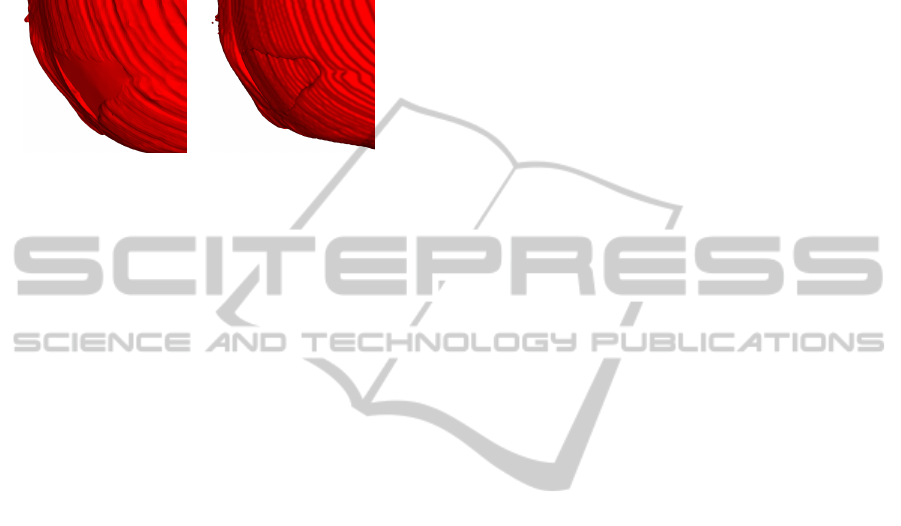
sented on the third column of Table 3, for the top sur-
face. All the reported distances are higher than the
ones reported by our technique which indicates that
we can better recover the curvature of the region. This
fact is also confirmed by the distance field pictured on
Figure 9.(c).
(a) (b)
Figure 10: (a) Viewpoints of the solution obtained by the
method described in (You et al., 2009). (b) A viewpoint of
the prosthesis generated by our technique.
4 CONCLUSIONS AND FUTURE
WORKS
Based on a deformable model, a method is proposed
to reconstruct the defective position of a skull. The
goal is to construct the prosthesis model for the defec-
tive region. We show a promising result and compare
our technique with a state-of-the-art one, showing that
our method can generate a more suitable prosthesis
geometry.
Future directions for our work are to improve the
method that obtain the boundary conditions (avoid-
ing the problem pictured on Figure 7). We also plan
to test and compare the approach with other available
techniques (Hu et al., 2007; Lin et al., 2008). Besides,
we intend to apply a 3D deformable model, using D-
NURBS (Qin and Terzopoulos, 1996), to get the pros-
thesis geometry. It could address the staircase defect
generated by the slice-by-slice strategy and generate
more smooth patches.
ACKNOWLEDGEMENTS
Authors would like to thank the support provided by
CNPq, CAPES (grant 094/2007) and FAPERJ (grant
E-26/170.030/2008).
REFERENCES
Chen, J.-J., Liu, W., Li, M.-Z., and Wang, C.-T. (2006).
Digital manufacture of titanium prosthesis for cranio-
plasty. The International Journal of Advanced Manu-
facturing Technology, 27(11-12):1148–1152.
Cohen, L. D. (1991). On active contour models and bal-
loons. CVGIP:Image Understanding, 53(2):211–218.
Hu, Q., Yang, H., and Yao, Y. (2007). A software method to
model and fabricate the defective bone repair bioscaf-
fold using in tissue engineering. In Li, K., Li, X.,
Irwin, G., and He, G., editors, Life System Model-
ing and Simulation, volume 4689 of Lecture Notes in
Computer Science, pages 445–452. Springer Berlin /
Heidelberg.
Kai, C. C., Meng, C. S., Ching, L. S., Hoe, E. K., and
Fah, L. K. (2009). Cranioplasty using polymethyl
methacrylate prostheses. Journal of Clinical Neuro-
science, 16(1):56–63.
Lee, M.-Y., Chang, C.-C., Lin, C.-C., Lo, L.-J., and Chen,
Y.-R. (2002). Custom implant design for patients with
cranial defects. Engineering in Medicine and Biology
Magazine, IEEE, 21(2):38–44.
Lee, S.-C., Wu, C.-T., Lee, S.-T., and Chen, P.-J. (2009).
Cranioplasty using polymethyl methacrylate prosthe-
ses. Journal of Clinical Neuroscience, 16(1):56–63.
Lin, L., Zhang, J., and Fang, M. (2008). Modelling the bio-
scaffold for repairing symmetrical and unsymmetrical
defective skull. In Bioinformatics and Biomedical En-
gineering, 2008. ICBBE 2008. The 2nd International
Conference on, pages 905–908.
Qin, H. and Terzopoulos, D. (1996). D-nurbs: a physics-
based framework for geometric design. Visualiza-
tion and Computer Graphics, IEEE Transactions on,
2(1):85 –96.
Sanan, A. M. and Haines, S. J. M. (1997). Repairing holes
in the head: A history of cranioplasty. Neurosurgery,
40(3):588–603.
Solaro, P., Pierangeli, E., Pizzoni, C., Boffi, P., Scalese,
G., Di Lorenzo, N., and Pirillo, V. (2008). From
computerized tomography data processing to rapid
manufacturing of custom-made prostheses for cran-
ioplasty: Case report. Journal of Neurosurgical Sci-
ences, 52(4):113–116.
You, F., Hu, Q., Yao, Y., and Lu, Q. (2009). A new modeling
method on skull defect repair. Measuring Technology
and Mechatronics Automation, 2009. ICMTMA ’09.
International Conference on, 1(11-12):568–572.
VISAPP 2011 - International Conference on Computer Vision Theory and Applications
142