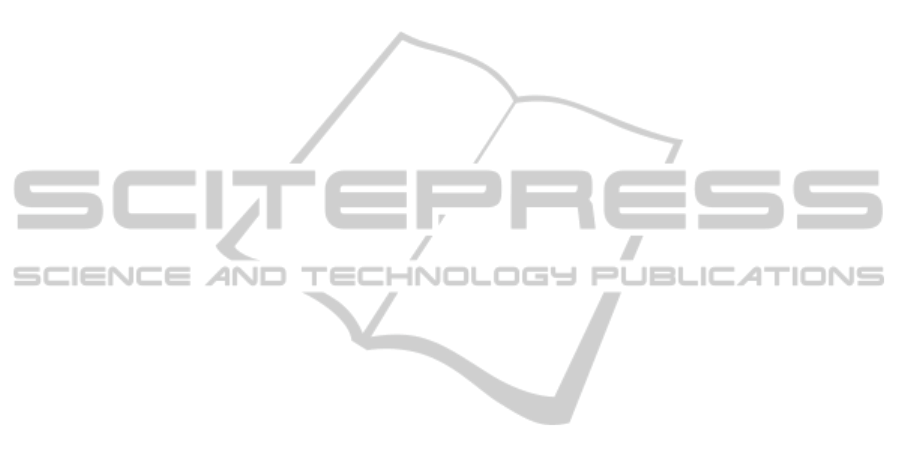
The paper is organized as follows. Identified re-
quirements steering the robot design are presented in
the next section. Detailed description of the robot
hardware is described in Section 3. The realization of
the arena with moving obstacles, robots’ docking sta-
tions and a global localization system are presented in
Section 4. A remote user access to the robots is real-
ized by the supporting computer that is directly acces-
sible through the Internet, its role and concept of the
user access to robots is briefly described in Section 5.
2 SYSTEM REQUIREMENTS
This section summarizes requirements affecting the
SyRoTek system design. At first, it is worth to men-
tion the system is designed as a multi-robotic, which
requires enough available robots for collective tasks.
Regarding to the expected scale of multi-robotic ex-
periments, we have decided to create a system with
10–15 robots.
The available space about 10 m
2
, restricts the
maximal robot diameter to 20 cm in order to pro-
vide sufficient work area. A differential drive with
two controlled wheels has been selected, offering suf-
ficient maneuverability in narrow space. The maxi-
mal robot velocity in range 0.2–0.5 m/s is considered
as sufficient.
The main goal of the SyRoTek system is to sup-
port education with real robots that will help students
to realize how robots sense the environment and how
to deal with uncertainties that are inevitable part of
real world. In order to provide such experiences, vari-
ety of sensors are requested to be mounted at the robot
body. The range-measuring sensors are the most typi-
cal sensors for basic robotic tasks. Also robot naviga-
tion based on image processing is becoming common
nowadays, so a color camera has been included in the
basic set of robot’s sensor equipment. Rotating laser
scanners (LIDARs) was selected as an optional equip-
ment for more advanced tasks.
The sensor equipment requires appropriate com-
putational resources that will allow simple sensory
data processing on-board. A PC-compatible com-
puter running operating system is highly desired for
such tasks, as it will allow a comfortable maintenance
and re-configuration.
Wireless communication device is needed on-
board for transmitting sensor data, control commands,
and software updates. IEEE 802.11 (WiFi) network
modules allow a wide bandwidth, but their disadvan-
tage is absence of the latency definition and eventual
drop-outs in noisy environments with many wireless
networks running alongside. This issue motivate us
to use another communication module to control the
robot, even at the cost of lower bandwidth.
The SyRoTek system is requested to run 24 hours
a day with a minimal maintenance that is mainly re-
lated to autonomous robots charging. A minimal run-
time for a charged robot is about two hours, which is
derived from the duration of regular course lab. Many
safety issues have to be solved as well, guaranteeing
any part of the system cannot be damaged as a result
of unexpected user action or internal failure.
3 ROBOTS
At the beginning of the SyRoTek project, several
available robotic platforms were discussed whether
they are applicable and meet identified requirements
of the project needs. Many robots were rejected due
to their size over 20 cm in diameter. Smaller robots
mostly did not meet desired sensor equipment or had
very poor options for extensions.
The most critical feature considered in the plat-
forms evaluation is mechanism of the robot charging.
All available robots considered are recharged with hu-
man attendance that would result in the need to adjust
robot for automatic recharge. Considering the amount
of necessary modifications of the considered robots in
combination with its price, we have decided to design
and manufacture a robot to serve our needs. The de-
veloped S1R robot is described in this section.
The most important component of the robot, influ-
encing its design, are batteries and motors. Lithium-
Polymer rechargeable cells were selected for the best
trade-off between capacity and size. Required opera-
tion time on batteries results in need of about 50 Wh
battery capacity. Monitoring of each cell individually
is necessary during the charging of the lithium based
battery, therefore a charger circuit has been embedded
into the robot body.
Two Faulhaber 2224 motors with integrated gear-
box and IRC encoder have been selected to meet the
required differential kinematics. Two driven wheels
are mounted directly to the motor gearbox axes. Outer
casing of the chassis is a bumper of octagonal shape
with rounded corners, as shown in Fig. 2.
On the top of the chassis, electronic modules are
mounted. Three main electronic boards are
• power control and charger board (power board),
• motor control and sensor data acquisition board
(control board) and
• on-board computer interface board with on-board
computer (OBC) mounted on.
A TECHNICAL SOLUTION OF A ROBOTIC E-LEARNING SYSTEM IN THE SYROTEK PROJECT
413