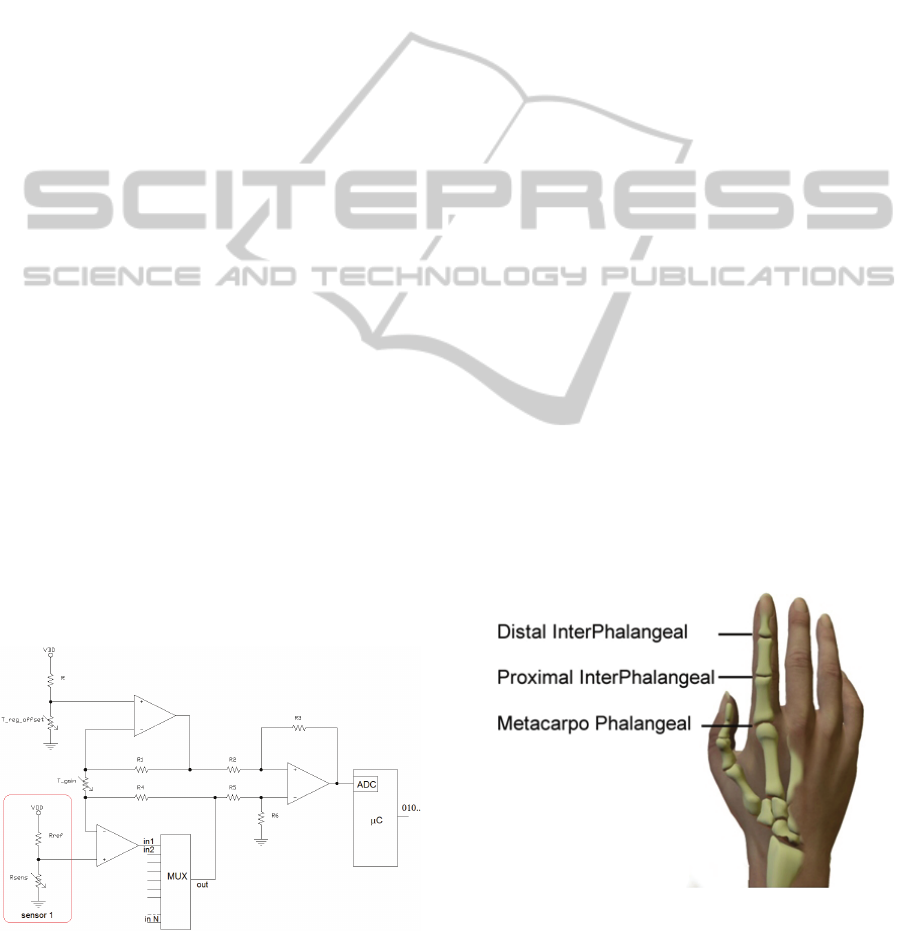
3 SIGNAL CONDITIONING
In this paragraph we analyze the optimized
electronic interface for our HITEG-Glove, according
to the afore-mentioned conditions listed in the
introduction. A novel approach for analog signal
conditioning before A/D conversion, which matches
the requirements is presented. System configuration,
accuracy and resolution have been analyzed in-depth
and designing rules have been defined. Experimental
results show that this electronic interface exhibits
less than 1% error in a large measurement range for
strain sensor rotation angle. It also shows a good
stability to power supply interference. The interface
has been successfully applied to a glove-based
measurement system of hand gesture.
Resistive bend sensors are integrated in clothing
to acquire wearer’s posture and movements in the
form of voltage signals. They are interestingly light,
soft and environmentally stable.
Piezoresistive sensors have been extensively
investigated with some promising ones being
explored for real applications (Saggio G. et al., 2009
- Orengo G. et al, 2009). They have a large
measurement range for outward bendings from 0° to
120°, and correspondingly the resistance normally
changes from 10 to 170 kΩ. The hysteresis they
manifest is really negligible and repeatability is
exceptional. Thanks to their high sensibility these
sensors can be adopted as a key-element for
measuring ROM of people with reduced hand
capabilities. A second key-element is our proposed
electronic interface and signal conditioning circuitry.
The optimized electronic interface for wearable
sensors here concerned is based on a differential
instrumentation amplifier. Fig. 5 shows the proposed
electronic interface.
Figure 5: Signal conditioning electronic interface
proposed.
It consists of a group of voltage dividers for
resistive sensors (one for each sensor) to extract a
voltage signal from sensor resistance variation using
a first stage input buffer. Subsequently a second
stage provides to properly shift/amplify the sensor
signals with the possibility of finely adjusting both
gain and offset level to make the levels of output
voltage dividers fit the input range of a PIC
microcontroller 12 bits A/D converter. In this way
we can measure very little signal variation
corresponding to very little joint bendings on
disabled subject. Then the microcontroller can send
the digital signals in a serial format to a general
purpose PC for post elaboration, reconverting them
to the corresponding bending angles of the joints.
Voltage dividers are used because of their simple
structures and potential high dynamic measurement
ranges they can furnish. In order to minimize the
size of the electronic interface, a single conditioning
circuit of the signal, which can be used by every
sensor implementing a polling routine on a
multiplexer, has been reasonably designed. It is
important to notice that the voltage signal variation
range can change from sensor to sensor; this is
because the technological process of factory doesn’t
produce identical devices (as it results clear by
observing the standard deviation reported on the 7
calibration points of the characteristic curve reported
in Fig. 3). Another reason is that the maximum
bending angle of each sensor depends on the joint it
is applied to; for example the sensors of the
proximal interphalangeal joints, which perform the
maximum bending angle possible (typically 120° but
in a wholly able subject), react with the largest
resistance variation.
Figure 6: Human finger joints.
For such reasons it is necessary to choose in the
design of the instrumented differential amplifier a
voltage gain (and a level shift) so to realize the best
HEALTHINF 2011 - International Conference on Health Informatics
250