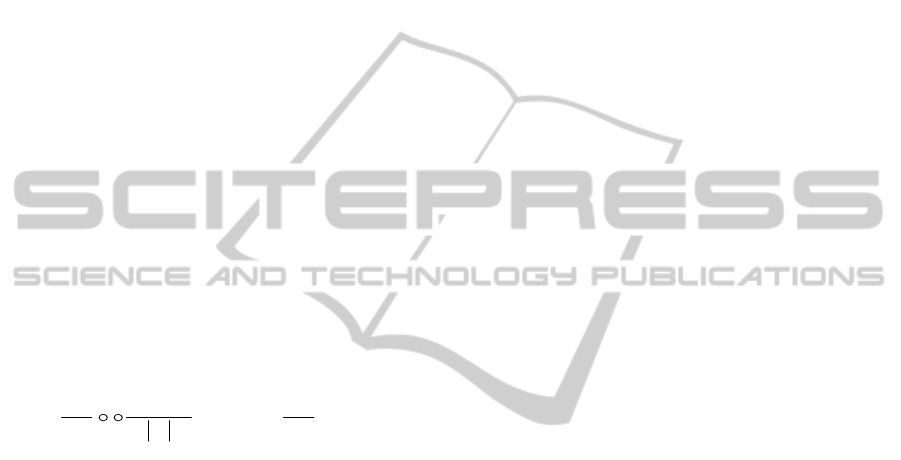
posture in a laboratory setting which are not of direct
interest in this study.
Comfort, accuracy and a user friendly interface
are key elements for such a device to work
successfully and be accepted in the medical world.
The basic element of the measuring system
introduced here is a very flexible, textile integrated
bending sensor. Several of these basis elements may
be combined in order to measure multi-dimensional
joints or more degrees of freedom of the human
body.
In the next sections the basic element required to
measure bending is described.
2 BENDING SENSOR
2.1 Single Bending Sensor
Measuring bending in our setting is based on the
change of electrical inductance of a very simple coil
(a loop of a conductive wire). It appears that the
inductance of a coil changes as the form of the coil
changes. The mutual inductance by a filamentary
circuit i on a filamentary circuit j is given by the
double integral:
lY
sdds
L
a
CC
i
π
μ
π
μ
44
0
2/][
0
+
⎟
⎟
⎠
⎞
⎜
⎜
⎝
⎛
′
⋅
≈
≥
′
∫∫
R
R
(1)
where
0
denotes the magnetic constant (4πx10
-
7
H/m), C and C
′
are curves along the wires,
is
the distance between two points on respectively
C
and
C
′
. The vectors
ds
and
sd
′
represent
vectors along C and C
′
. When
becomes zero the
above equation becomes infinitive and therefore
there is an extra condition that
has to be larger
than half the thickness of the wire a. In that case the
inductance is only dependant on the radius a and its
length l and some factor Y denoting the current
distribution through the wire (typically Y=1/4).
When the form of the coil changes, the orientation of
ds
and
sd
′
changes and probably the distance
between them too. That results in a change of the
inductance of the coil.
As can be seen in equation (1) the mutual
position and orientation of the wire segments
determine the total inductance of the coil. It is these
elements that vary when the coil bends and thus
consequently changes the inductance
correspondingly. The wire used in this sensor is very
flexible and thin and integrated in a carrier e.g.. knee
brace, t-shirt, strap etc.
In the case that the bend of the coil is directly
connected to a single bending angle of a human joint
(knee, elbow etc.), a simple calibration can be used
to translate the bending inductance readings into an
absolute angle value. Calibration can be done using
a reference measuring system that simultaneously
measures the joint angle.
However in some cases, where the carrier may
be minimally shifted due to movement, the system
can be automatically recalibrated based on extra
information from accelerometers mounted on the
carrier.
2.2 Automatic Recalibration
In many applications where the bending sensors are
firmly attached to a body joint the translation from
inductance reading into joint angles can be done
once based on some discrete calibration
measurements. In particular in the case of a single
joint the calibration can be performed using
mechanical goniometry.
However, wearing a sensory system for a longer
time in a day inherently implies local shifting of the
system on the body, hence a discrepancy of the
calibration of the sensor. In addition, by fitting or
“putting on” the sensory system in a non-
reproducible way, the user introduces an additional
error in the calibration. To account for this an
automatic calibration was introduced based on extra
sensors mounted around the joint. A set of two tri-
axial accelerometers is placed above and below the
joint. When the user is in a steady state (sitting,
standing etc.) the readings of the accelerometers
may be used to calculate the absolute angle of the
joint. In static situations the accelerometers are only
measuring some proportion of the gravitational
force. Based on this, the angle between the
accelerometers is calculated. In dynamic situations
(walking, running etc.), the accelerometers “see”
simultaneously the gravitational force and the
human movement. In this case the calculation of the
joint angle is not possible using the accelerometers.
For this case the inductance measurement is used for
calculating the joint angle. Every static situation
during the day is used to (re)calibrate the bending
sensor compensating for any changes of the bending
sensor attachment on the human joint.
In summary, during static situations the
accelerometers are used to calculate the absolute
joint angle and calibrating the bending sensor, and in
dynamic situations only the calibrated bending
sensor is used.
WEARABLE HUMAN BODY JOINT AND POSTURE MEASURING SYSTEM
269