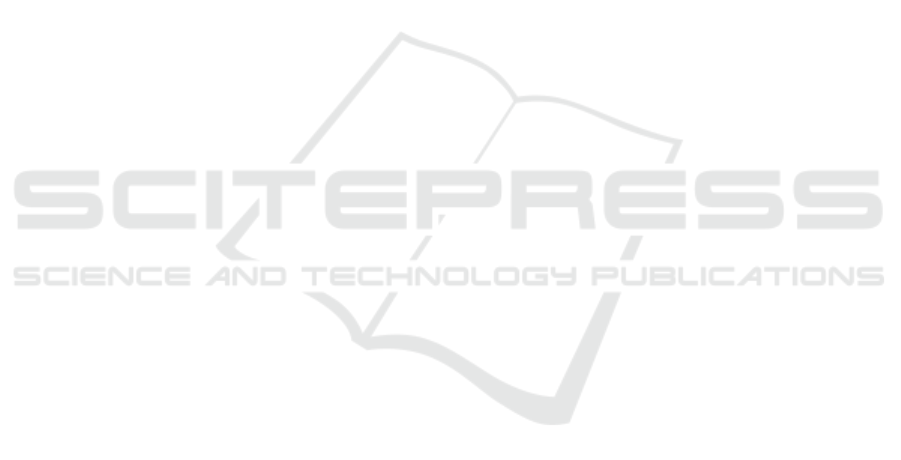
HUMAN KNEE PROSTHESIS EQUIPPED WITH FORCE
SENSORS
M. Gazzoli, E. Sardini, M. Serpelloni
Department of Information Engineering, University of Brescia, Brescia, Italy
G. Donzella
Department of Mechanical Engineering, University of Brescia, Brescia, Italy
Keywords: Measurement in human knee, Instrumented implant, Biomechanics, Force transducer, Strain sensor.
Abstract: In-vivo monitoring of human knee implants after total arthroplasty increases the knowledge about articular
motion and loading conditions. The proposed knee prosthesis equipped with force sensors executes force
measurements in polyethylene human knee prosthesis by two sensorized metal bars positioned under the
femoral condyles and fully contained in the polyethylene insert. In this paper, a new force sensor, which
acts in the knee integrated in the prosthesis, is proposed with the aim of reducing the hysteresis of
polyethylene material and increase the rigidity of the insert. The fabricated sensors are characterized and
tested by means of a mechanical press controlled load. The realized conditioning electronics is done by low
power components and it can be integrated in an autonomous system. The forces transmitted across the knee
joint during normal human activities such as walking, running or climbing can be directly measured.
Furthermore, the device can be used to improve design, refine surgical instrumentation, guide post-operative
physical therapy and detect human activities that can overload the system.
1 INTRODUCTION
The measurement of forces acting on knees, while
walking or during normal movements of the leg is a
topic widely discussed in (Gattiker, Umbrecht,
Neuenschwander, Sennhauser, Hierold, 2008),
(Westerhoff, Graichen, Bender, Rohlmann,
Bergmann, 2009), (Heinlein, Graichen, Bender,
Rohlmann, Bergmann, 2007). In Heinlein et al.
(2007), a measurement system detects the forces
using strain gauge sensors: the authors propose the
measurement of six degrees of freedom of the knee
(three forces and three moments) using a titanium
frame inserted in the tibia with six strain gauges. In
(Crescini, Sardini, Serpelloni, 2009), an
instrumented knee prosthesis is proposed for
measure the forces between the femur and tibia by
magnetoresistors. These sensors measure the
deformation of the polyethylene surface of the
prosthesis in contact with the condyles of the tibia.
But, in this configuration and particular design, the
material shows hysteresis after application of forces,
because the polyethylene material has a viscous-
elastic component. The proposed system relies on
the use of a new sensors technology. A typical
prosthesis for human knee is composed by three
principal inserts. In Figure 1, the 3D model of the
adopted prosthesis is represented. The femoral and
tibial insert are made on titanium and the tibial plate
is made of polyethylene. On the top of the implant
two excavations are carried out (Figure 1) centered
under the contact point between the condyles and the
polyethylene insert. These holes are made for
accommodate two sensorized metal bars. Two strain
gauges are placed under the metal bars for
measuring the deformations and correlate the
measured data to the force applied. In this way, the
sensors are closer to the focal point of the condyles
with the prosthesis, and this placing allows
integrating electronics and sensors in the
polyethylene insert. The realized sensors and
conditioning electronics is done by low power
components and it can be integrated in an
autonomous system as proposed in (Crescini et al.,
2009).
349
Gazzoli M., Sardini E., Serpelloni M. and Donzella G..
HUMAN KNEE PROSTHESIS EQUIPPED WITH FORCE SENSORS.
DOI: 10.5220/0003154603490352
In Proceedings of the International Conference on Biomedical Electronics and Devices (BIODEVICES-2011), pages 349-352
ISBN: 978-989-8425-37-9
Copyright
c
2011 SCITEPRESS (Science and Technology Publications, Lda.)