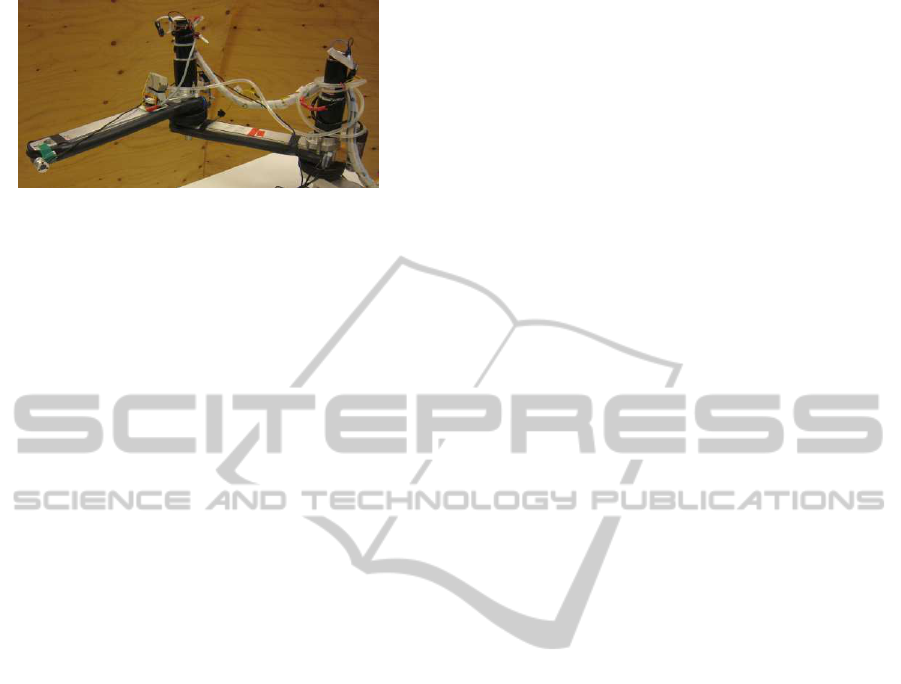
Figure 1: Two link planar robot prototype.
rect control over these muscles to generate almost any
desired motions. Human arm exhibits the required
three principle modes of motions (stiff, compliant and
soft) by controlling the tension between their antago-
nistic set of muscles. Thus, a pair of continuously
controlled antagonistic muscles ensures the required
level of adaptable compliance and position accuracy.
2.1 Modes of motion for safe HRI
In HRI tasks, purely motion control strategy for con-
trolling the robot interaction forces is not enough,
mainly due to imprecise modeling of the robot ma-
nipulator and the highly unpredictable nature of the
HRI itself. For safe HRI, robot has to execute simul-
taneously multiple-axes motions based on feedback
signals. This usually involves a combination of sev-
eral motions varying from fully stiff to fully compli-
ant. The contact situations may vary depending upon
the specific requirement of interaction task, but in all
cases the robot has to execute three different modes
of motion namely:
Stiff motion, refers to robot motion in unconstrained
free work space. The reaching of desired position is
achieved by a standard position and velocity control.
It manifests zero compliance, therefore only this mo-
tion mode is not sufficient for performing HRI tasks.
Soft motion, refers to robot motion in a dynami-
cally constrained work space. The dilemma of avoid-
able/unavoidable collision with a sudden, unexpected
intrusion of an obstacle for example, human body or
part of it, implies the necessity of switching from fully
stiff to zero-stiff joint in order to cut the transmission
of a torque to the adjacent robot link.
Compliant motion, represents all transitions between
stiff and soft motion. In some situations the human
wants to superimpose its motion over the robot’s spec-
ified motion. For such conditions the robot has to ac-
complish compliant motion mode.
For our research two-link planar experimental
robot prototype was set-up (Figure 1). The desired
adaptable compliance or variable stiffness is intro-
duced by our dedicated MR fluid actuator, one for
driving each joint. Operational smoothness in the
performance of the MR fluid actuator mechanism is
shown in (R.Muhammad.Ahmed et al., 2008). Fully
activated MR fluid actuator (max clutch current) cor-
responds to stiff motion mode. Alternatively, fully de-
activated MR fluid actuator (zero clutch current) con-
forms to soft motion mode. All levels between fully
activated and deactivated actuator refers to the com-
pliant motion mode. These transitions can be tuned
depending upon the type, geometry and modalities of
the contact object accordingly.
2.2 Collision Safety Analysis
Previously, achieving high position robot accuracy
was considered as the main objective. Now, with the
emergence of new trends and applications in service
robotics, there is a strong belief that both position ac-
curacy and the collision safety are equally eminent
and indispensable for tasks involving HRI. A contact
phase is considered to be safe, only when the robot
exerted collision forces remain under the human pain
tolerance limits and never causes injury to the human.
This, consequently, formulates a criterion for the col-
lision safety analysis of the robot manipulator based
on static and dynamic collision.
Static collision, appears in situations where robot ma-
nipulator is directed to collide with the human, and
the collision is performed at very low speed, typically
less than 0.2 m/s. In order to evaluate the safety per-
formance several researchers have suggested a col-
lision force of 50N as a human pain tolerance limit
(Y.Yamada et al., 1996). Therefore, we have em-
ployed collision force threshold of 50N as a boundary
between the unsafe and safe regions of operation. We
did static collision tests and analyzed the static colli-
sion safety performance in both the stiff and compli-
ant modes of motion.
Dynamic collision, replicates the condition where
robot is forced to collide with the human at higher
speeds. Since the topic of human robot colli-
sion safety in dynamic collision is relatively new in
robotics, no specific standard has been established
yet. However, in order to evaluate the safety per-
formance at dynamic collision, head injury crite-
rion (HIC) and abbreviated injury scale (AIS) are
currently employed (A.Bicchi and G.Tonietti, 2004),
(J.Versace, 1971). Head injury criterion (HIC) defines
the index for injury severity (damages) and used by
automobile industry for car crash. HIC value greater
than 1000 refers to a very severe head injury. For
the normal operation of machines, a HIC value of
100 is suggested. Therefore, for the safety perfor-
TWO LINK COMPLIANT ROBOT MANIPULATOR FOR HUMAN ROBOT COLLISION SAFETY
519