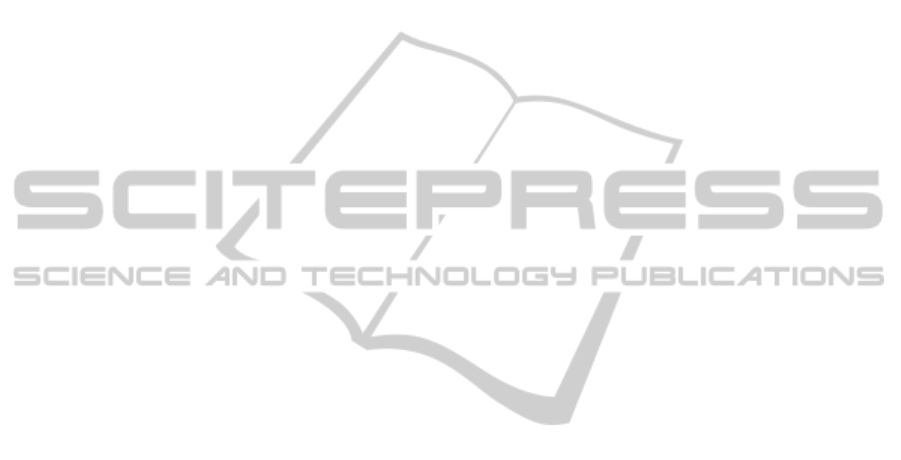
uses this information to geometrically segment
complex holes into simple approximately planar
holes, called sub-holes. The patch meshes that are
used to fill those sub-holes are generated by using
planar triangulation algorithm for the point set at the
hole boundaries. Then these patch meshes are
mapped back to the 3D space and stitched to the
original model at the hole areas to achieve the final
result. The user is able to interact with our system
through correcting the crest lines, adjusting the
feature points defined by the crest lines and the hole
boundaries, pairing the feature points or specifying
the corner hole locations. The adjustment of the
location of the crest lines by users results in
modification in the shape of the patch mesh which is
later stitched to the original model, as holes are
filled using different geometric information. To
validate our approach, we have tested our technique
on different mesh models with many possible cases,
and the results show that our methods effectively
reconstruct the sharp features. Most approaches for
hole filling in literature do not reconstruct these fine
details due to the interpolation schemes used. We
overcome this limitation by including additional
information on the object shape in areas of high
curvature and by limited user intervention.
REFERENCES
Attene, M., Falcidieno, B., Rossignac, J., Spagnuolo, M.,
2003. Edge-Sharpener: Recovering Sharp Features in
Triangulations of Non-adaptively Re-meshed
Surfaces. In Proceedings of the First Eurographics
Symposium Geometry Processing (SGP’03), pages 63-
72.
Barequet, G., Kumar, S., 1997. Repairing CAD Models. In
Proceedings of the 8th conference on Visualization
'97, pages 363-371, Phoenix, Arizona, USA.
Barequet, G., Dickerson, M., Eppstein, D., 1998. On
triangulating three-dimensional polygons.
Computational Geometry: Theory and Applications,
10(3) pages 155-170.
Chen, C.-Y., Cheng, K.-Y., 2008. A sharpness-dependent
filter for recovering sharp features in repaired 3D
mesh models. IEEE Transactions on Visualization and
Computer Graphics, volume 14, No. 1,
January/February 2008.
Chen, C.-Y., Cheng, K.-Y., Liao, H. Y. M., 2005. A
Sharpness Dependent Approach to 3D Polygon Mesh
Hole Filling. Eurographics, Short Presentations, 2005.
Chew, P. L., 1989. Guaranteed-Quality Triangular
Meshes. Technical report 89-983, Department of
Computer Science, Cornell University, Ithaca, NY,
April 1989.
Chui, C. K., Lai, M.-J., 2000. Filling Polygonal Holes
Using C
1
Cubic Triangular Spline Patches. Computer
Aided Geometric Design, volume 17(2000), pages
297-307.
Dunlop, R., 2005. Introduction to Catmull-Rom Splines.
Technical articles, Microsoft DirectX MVP. URL:
http://www.mvps.org/directx/articles/catmull/
He, X. J., Chen, Y. H., 2006. A Haptics-guided Hole-
filling System Based on Triangular Mesh. Computer
Aided Design and Application, volume 3(6), pages
711-718.
Jun, Y., 2005. A Piecewise Hole Filling Algorithm in
Reverse Engineering. Computer-Aided Design 37,
pages 263-270.
Kobbelt, L. P., Botsch, M., Schwanecke, U., Seidel, H.-P.,
2001. Feature Sensitive Surface Extraction from
Volume Data. In Proc. of ACM SIGGRAPH 2001,
pages 57–66.
Liepa, P., 2003. Filling holes in Meshes. In Proceedings of
the Eurographics/ACM SIGGRAPH symposium on
Geometry Processing 2003, Eurographics Association,
pages 200-205.
Ohtake, Y., Belyaev, A., Alexa, M., Turk, G., Seidel, H.-
P., 2003. Multi-level Partition of Unity Implicits. ACM
Trans. Graphics, Proc. ACM SIGGRAPH 2003,
volume 22(3), pages 463-470.
Podolak, P., Rusinkiewicz, S.2005. Atomic Volumes for
Mesh Completion. In Proceedings of Eurographics
Symposium on Geometry Processing, Dublin, Ireland,
29 August-2 September 2005, pages 33-41, Blackwell
Press 2005.
Sharf, A., Alexa, M., Cohen-Or, D., 2004. Context-based
Surface Completion. ACM Transactions on Graphics,
SIGGRAPH 04, 23, 3.
Yoshizawa, S., Belyaev, A.G., Seidel, H.-P., 2005. Fast
and Robust Detection of Crest Lines on Meshes. ACM
Symposium on Solid and Physical Modeling, pages
227-232, Technical Sketch, June 13-15, 2005, MIT,
Cambridge, MA.
Yoshizawa, S., Belyaev, A., Yokota, H., Seidel, H.-P.,
2007. Fast and Faithful Geometric Algorithm for
Detecting Crest Lines on Meshes. Pacific Graphics,
pages 231-237, October 29-November 2, 2007, Maui,
Hawaii.
Zhao, W., Gao, S., Lin, H., 2007. A Robust Hole-Filling
Algorithm for Triangular Mesh. Visual Computer 23,
pages 987-997.
Zhao, M., Ma, L., Mao, Z., Li, Z., 2006. Feature Sensitive
Hole Filling with Crest Lines. Lecture notes in
Computer Science. In Proc. of Advances in Natural
Computation. The Second International Conference on
Natural Computation, Xi’an, China.
GRAPP 2011 - International Conference on Computer Graphics Theory and Applications
58