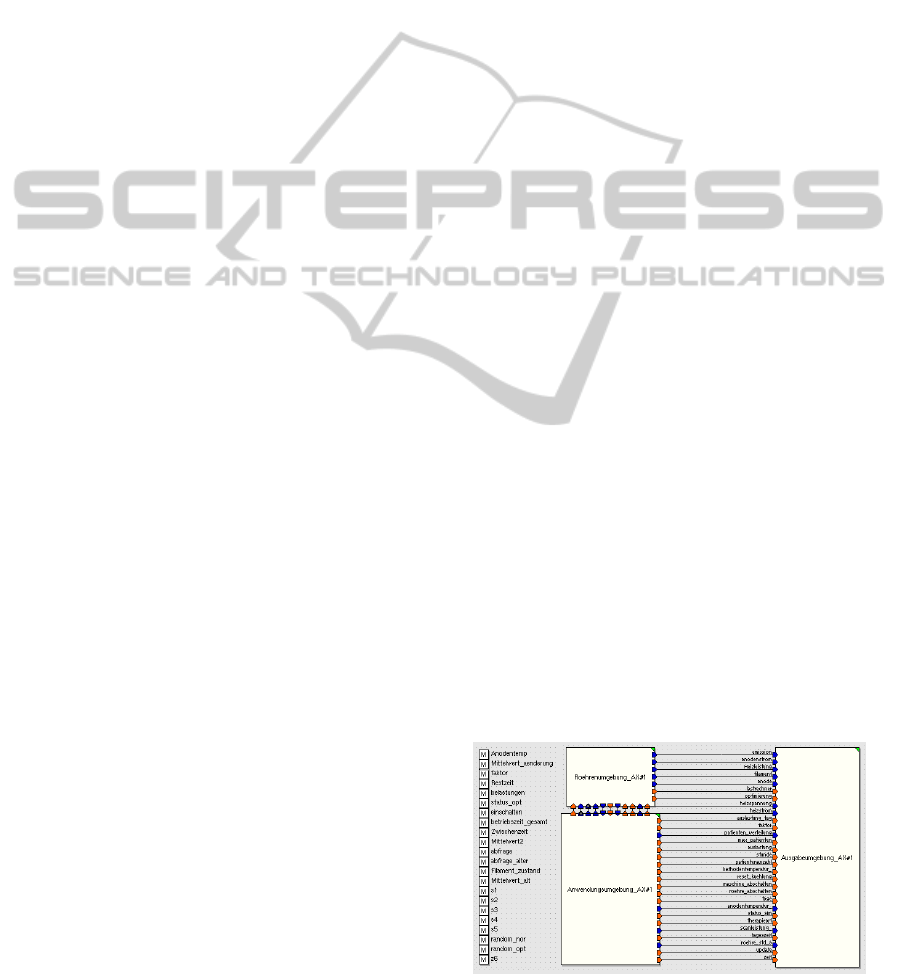
incidents. This is why, in so called unavoidable
circumstances, one would like to have at least a big
enough lead time, to ensure the exchange can be
made before there is a downtime of a system.
3 SIMULATION
The hospital-specific diagnostic and treatment
requirements are implemented into the simulation
environment. The daily routine of a clinic is
considered in the simulation, as well as a statistically
spread patient number, the load profile given by
logging files recorded over months will give all
necessary operating points. In a first step, manually
selected load profiles are used, the interface for on-
site recorded load profiles (.tua files = tube history
records) is in work.
Particularly interesting is the implementation of
the "optimization". The calculation of residual life is
based on the fact that all calculated life-critical
values are afflicted with an error reflected from
practise of about + -15%. This is due to
manufacturing tolerances of the tube and its
environmental factors. The thermal balance
calculated with the knowledge of the geometries and
materials does not show the correct value for the
surface temperature of the anode plate or the cathode
surface. The "optimization" deals with the
simulation exactly as before, but with a smaller
error: + -2%. This error is the assumed total residual
error of the measurement chain (pyrometer,
operational amplifiers, AD-converter) to measure
the surface temperature (Heuermann, 2010).
Creating a discrete event simulation, which is
extended and detailed as well as driven by real load
profiles from customer sites, enables reliable
investigations. The work has shown that
MLDesigner (MLDesign Technologies, Inc. 2007) is
the right tool for the reconstruction of the technically
physical processes within a medical system.
MLDesigner offers the possibility to use Markov-
Chains for the network theorem based system
(queuing networks with parallel and serial service
units) and probability tools like Poisson-distribution
as well as random generators for the patient arrivals.
During observation, it soon becomes clear that
the topic is a classic optimization problem. It is a
balancing act between maximized service life (carry
out the exchange as late as possible), and realizing
the avoidance of potential downtime. A statement of
this quality on the life of a high-performance tube
can not be given to this day in a satisfactory manner.
The existing studies and investigations are only
estimates and approaches. The complex relation-
ships and calculations within such a tube are seen
analyzed and evaluated from the outside of the tube
(Wippler, 2009, Heuermann, 2006).
The underlying research work pursues a
fundamentally new approach. This means a direct
view on the processes within the tube, instead of just
estimating. This allows examining the condition of
the tube much more in detail, with the result that the
statements on the processes are significantly more
related to reality.
A simple example is the surface temperature of
the cathode. So far, the temperature is calculated
according to complex procedures. Despite all
precision and complexity of observation, the result is
still estimation. The idea of the research works
however is just to measure the surface temperature
of the cathode. Thus, it is possible to respond to
changes almost immediately. The model to be
developed will shed light on whether it is precisely
this optimization, that will be prove decisive for the
substantial extension of the economic life of a high
power tube.
The realization of this comparison is carried out
by two simulation models. The basic model
corresponds to the current usage of high power
tubes, ie without any optimizations. Based on that
first developed basic model, a model extension is
designed. This serves a direct comparison between
the basic and extended model. These extensions
include the optimizations as discussed. Thereafter,
the data of the two simulation runs can be compared.
With the optimization, a service life extension
should be observed under normal circumstances. In
the simulation a very flexible block structure was
realized: An adaptive application environment (rep.-
rates, cathode/anode current, filament power,
patients/h etc.), a flexible exchangeable tube model
block and a load block which reflects the required
energy (e.g. 23MV, 21MeV, 160keV ect.) within an
individual diagnostic- or treatmentplan was
developed (Heuermann, 2007, 2010).
Figure 6: Encapsulated simulation environment for
angiography.
SIMULTECH 2011 - 1st International Conference on Simulation and Modeling Methodologies, Technologies and
Applications
398