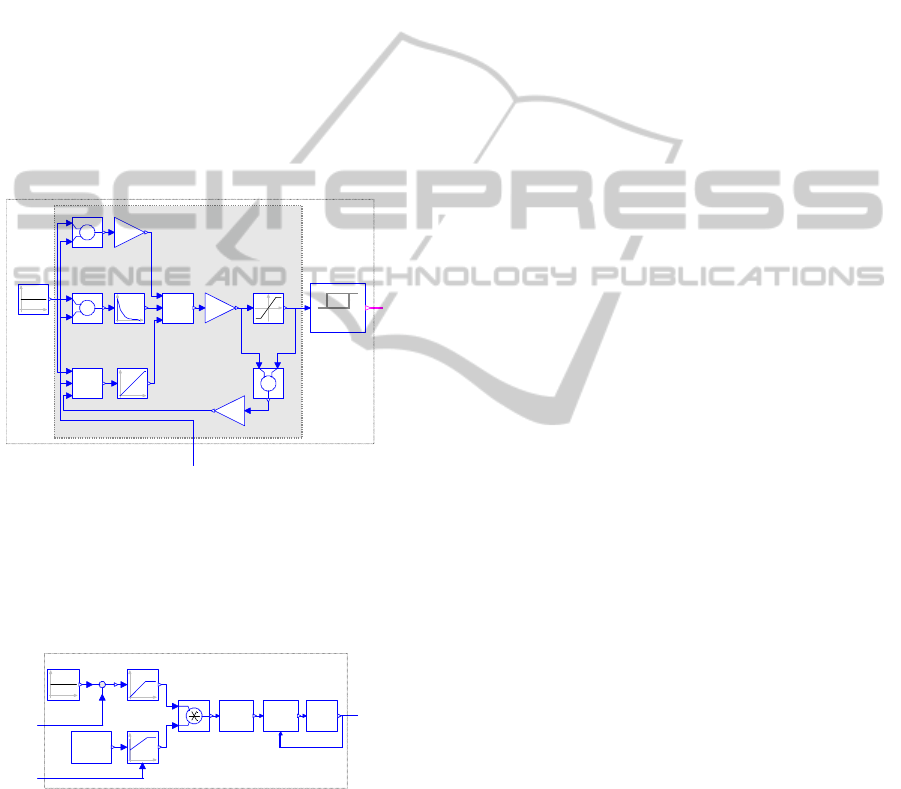
used by the controller to increase the pumping rate.
However, this has an impact on the aggregated
amount of extracted water. Due to this consequence,
it has been decided to ignore low pressure events so
as to encourage farmers to obey the planned
irrigation schedule.
The filling process controller is based on a PID
controller with limited output, anti-windup
compensation and set point weighting as illustrated
in Figure 11 (Astrom, 1995). This PID controller is
available in the Modelica standard library. The
controller is tuned and its output is limited to the
range [0, 25]. The analog output is quantized taking
into account a sufficient hysteresis value (0.4) to
prevent possible oscillations. The resultant number
specifies the required number of running wells. One
should mention that this number is limited to 25 in
order to leave 2 wells as standby.
Figure 11: Filling process controller.
On the other hand, the distribution process has
10 speed-controlled boosters and the maximum
capacity is limited to 8, leaving 2 as standby. The
simulated controller of this process is shown in
Figure 12.
Figure 12: Distribution process controller.
The lower part of the controller has a PID
module with limited output, anti-windup
compensation and set point weighting. Its output
specifies the required pumping capacity which has a
minimum of 0 when all pumps are off and a
maximum of 8·2900 when 8 booster pumps run at
their full speed. The upper part has an integrator
with a limited output [0,1]. In regular cases, the error
signal is positive and the integrator saturates to unity
value. Once the pressure exceeds the specified
threshold (P
th
≈98% of the maximum permissible
pressure), the integrator output starts to decrease and
eventually saturates to 0. This gives a measure for
the persistence of the pressure to exceed the
threshold value. The result of this integrator is
multiplied with the output of the Limited PID
module to generate the recommended pumping
capacity. The distributer module uses this value to
generate the reference speeds for the boosters. In
order to maximize efficiency, only one booster
pump may be assigned a partial load while all others
that share the pumping load must be assigned the
rated speed. The sequencer block regulates the
starting and shutting operations of the boosters. In
order to protect the hydraulic system from water
hummer effects and also to protect the power system
from electrical surges, booster pumps are allowed to
enter or leave operation only one after another.
Having a feedback from the Variable Frequency
Drives (VFD) of the motors, the sequencer is able to
manage that task. The VFD is modeled by a first-
order block with a time constant of 5 s resulting in
an acceleration time of about half a minute to move
forward or backward between zero speed and rated
speed states.
The most important simulation outputs are
shown in Figure 13. The tank’s water level (L) is
depicted in Figure 13a. As intended, the tank starts
at full state in the morning and the controller
returned it back to that state at the end of day. The
number of running pumps, which is shown in Figure
13b, demonstrates how pumps are called for running
when the error signal (deviation from the tank full
state) and its derivative is high in the morning. Later
in the afternoon, supplied water is less than collected
water, and thus the water level in the tank starts to
increase. Consequently, the controller decreases the
number of running pumps. Figure 13c shows the
demanded flow, the scheduled supply flow, and the
supplied flow (Q). The test data is designed to
explore the controller behavior when there is a large
mismatch between demand and scheduled supply.
During the first half of the day, there is excessive
demand and the controller supplies the planned
quantity. In contrast, during the second half of the
day, demand is much less than the scheduled supply.
The controller delivers excess flow to the extent that
pressure (P) at the network does not exceed the safe
limit as illustrated in Figure 13d. Finally, Figure 13e
shows how 6 booster pumps share the pumping load
of that day. At any given time, the controller adjusts
LimPID
L
u
tank's water level
limiter
uMax={25}
limiter
addP
-1
wp
addP
+
wp
-1
addD
-1
wd
addD
+
wd
-1
k={1}
P
I
I
k={16000}
D
k={5000}
k={12}
gainPID
addPID
+1
+1
+1
+
addI
+1
-1
+1
+
addSat
-1
+1
addSat
+
+1
-1
k={0.093}
gainTrack
Quantizer
Setpoint
k={4.9}
P
actual supply flow
speed vector
s
Q
limPID
PID
-
feedback
product
LimIntegrator
I
k={1e-5}
sequenc er
distributer
VFD
Pt h
k={10.8e5}
Supply
Schedualed
ICINCO 2011 - 8th International Conference on Informatics in Control, Automation and Robotics
328