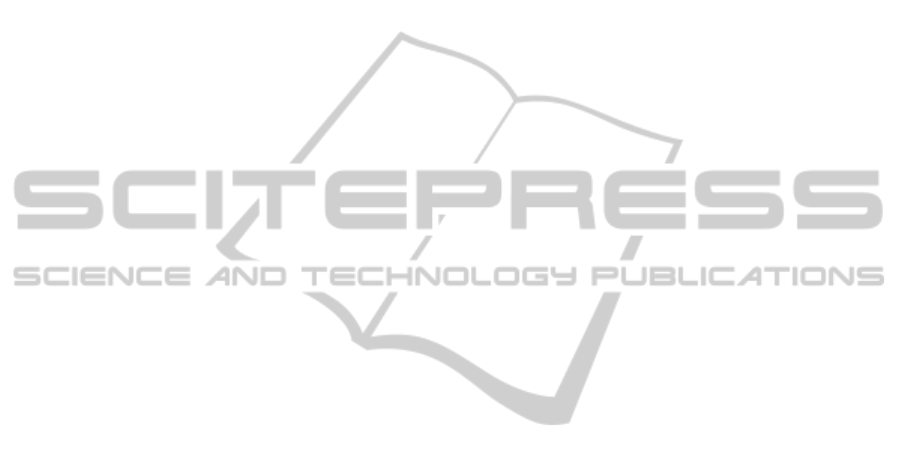
high-permittivity material on the chip is also
explained and the best results of this endeavour are
shown.
The measurement system to operate the chip was
also explained in detail.
The functionality of the chip was proven
electrically. Biological experiments will follow
shortly to verify its capability to measure from
cardiomyocyte cultures grown in vitro.
REFERENCES
Thomas, C., Springer, P., Loeb, G., Okun, L., 1972, A
miniature microelectrode array to monitor the
bioelectric activity of cultured cells, Exp. Cell Res.,
74, pp. 61-66
Pine, J., 1980, Recording action-potentials from cultured
neurons with extra-cellular micro- circuit electrodes,
Journal of Neurosience Methods, 2, pp. 19-31
Gross, G., Williams A., 1982, Recording of spontaneous
activity with photoetched microelectrode surfaces
from mouse spinal neurons in culture, Journal of
Neuroscience Methods, vol. 5, pp. 13-22
Heer, F., Hafizovic, S., Franks, W., Blau, A., Ziegler C.,
Hierlemann A., 2006, IEEE Journal of Solid-State
Circuit, 41, 1620
Heer, F., Franks, W., Blau, A., Taschini S., Ziegler C.,
Hierlemann, A., Baltes H., 2004, Biosensors and
Bioelectronics, 20, 358
Eversmann, B., Jenkner, M., Hofmann, F., Paulus, C.,
Brederlow, R., Holzapfl, B., Fromherz, P., Merz, M.,
Brenner, M., Schreiter, M., Gabl, R., Plehnert, K.,
Steinhauser, M., Eckstein, G., Schmitt-Landsiedel, D.,
Thewes, R., 2003, IEEE Journal of Solid-State
Circuit, 38, 2306
Hofmann, F., Eversmann, B., Jenkner, M., Frey, A., Merz,
M., Birkenmaier, T., Fromherz, P., Schreiter, M.,
Gabl, R., Plehnert, K., Steinhauser, M., Eckstein, G.,
Thewes, R., 2003, ESSDERC 2003, Proc. 33rd
European Solid- State Device Research Conference,
167
Meyburg, S., Stockmann, R., Moers, J., Offenhaeusser, A.,
Ingebrandt, S., 2007, Sensors Actuators B
Meyburg, S., Goryll, M., Moers, J., Ingebrandt, S.,
Böcker-Meffert, S., Lüth, H., Offenhaeusser, A., 2006,
Biosensors and Bioelectronics, 21, 1037
Meyburg, S., Wrobel, G., Stockmann, R., Moers, J.,
Ingebrandt, S., Offenhaeusser, A., 2006, Applied
Physics Letters, 89, 013901
Imfeld, K., Neukom, S., Maccione, A., Bornat, Y.,
Martinoia, S., Farine, P-A., Koudelka-Hep, M.,
Berdondini, L., 2008, IEEE Transactions on
Biomedical Engineering, 55, 2064
Schindler, M., Kim, S.K., Hwang, C.S., Schindler, C.,
Offenhaeusser, A., Ingebrandt, S., 2007, Rapid
Research Letters, phys. stat. sol. 2, No. 1, 4-6, DOI
10.1002/pssr.200701242
HIGH-DENSITY CMOS ARRAY FOR BI-DIRECTIONAL COUPLING OF ELECTROGENIC CELLS
421