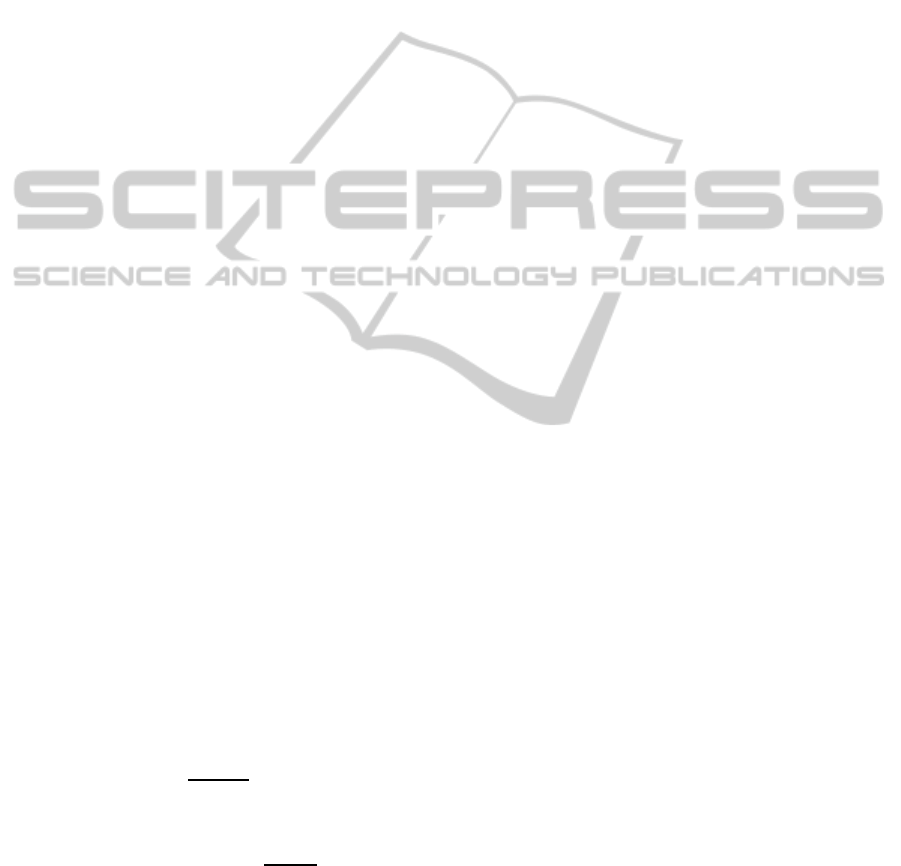
mass flow distribution are not aggregated for optimal
operation. Hydraulic balancing of the heating sys-
tems is often used to achieve more efficient heat dis-
tribution. There are still about 90% of all operated
systems, where such measures have not been con-
ducted (Guzek, 2010) and (Szendrei, 2010). Stan-
dard procedures of hydraulic balancing cover hydro-
static adjustments for heating loads under extreme cir-
cumstances (full load). In this condition, the proper
mass flow distribution can be obtained throughout the
system by adjusting proper resistance at the heating
valves (forward-motion pipe). Alternatively, resistors
are inserted in the backward-motion pipe of the dis-
tribution system. This adjustment is legally forced by
the DIN 18380 requirements. More realistic load pro-
files have to cover partial heating scenarios. In these
cases, that occur throughout 95% of the heating sea-
son, significantly smaller mass flows have to be cir-
culated by the distribution system. Besides meteoro-
logic influence, the mass flow is object to dynamic
user settings (R.Yao and Steemers, 2005). That way,
the statically adjusted resistances are out of tolerance
and do not ensure homogeneous mass flows. The ef-
fects of imbalanced working conditions are:
Thermal/Comfort Effects: delayed heat-up of
rooms/dwelling, flow noises, declined control
quality of thv;
Efficiency Effects: increased energy demand, in-
creasing backward-motion water temperatures,
rising operating expenses, decreasing system
durability.
In order to achieve adequate hydraulic conditions,
the control system for space heating can be used.
To anticipate the hydraulic interferences between the
dwellings, it is essential to control the mass flow of
each mesh that supplies different heating devices over
the storeys. Therefore, the configuration of the KNX-
network must consider the systems installation of ris-
ing pipes and its attached devices. So far, mass flow
specifications regarded the entire pipe setup within a
closed heating system according to:
˙m =
∑
˙
Q
c
p
· △ϑ
(2)
and
△p =
∑
(R·l)+
∑
(ζ·
ν
2
· ρ
m
2
) (3)
Since smaller pipe sections are more simple to con-
trol and to calculate, such entire systems can be seg-
mented into meshes. Each rising pipe, supplying the
above storeys/rooms with water, may represent a sin-
gle mesh. At the main distributing pipe, a difference
pressure controler disconnects the meshes from the
hydraulic mainframe. The calculations and condi-
tions follow the shown procedures from equations 2
and 3.
2.2 KNX-based Building Services in
Space Heating
With these information, different load scenarios can
be modelled. A dynamic control within the given
structure with independent hydraulic mesh conditions
is enabled. Because of reducing the number of at-
tached heating valves, the mass flow conditions are
to be assumed more effectively. Thus, possible load
scenarios can be modelled and deposited for facility
server applications. According to heating demand in
the meshes, valve ranges can be tuned in to dynami-
cally balance the meshes mass flow and ensuring ad-
equate heat supply. The advantage of this approach
is the coverage of static and dynamic load profiles.
In general, heating valves in lower storeys require a
higher hydrostatic resistance (bigger valve range). In
accordance with the number of storeys, the necessary
resistance is to be decreased. The implementation of
this control requires accurately working valve drivers.
These are to be found among KNX-based, continu-
ously controlled drivers.
As demonstration and try-out objects, two multi-
storey residential buildings have been equipped with
KNX-based actors and sensors. Applications of
heating control, electric appliance control, protec-
tion/security control and others are installed. Besides
control procedures, the KNX-network enables visu-
alisation, remote operations, flexible billing and in-
dividual setups of the installed components (T. Teich,
M. Zimmermann, S. Franke, F. Janh and M. Schrader,
2010). In the field of heating control, the existing
building service hardware (i.e. heating devices, pipes,
heat generator) did not have to be renewed. The func-
tionality of heat generation and distribution hardware
was available for restarting it with KNX-based valve
drivers. Thus, integrative control procedures of room
temperature and heat generator settings are enabled
throughout the building. The valve drivers are ad-
dressable, continuously controllable units with a to-
tal range of 3 millimetres, that replaced the exist-
ing thermostatic valves. With such drivers, conven-
tional valve-cores became easy to control. Inside the
buildings, the equipment is linked via Ethernet. The
communication between facilities is transacted over
VPNs. Those provide a private communications net-
work over a shared public network infrastructure such
as the Internet. Basically, there are three types of
virtual private networks: Remote access VPN con-
nection (end-to-site), Branch Office VPN connection
HYDRAULIC BALANCE IN SMART HOMES - Using The KNX-standard for Performing Balanced Heating Conditions
in Dynamic Load Situations
383