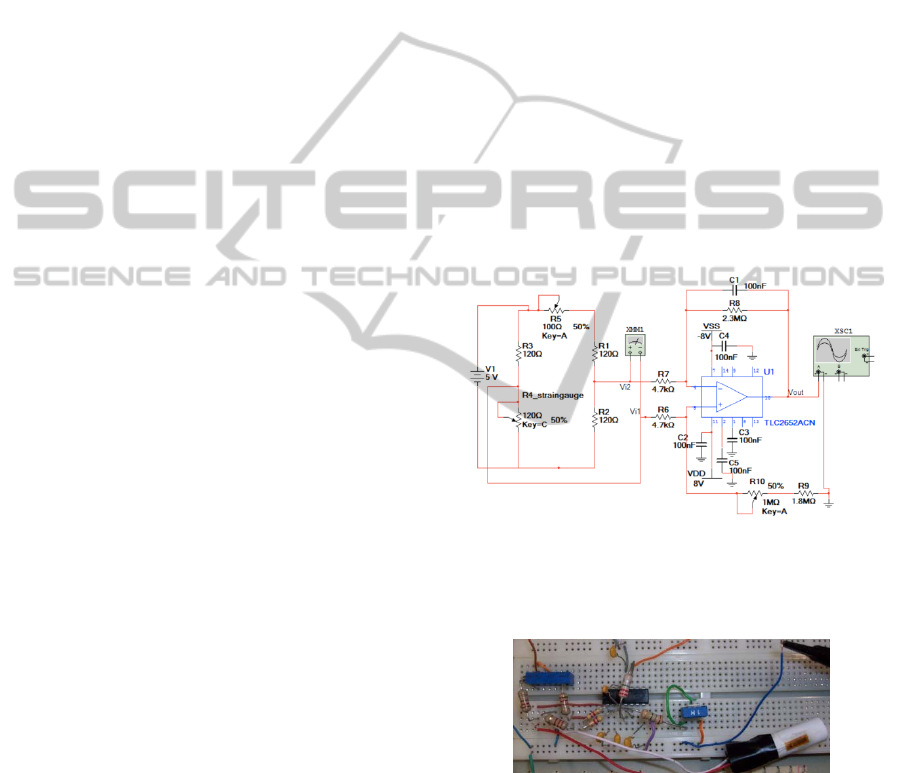
However they are not yet able to record images from
the gastrointestinal tract (Camilleri, 2008). With the
very promising developments on the capsule
locomotion and stopping mechanisms, the addition
of manometry functions as a complement to existent
EC imaging functions will be of great clinical utility.
Using microtechnologies it is possible to build
small transducers on the capsule surface. These
technologies enable implementation of many
transducers that can record pressure values all
around the capsule area. As a first step, the
deposition process of strain gauge transducers is
studied and described. Also, an electronic circuit for
the readout of the transducer output signal is
designed and implemented. The proper functioning
of the circuit will be first tested using a commercial
strain gauge transducer. The results of the system
performance and amplification circuit are described.
2 EXPERIMENTAL
2.1 Fabrication of Transducer Element
The transducer element can be fabricated with thin-
film deposition and patterning processes. However,
some constrains were already studied and must be
considered during the fabrication process: the
polymer of current available EC cannot support
temperatures above 120 ºC and is incompatible with
chemicals (solvents) used in some photo-
lithographic processes; and the curved surface of EC
limits the use of rigid lithographic masks.
The fabrication of the sensing element starts with
a polyimide film (5 mm in length and width, and a
thickness of 25 µm). Next, a chromium layer is
deposited in the polyimide film by e-beam. A
photoresist mask is created by lithography processes
to be used in the wet-etching of the chromium film.
The polyimide film is then etched, using the
chromium pattern film as mask. This patterned
polyimide film is after used as shadow mask in the
deposition of metal in the EC. A shadow mask
process allows the fabrication of the transducer
element, despite the constraints previously
considered. The mask is glued to the EC surface
before the deposition of a thin metal layer. Since
there is only a single mask, there are no concerns
regarding its alignment. The metal deposition occurs
through the etched region of the polyimide mask,
creating regions were metal will be deposited, and
regions without metal, forming the transducer
element in the EC. After the deposition, the mask is
removed, exposing the transducer that should be
encapsulated with a biocompatible polymer. Due to
the mentioned fabrication constraints, the deposition
process is being optimized for the capsule surface
polymer, and is currently in progress.
2.2 Circuit Design
For the circuit design and test, one commercial
solid-state strain gauge transducer was connected in
a quarter Wheatstone bridge configuration (Figures
1 and 2). The transducer length and width is equal to
5 and 1.8 mm, respectively, and it has a resistance of
120 ± 5%. Since our surface is not planar we will
not use two gauges because it cannot be assured the
same proportion of compressive and tensile stress in
both transducers. Also, an in vivo study of Cowles et
al. (1978) found that mechanical events recordings
obtained from a one quarter Wheatstone bridge
transducer were of the same quality as those
produced by a one half bridge configuration, in
terms of accuracy, sensitivity and stability.
Figure 1: Layout of the system circuit with a differential
amplifier, TLC2652CN, to increase the amplitude of the
bridge output signal. The TLC2652CN features low offset
voltage 1PV with -0.003 V/°C, and a CMRR of 120 dB.
Figure 2: Implementation of the circuit on a breadboard.
The strain gauge was glued to a cylindrical tube
using cyanoacrylate glue. The gauge lead out wires
were then soldered to electrical wires and mounted
on a breadboard, in a bridge circuit, together with
three resistors - R1, R2 and R3 - of the same value
(120 ). The multi-turn potentiometer (R5) is used
to compensate the resistance tolerance of the bridge
BIODEVICES 2011 - International Conference on Biomedical Electronics and Devices
398