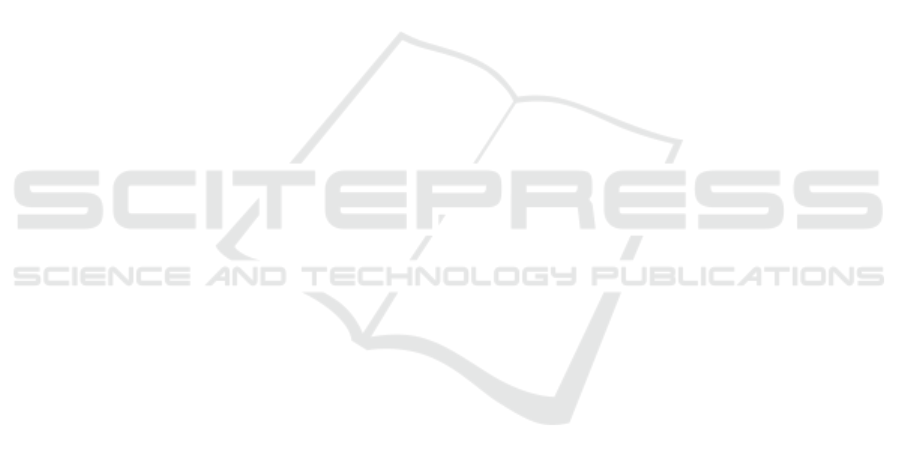
INTRODUCING A NEW HALL EFFECT SENSOR
Novel Dynamic Offset Reduction Method
Vlassis N. Petoussis, Panos Dimitropoulos, George Stamoulis and Elias Houstis
University of Thessaly, Department of Computer & Communication Engineering
37th Glavani & 28th October Str., Volos, Greece
Keywords: Hall effect sensor, Offset reduction.
Abstract: Silicon Hall plates show an offset of a few millitesla. A large portion of this offset is caused by mechanical
stress in the device. The offset can be reduced when the spinning - current principle is applied. In this paper
we present a model and numerical analysis of a new Hall effect sensor which using a novel offset reduction
method. We call it “Wheel Hall Senor” and senses all 3 filed dimensions. The flux-density of B
Z
is
proportional to the DC component of the output signal, whereas the B
X
and B
Y
components are proportional
to the first harmonic of the output signal. Furthermore we calculate the function which governs the changes
in the electric field inside the new Hall effect sensor in presence of magnetic field. This function help us to
control in MatLab environment the equipotential lines and to monitor the changes in biasing conditions.
About the new sensor, the combination of his pioneering form and the elaborate sequence of using the
dynamic spinning current technique, could be lead to satisfactory results of produced Hall voltage with
small noise in a presence of external magnetic field.
1 INTRODUCTION
Hall plates are used in a wide variety of applications
to measure static and dynamic magnetic fields. A
major drawback of these sensors is their high offset
voltage, i.e., an output signal in the absence of a
magnetic induction. According to (A. Bellekom,
1994) the effects which contribute to the offset
voltage are piezoresistive effects, geometrical errors,
temperature gradients, nonhomogeneities, etc.
However, the offset voltage with a spatially periodic
nature differs from the Hall voltage, which is
constant. One way to reduce the offset caused by
orthogonal asymmetries is to use coupled symmetric
Hall plates (Maupin, 1980). However, the offset can
never be completely cancelled because there will
always be small differences between the Hall
devices. To overcome the mismatch, the bias current
of a single four contact Hall device is spun by
contact commutating and the resulting output
voltages are averaged over time. The orientation
dependence of the offset sources in silicon suggests
that orthogonal switching is not sufficient. To cancel
components of higher asymmetries a multicontact
Hall plate with more than four terminals is
necessary. The method presented in this paper is
based on Hall device with sixteen outside and
sixteen inside contacts. The spinning current vector
is generated by two harmonic biasing currents. As a
result, the output signal becomes spatially
continuously accessible, hence, asymmetries of
higher order can be cancelled out. Aim of present
work is the presentation of new Hall sensor with
pioneering form that reminds cogwheel with two
lines teeth, one internally and one externally (for this
reason we name it “Wheel Hall Sensor”) but also
with different way in the cancellation of offset
voltage and finally 1/f noise rejection. Initially the
designing constituted fundamental objective that as
aim had the respect and compatibility in the existing
techniques of reduction 1/f noise and also offset
voltage. For this aim was selected the circular
structure.
2 OFFSET VOLTAGE
In a standard IC process Hall plates have the
advantage of cheap and small. Therefore they are
quite often used in applications where the permanent
magnet is combined with the sensor. Because Hall
plates show a large offset the magnet used in these
464
Petoussis V., Dimitropoulos P., Stamoulis G. and Houstis E..
INTRODUCING A NEW HALL EFFECT SENSOR - Novel Dynamic Offset Reduction Method.
DOI: 10.5220/0003397304640469
In Proceedings of the 1st International Conference on Pervasive and Embedded Computing and Communication Systems (PECCS-2011), pages
464-469
ISBN: 978-989-8425-48-5
Copyright
c
2011 SCITEPRESS (Science and Technology Publications, Lda.)