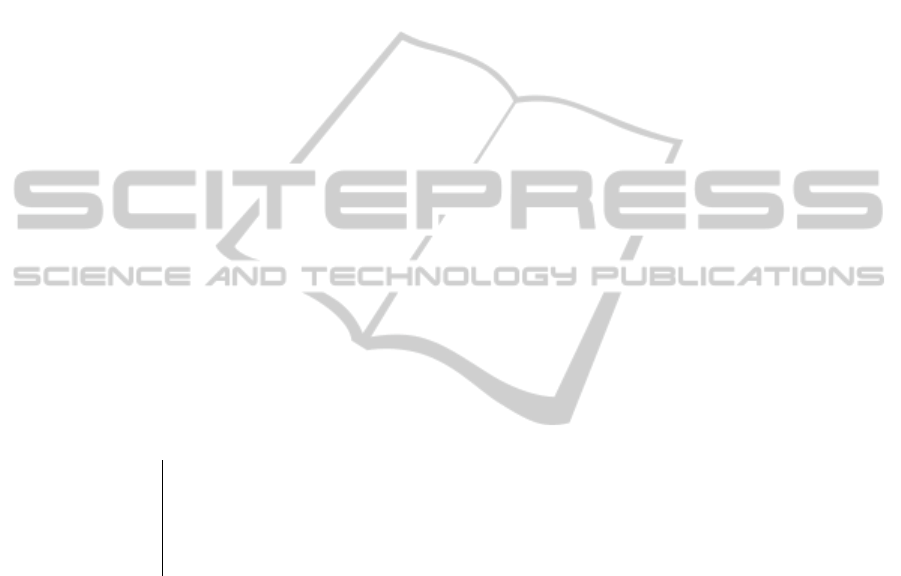
independence of each channel that was assumed
during the derivation of equations 1 and 2 does not
necessarily hold true. The average NRMSE for our
experimental data is approximately 7.7% for the 3-
dimensional surfaces, and 4.7% for the 2-
dimensional plot.
6 DISCUSSION AND FUTURE
WORK
The spatial MFJ’s wide range of motion that was
proposed in the design concept is indeed supported
by experimental analysis. The projection of the
MFJ’s movement spans all 4 quadrants of the x-y
plane. Furthermore, relatively large displacements
(greater than 40 degrees as seen in Figure 4) can be
achieved by applying no more than 20psi of fluidic
pressure.
This wide range of motion, along with its
lightweight, non-metallic parts and non-electric or
magnetic stimulation make the spatial MFJ a
desirable device to insert into the human body.
Therefore, it may be useful for biomedical
applications based on its performance and
composition. Some characteristics of the MFJ are
summarized in Table 2.
Table 2: Summary of MFJ Characteristics.
Dimension
40 × 6 × 7
Mass 2.26g
Max rotation
>40 deg
Max pressure
required
21.5 psi
The pressure in the channels can be controlled
with syringes and syringe pumps, which help to
control the pressure input. Using equations 1 and 2,
the user can know approximately what pressures
must be input into each channel in order to achieve a
desired position. This system may be useful in
intubation processes such as laryngoscopy,
endoscopy, or colonoscopy, in which a destination
can be viewed with a camera, and appropriate
pressures can be input into the system so that the
MFJ can reach the desired destination.
7 CONCLUSIONS
In this paper, we presented the design of the MFJ,
which potentially provides solutions to the
shortcomings of previous fluidic and pneumatic
actuators. The MFJ displays large multi-dimensional
movements (rotations greater than 40 deg), is
lightweight (about 2g), compact in size (about 1.7
cm
3
), and has a predictable pressure-displacement
behavior. We have developed a simplified
mathematical model, which approximates the
relationship between the pressure in the three MFJ
channels and the MFJ displacements; error between
model prediction and experimental data is about
7.7%. Such an error could potentially be
dramatically reduced if the effect of each channel to
the other channels could be taken into account. It
should be noted that by scaling the fabrication mold
up or down, the dimension of the MFJ could be
easily altered for different applications. The device
presented in this paper is made of a polymer-based
material and implements a unique channel design.
The manufacturing process is very simple, contains
few components, and allows for mass production.
These properties make the spatial MFJ potentially
useful in bio-mechatronic applications.
ACKNOWLEDGEMENTS
This work was supported by the Natural Sciences
and Engineering Research Council of Canada
(NSERC). The authors would like to thank Verathon
Medical Canada.
REFERENCES
Lim, G., Park, K., Sugihara, M., Minaret, K., Esashi, M.,
1996. Future of active catheters. Sensors and
Actuators A, vol. 56, no. 1–2, pp. 113–121.
Kawai, F., Cusin, P., Konishi, K., 2001. Thin flexible end-
effecter using pneumatic balloon actuator. Sensors and
Actuators A 89, pp. 28–35.
Muyari, Y., Haga, Y., Mineta, T., Esashi, M., 2003.
Development of hydraulic suction type active catheter
using super elastic alloy tube. In: Proc. 20th Sensor
Symposium. Japan, 2003.
Suzumori, K., Iikura, S., Tanaka, H., 1991. Development
of flexible microactuator and its applications to robotic
mechanisms. In: Proc. 1991 IEEE International
Conference on Robotics and Automation. Sacramento,
California, April 1991.
Haga, Y., Esashi, M., 1998. Small diameter active catheter
using shape memory alloy coils. In: Proc. 11
th
IEEE
International Workshop on Micro Electro Mechanical
Systems (MEMS’98). Germany, 1998.
A NOVEL SPATIAL MICROCHANNEL FLUIDIC JOINT
243