensor, Figure 2.0, has been
achieved using an electronic PCB design equal in
size to the dimensions of the LiPo battery used. The
assembled device has a very low profile with no on-
off switch or flash connectors.
Figure 2: The ACT sensor, 20mm x 12 mm x 3mm, the
flash connector on the right is snapped off pre
encapsulation.
The hermetic sealing requirement implies that
the sensor must have a contactless charging method
and that the sensor is totally encapsulated.
To achieve this, the ACT sensor incorporates a
LiPo battery charging circuit as well as the
rectification stage for an inductive voltage power
input. The microcontroller, powered by the battery,
is able to sense when the rectified inductive input
voltage rises above the input threshold required by
the charging circuit. When this occurs the
microcontroller goes into a deep sleep effectively
switching itself off and appearing as a tiny load
shunt across the battery. This allows the charging
circuit to charge the LiPo battery without any
interference, until the battery voltage has reached the
fully charged level.
Meanwhile the inductive loop coil which is
driven at 10KHz by a standard off the shelf
MENTAL HEALTH DECLINE PREDICTION - A Smart Sensor for Day to Day Activity Recognition
221