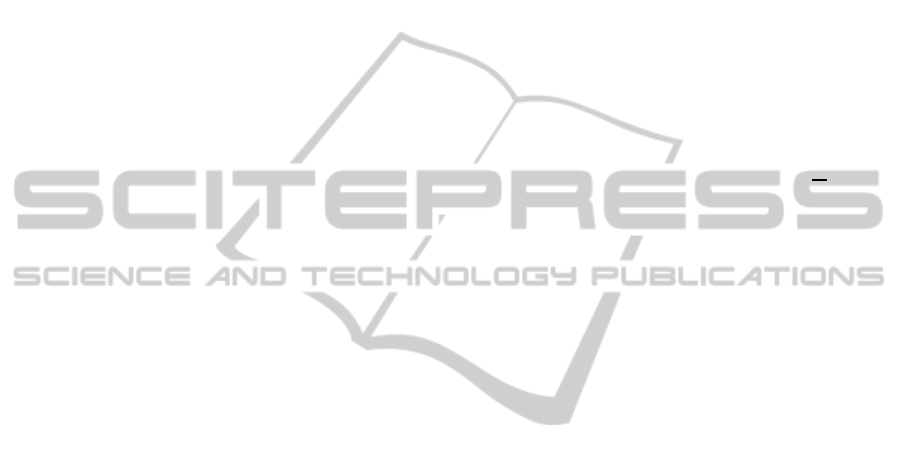
setting since the cycle times depend on the allocation
of the operations. Tool life has a number of implica-
tions in the current problem setting as well: Contin-
uing to use a tool even after its life is over results in
quality problems and, thus, the tools must be replaced
before their lives end. On the other hand, replacing a
tool before its life is over increases the tooling cost.
Additionally, the life of a tool may end at a time in-
stance when the assembly line is supposed to be op-
erating and therefore may result in line stoppages. In
order to overcome this problem, we aim to design the
line so that the tools are changed in periods of un-
availability in which the line is already not operating.
At each break, if there exist welding tools that have
a remaining number of spot welds less than the total
number of spot welds that they have to perform until
the next break, they must be replaced with new ones.
With such an operating rule and by assigning the op-
erations to the stations considering not only the cycle
times but also the tool usage rates at each station, we
prove that the total profit can be increased.
The design problem that we study in this paper is
originated from a project that we conducted for one
of the leading automotive manufacturing companies
in Turkey. One of the important aspects of any design
problem is the operational problems that can be faced
during the actual implementation of the design. We
first investigated the existing automotive body com-
ponent robotic spot welding assembly line, where the
line is fully automated to produce two models in any
order. In that project, our aim was to develop a tool
change decision policy for the assembly line where
there was no systematic approach for scheduling the
tool change periods. All of the tools were being re-
placed just at the end of their lives. As a consequence,
the line was stopped regularly for tool changes. The
company has allocated almost 10% of their available
capacity to the line stoppages due to tool changes.
This is the main reason why we study line design
and operation allocation problems together with the
scheduling of tool change periods in this study.
2 PROBLEM DEFINITION
We consider an assembly line that contains at most
m stations: S
j
, j ∈ M={1, 2,. .., m}. Space restric-
tions in the production area and a limited budget for
investment costs are among the reasons of such a re-
striction on the number of stations. We use parameter
V
j
to denote the cost of setting up S
j
. There are g dif-
ferent models to be produced in this robotic assembly
line. O
hi
represents operation i of a part of model h;
i ∈ N
h
= {1, 2, . . . , n
h
}, h ∈ G = {1, 2, . . . , g}. A num-
ber of spot welds are grouped together to form an op-
eration. The selection is based on the closeness of
the welds to each other and to satisfy the proper ge-
ometry of the assembled components. Let W
hi
be the
number of spot welds required to perform operation i
on model h. The total number of spot welds that the
welding tool in S
j
can process before its life is over is
denoted by B
j
.
Factors that affect the number of stations to be
installed are the target cycle time, the station invest-
ment cost, and the tooling cost. Let us represent the
yearly expected demand for the parts to be produced
as θ
h
. We use the parameter γ
h
to denote the target
cycle time for model h to meet the yearly expected
demand θ
h
. In general, let T
h
be the total time allo-
cated for production of model h; f
h
the actual cycle
time of model h; and
b
θ
h
the corresponding production
quantity. Then, we have the following:
b
θ
h
=
T
h
f
h
∀h.
Producing model h less than a specified quantity is
not acceptable. Let this specified quantity be denoted
by θ
U
h
and the corresponding cycle time be denoted by
γ
U
h
, which specifies an upper bound on the cycle time.
Additionally, if production exceeds a certain quantity
for each model, it is not possible to make any addi-
tional profit. Let this production level be denoted by
θ
L
h
and the corresponding cycle time lower bound be
denoted by γ
L
h
. Clearly, we have θ
U
h
≤ θ
h
≤ θ
L
h
. Ad-
ditionally, the individual profit gained from model h
is assumed to be a piecewise linear function. It is de-
noted by PR
h
for
b
θ
h
≤ θ
h
. On the other hand, if the ac-
tual production amount of model h exceeds the yearly
demand of θ
h
so that θ
h
<
b
θ
h
≤ θ
L
h
, then the profit
for each model h produced as surplus is PR
ε
h
, where
PR
ε
h
= PR
h
− ∆
h
, 0 ≤ ∆
h
≤ PR
h
, where ∆
h
denotes
the reduction in the individual profit for the excess
parts when the production exceeds the expected de-
mand. As a consequence, the individual profits from
each model h is a two-piece linear function where the
slope of the second piece is less than that of first piece.
In this study, we consider the tool change periods
as a decision variable. If the tools are only changed
at scheduled breaks as we propose, the line will never
stop for a tool change, which increases the throughput
rate, but on the other hand, some tools will be changed
before their lifetime ends. Therefore, the tooling cost
will be increased. As a result, one aim of the current
study is to determine the best solution that balances
the increased tooling cost with the increased through-
put rate. Let C
j
be the cost of the tools in S
j
. We as-
sume there are q = 1, 2, . . . ,U, total number of breaks
in the planning horizon. We also need the following
decision variable:
z
jq
= Binary variable indicating whether tools in S
j
are changed in tool change period q or not.
ICINCO 2011 - 8th International Conference on Informatics in Control, Automation and Robotics
388