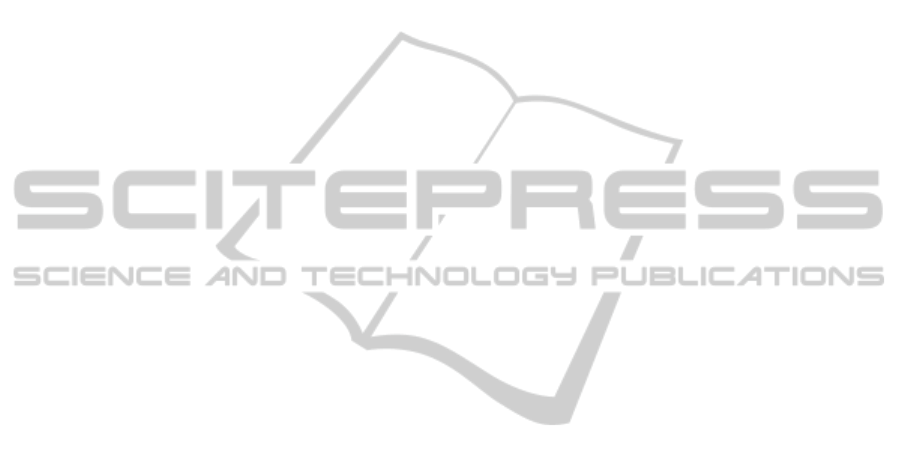
Bloor, M. I. G., Wilson, M. J., 1989a. Generating n-sided
patches with partial differential equations. New
Advances in Computer Graphics, Proceedings of CG
International’89, Springer-Verlag, Tokyo, Japan, 129-
145.
Bloor, M. I. G., Wilson, M. J., 1989b. Generating blend
surfaces using partial differential equations.
Computer-Aided Design 21(3),165-171.
Bloor, M. I. G., Wilson, M. J., 1990a. Using partial
differential equations to generate free-form surfaces.
Computer-Aided Design 22(4), 202-212.
Bloor, M. I. G., Wilson, M. J., 1990b. Representing PDE
surfaces in terms of B-splines. Computer-Aided
Design 22(6), 324-331.
Bloor, M. I. G., Wilson, M. J., 1996. Spectral
approximations to PDE surfaces, Computer-Aided
design 28(2),145-152.
Celniker, G., Gossard, D., 1991. Deformable curve and
surface finite-elements for free-form shape design.
Computer Graphics 25(4), 257-266.
Du, H., Qin, H., 2005. Dynamic PDE-based surface design
using geometric and physical constraints. Graphical
Models 67, 43–71.
Farin, G., 1997. Curves and Surfaces for Computer Aided
Geometric Design: A Practical Guide. 4th Edition,
Academic Press.
Guillet, S., Léon, J. C., 1998. Parametrically deformed
free-form surfaces as part of a variational model.
Computer-Aided Design 30(8), 621-630.
Hyodo, Y., 1990. The generation of free form surface
defined with contour and sectional curves. Journal of
the Japan Society of Precision Engineering 56(10),
1912-1916.
Li, Z. C., 1998. Boundary penalty finite element methods
for blending surfaces, I. Basic theory. Journal of
Computational Mathematics 16, 457-480.
Li, Z. C., 1999. Boundary penalty finite element methods
for blending surfaces, II. Biharmonic equations.
Journal of Computational and Applied Mathematics
110, 155-176.
Li, Z. C., Chang, C.-S., 1999. Boundary penalty finite
element methods for blending surfaces, III.
Superconvergence and stability and examples. Journal
of Computational and Applied Mathematics 110, 241-
270.
Miura, K. T., 2000. Unit quaternion integral curve: a new
type of fair free-form curves. Computer Aided
Geometric Design 17(1), 39-58.
Nealen, A., Müller, M., Keiser, R., Boxerman, E., Carlson,
M., 2006. Physically based deformable models in
computer graphics. Computer Graphics Forum 25(4),
809-836.
Ochiai, Y., Yasutomi, Z., 2000. Improved method
generating a free-form surface using integral
equations. Computer Aided Geometric Design 17(3),
233-245.
Qin, H., Terzopoulos, D., 1995. Dynamic NURBS swung
surfaces for physics-based shape design. Computer-
aided Design 27(2), 111-127.
Terzopoulos, D., Platt, J., Barr, A., Fleischer, K., 1987.
Elastically deformable models. Computer Graphics
21(4), 205-214.
Terzopoulos, D., Fleischer, K., 1988. Modeling inelastic
deformation: viscoelasticity, plasticity, fracture.
Computer Graphics 22(4), 269-278.
Terzopoulos, D., Qin, H., 1994. Dynamic NURBS with
geometric constraints for interactive sculpting. ACM
Transactions on Graphics 13(2), 103-136.
Ugail, H., Bloor, M. I. G., Wilson, M. J., 1999a.
Techniques for interactive design using the PDE
method. ACM Transactions on Graphics 18(2), 195-
212.
Ugail, H., Bloor, M. I. G., Wilson, M. J., 1999b.
Manipulation of PDE surfaces using an interactively
defined parameterisation. Computers & Graphics
23(4), 525-534.
Vassilev, T. I., 1997. Interactive sculpting with
deformable nonuniform B-splines. Computer Graphics
Forum 16, 191-199.
Vida, J., Martin, R. R., Varady, T., 1994. A survey of
blending methods that use parametric surfaces.
Computer-Aided Design 26(5), 341-365.
You, L. H., Zhang, J. J., Comninos, P., 1999. Cloth
deformation modelling using a plate bending model.
In Proceedings of the 7
th
International Conference in
Central Europo on Computer Graphics, Visualization
and Interactive Digital Media’99, 485-491.
You, L. H., Zhang, J. J., Comninos, P., 2000. A volumetric
deformable muscle model for computer animation
using weighted residual method. Computer Methods in
Applied Mechanics and Engineering 190(8-10), 853-
863.
You, L. H., Zhang, J. J., 2003. Fast generation of 3-D
deformable moving surfaces. IEEE Transactions on
Systems, Man and Cybernetics-Part B: Cybernetics
33(4), 616-625.
You, L. H., Zhang, J. J., 2004. PDE blending surfaces with
2
C continuity. Computers & Graphics 28, 895-906.
Zhang, J. J., You, L. H., Comninos, P., 1999. Computer
simulation of flexible fabrics. In Proceedings of the
17
th
Annual Conference, UK Chapter,
EUROGRAPHICS, 27-35.
GRAPP 2011 - International Conference on Computer Graphics Theory and Applications
30